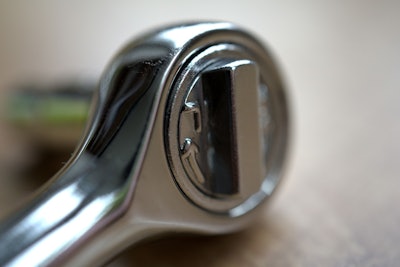
Maintaining your feed facility is crucial for operational efficiency and product quality. A well-crafted maintenance plan is key to keeping your equipment running smoothly, preventing costly breakdowns, and ensuring your facility meets safety standards. By implementing a proactive approach to maintenance, you can boost productivity, extend the life of your machinery, and maintain a safe working environment for your staff.
To create an effective maintenance plan for your feed facility, you'll need to assess your current condition, set priorities, and develop preventive maintenance schedules. This article will guide you through the process of building a comprehensive maintenance strategy, from initial evaluation to implementation and monitoring. You'll learn how to streamline your maintenance efforts, improve record-keeping, and train your team to handle maintenance tasks efficiently. By following these steps, you'll be on your way to a more reliable and productive feed facility.
Assess current facility condition
To create an effective maintenance plan for your feed facility, you need to start by assessing its current condition. This crucial step provides a comprehensive snapshot of your facility's health, helping you understand what's working well and what needs attention. By conducting a thorough inspection, documenting your equipment and asset inventory, and identifying critical systems, you'll lay the foundation for a proactive maintenance strategy.
Begin by performing a systematic walkthrough of your facility. Examine each area and component to identify visible signs of damage, deterioration, or deficiencies. Use checklists, measurement devices, and cameras to record data on the condition, functionality, and performance of various systems and equipment. Pay close attention to the building envelope, mechanical systems, electrical systems, and safety features. Document your findings with detailed notes and photographs to create a clear picture of your facility's current state.
Creating a comprehensive inventory of your facility's assets is essential for effective maintenance management. Develop a centralized asset repository that includes information such as equipment specifications, warranty details, and maintenance history. This inventory will help you streamline maintenance scheduling, claim warranties, and make informed decisions about asset upgrades or replacements. Consider using asset tracking software to maintain an up-to-date record of your equipment's location, condition, and usage.
Prioritize your facility's assets based on their importance to your operations. Categorize equipment into groups such as life safety, critical, and non-critical. This classification will help you allocate maintenance resources effectively and ensure that essential systems receive the attention they need. Focus on identifying systems that are crucial for maintaining product quality, safety standards, and operational efficiency in your feed facility.
Establish maintenance priorities
After assessing your facility's condition, the next step in creating a maintenance plan is to establish priorities. This process involves categorizing equipment, determining maintenance frequency, and setting performance standards.
To optimize your maintenance strategy, you need to prioritize your equipment based on its criticality to operations. Start by creating a system that classifies assets into different levels of importance. For example, you might use categories such as critical, essential, and non-essential. This classification helps you allocate resources effectively and ensures that the most crucial systems receive the attention they need.
Consider factors such as the impact on production, safety risks, and potential downtime costs when categorizing your equipment. By focusing on the most critical assets first, you can minimize the risk of unexpected breakdowns and maintain operational efficiency.
Once you've categorized your equipment, it's time to establish how often each asset should be maintained. The goal is to strike a balance between preventing breakdowns and avoiding excessive maintenance. A common rule of thumb is to set the inspection frequency to roughly half the failure developing period (FDP).
However, determining the optimal maintenance frequency isn't always straightforward. Consider factors such as manufacturer recommendations, equipment usage patterns, and historical performance data. Remember that maintenance frequency may need adjustment over time as you gather more data and experience with your equipment.
To ensure your maintenance plan is effective, it's crucial to establish clear performance standards for each piece of equipment. These standards serve as benchmarks for evaluating the success of your maintenance efforts and help identify areas for improvement.
Define specific, measurable targets for key performance indicators such as equipment uptime, mean time between failures, and maintenance costs. By setting these standards, you create a framework for continuous improvement and can make data-driven decisions to optimize your maintenance strategy.
Develop preventive maintenance schedules
To create an effective maintenance plan, you need to develop preventive maintenance schedules. This crucial step helps you streamline your maintenance efforts and improve operational efficiency. By implementing a proactive approach, you can minimize equipment downtime and extend the lifespan of your assets.
Start by creating comprehensive task lists for each piece of equipment in your feed facility. These lists should include specific inspection, servicing, and maintenance tasks based on manufacturer recommendations and historical data. Prioritize tasks according to their importance, considering factors such as asset criticality, safety risks, and operational impact. This approach ensures that your maintenance staff focuses on high-impact tasks first, minimizing downtime risks and maintaining operational continuity.
Once you've created task lists, it's time to assign responsibilities to your maintenance team. Designate specific employees or teams to complete each maintenance task, taking into account their skill levels and scheduling constraints. This clear delineation of tasks ensures that everyone understands their responsibilities and timelines, reducing misunderstandings and neglected maintenance duties.
Establish a maintenance calendar to schedule recurring work orders and track task completion. Utilize a computerized maintenance management system (CMMS) or specialized maintenance management software to streamline scheduling, monitor tasks, and analyze trends for informed decision-making. This approach helps you maintain backlogs, track inventory, and measure important metrics like planned maintenance percentage (PMP) and preventive maintenance compliance (PMC).
Implement and monitor the plan
To create an effective maintenance plan, you need to put it into action and keep a close eye on its progress. This involves training your staff, using specialized software, and regularly reviewing your strategy.
Investing in your maintenance team is crucial for keeping your facility running smoothly. By providing comprehensive training, you can empower your staff to handle various maintenance tasks efficiently. Focus on both technical skills and safety requirements, such as OSHA regulations and lockout/tagout procedures. Consider offering certifications in specific areas like thermography and ultrasound to enhance your team's expertise.
Implementing a Computerized Maintenance Management System (CMMS) is essential for streamlining your maintenance operations. A CMMS helps you organize work orders, schedule preventive maintenance, and manage inventory. It provides a centralized platform for tracking maintenance activities, equipment performance, and resource allocation. By using CMMS software, you can improve efficiency, reduce human error, and make data-driven decisions.
To ensure your maintenance plan remains effective, it's crucial to review and update it regularly. Monitor key performance indicators such as planned maintenance percentage and mean time between failures to assess the success of your strategy. Use these metrics to identify areas for improvement and adjust your plan accordingly. By continuously evaluating and refining your approach, you can optimize your maintenance efforts and achieve long-term operational success.
Crafting a solid maintenance plan for your feed facility is a game-changer to boost productivity and ensure safety. By taking a close look at your current setup, setting clear priorities, and creating preventive maintenance schedules, you're setting yourself up for success. This approach helps you stay on top of potential issues, extend the life of your equipment, and keep your facility running smoothly.
Remember, a good maintenance plan is an ongoing process. It's crucial to keep training your staff, use the right tools like CMMS software, and regularly review your strategy. By staying proactive and adaptable, you'll be able to tackle challenges head-on and keep your feed facility in top shape. In the end, your efforts will pay off with a more efficient, safer, and more productive operation.