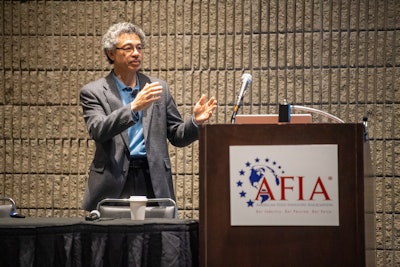
The American Feed Industry Association (AFIA) hosted a new half-day educational program today, in conjunction with the International Production & Processing Expo, providing animal agriculture business leaders with tips for managing volatile situations that impact their operations.
“From the constant threat of animal and human diseases, to supply chain interruptions, to dealing with the headwinds of changing trade policies, to volatile weather, today’s business leaders are managing a lot,” said Paul Davis, Ph.D., AFIA’s director of quality, animal food safety and education.
“Working with AFIA’s Nutrition Committee, we delivered a unique program today that gave business leaders a chance to hear lessons learned over the past two years from industry peers so that they left equipped with ideas and strategies for improving their crisis management plans for the future.”
The “Business Continuity in Times of Disruption: Lessons Learned from the Feed Industry” program covered topics such as: managing government relations when local, state and federal restrictions and requirements change or conflict; navigating personnel and other workforce issues; developing transparent internal communications; and ensuring the timely delivery of safe, quality products.
“We are more physically connected now than ever before,” said Yone Dewberry, chief supply chain officer at Land O’Lakes, Inc.
“When we are that integrated, and one part of the chain breaks down, you get major, major shortages.”
Dewberry provided the example that to make a single hot tub, 1,850 different parts must travel 887,776 miles from seven countries and 14 states.
Dewberry encouraged attendees to consider the different ingredients, vitamins, parts, bags, etc., they are using to manufacture their products to better understand the complexity of their supply chains and develop contingency plans in case there are supply chain bottlenecks.