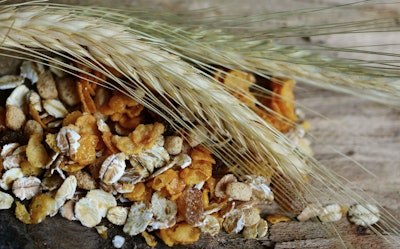
Grinding cereals to be mixed into feeds for animals is the second most energy consuming operation in any feed mill. That is, assuming the feed mill also pellets said feed and not just the occasional one. If no pellet mill exists, then the grinder — be it a hammer or a roller mill — becomes the most expensive item on the electricity/energy bill. It is thus only reasonable to have to address numerous questions about grinders during times when uncertainty and high electricity prices are in the daily news. The following review is offered for discussion toward deciding the optimal grinding size.
Grinding to reduce particle size of raw materials is accomplished by roller or hammermills. Roller mills use a combination of compact and shearing forces to produce particles of uniform size, but irregular shape. Hammermills use impact force to shatter material into particles of variable yet spherical size. Because of differences in physical characteristics, rolled ingredients are easier to handle as they flow better than ingredients ground with hammermills.
Roller mills are usually more expensive to install and maintain, but less demanding in energy inputs compared to hammermills. Because roller mills require less energy to achieve the same particle size than hammermills, they do not overheat processed ingredients reducing, thus, moisture loss (i.e., shrink). It has been reported that temperature increases of 2º to 6o C are common during hammermilling of corn.
But, hamme mills provide more flexibility in the type of materials they can process, and they are also capable of reducing particle size further than most roller mills. In general, it is accepted that in most feed applications, which require a particle size reduction between 600 and 800 microns, roller mills reduce milling cost in terms of throughput per unit of energy, but this advantage is rapidly lost as particle size falls below 500 microns. Of course, these are generalizations as specific brands of either type of grinder can offer disparate results.
Can mill type impact digestibility?
It is often argued that the type of milling may also affect animal performance because of potential differences in nutrient digestibility. It is suggested that the spherical shape of hammermilled ingredients inhibits enzyme penetration, and thus, reduces nutrient digestibility. Studies with growing pigs at Kansas State University (KSU) revealed that digestibility of organic matter, protein, and energy in pigs was increased by about 5% when corn was ground by a roller mill compared to corn ground by a hammermill. Differences in nutrient digestibility caused by mill type diminished as particle size was reduced from 800 to 400 microns, and this effect was not associated with variation in particle size giving credence to the notion of enzyme access.
Degree of fineness in ground material appears to have a more dramatic effect on nutrient digestibility and animal performance. It is well documented that a finer particle size improves performance in young pigs. Studies with oats and barley indicated that finely ground cereals improved feed efficiency and rate of gain in weaned pigs. Similar improvements in performance were observed with corn, wheat, and sorghum.
All of the above studies were conducted again at KSU. It is speculated that as particle size decreases the surface available for enzymatic digestion increases, whereas increased fluidity of digesta further enhances mixing of digesta and exposure to enzymes. Indeed, reducing particle size of corn from 800 to 400 microns increased digestibility of dry matter (+3%), protein (+10%), and energy (+4%) in growing pigs. From a comprehensive review of literature, Hancock and Behnke (2001), two KSU exceptional professors — now both retired — suggested 1.3% improvement in feed efficiency for each 100-micron reduction in particle size.
The value of reducing particle size
Reducing particle size not only increases energy consumption at the mill but it also reduces production throughput. In a further KSU trial, it was demonstrated that as particle size of corn was reduced from 1,000 to 400 microns, energy consumption increased and output was drastically decreased. Reduction from 1,000 to 600 microns resulted in a 40% increase in milling energy use and a 4% reduction in rate of production.
At 400 microns, milling energy was increased by 200%, whereas output was reduced by 52%, again compared with grinding at 1000 microns. Thus, it was widely accepted today that a particle size of about 600 microns was an optimal compromise between animal and milling performance. Today, this number is closer to 800 microns for pigs to save grinding cost.
Fine particle size may also reduce the flowing characteristics of the feed, especially of dairy products, which are rather hygroscopic, make up a large fraction of the diet. Thus, for meal-type diets a particle size of about 700-800 is often considered optimal. Conversely, in pelleted diets finely ground ingredients (i.e., less than 600 microns) are desirable because they produce more durable pellets, but they are obviously more expensive when electricity is expensive.