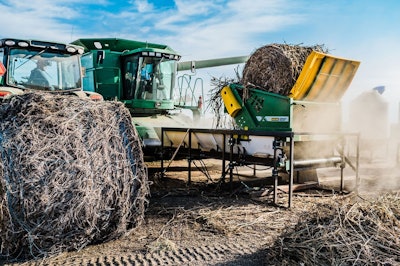
Industrial hemp is on the verge of a major growth phase driven by deregulation, new product development and massive growth in consumer demand.
Blue Sky Hemp Ventures is hoping to get a piece of that pie by kicking off production of high-quality cannabinoid extracts from its large-scale extraction facility, the first of its kind in Canada.
The company is currently producing CBD crude oil and distillate with CBD isolate expected to come on stream later this year, joining a host of hemp-based products on the company’s roster.
“Our business is among the first to pursue three revenue streams from the same hemp crop — fiber, food and extracts,” says Co-Founder and CEO Andrew Potter. “This is a big moment for us and our growing partners. As one of very few extractors, we have direct access to the high-value CBD market, estimated at $3.9 billion, which will generate significant revenue that hemp growers can’t get to alone.”
Hemp as a food product is projected to grow 15% annually. The market for hemp foods in Canada is estimated at approximately $150 million per year, says Potter.
“The primary drivers supporting growth in hemp food demand are, one, increasing consumer interest in plant-based proteins – hemp is one of the highest quality most digestible proteins on the market,” he says. “And two, the general trend toward healthier eating – hemp foods (hulled hemp, protein powders and hempseed oil) are all nutritionally dense superfoods.”
Whole plant utilization
Blue Sky Hemp Ventures was established in 2017 by four co-founders: Potter; Mike Rimell, CFO; Wilson Johnson, chief agronomist; and Devin Dubois, vice president of corporate affairs.
Headquartered in Calgary, Alberta, the company has operations in Rosetown and Saskatoon, both in Saskatchewan. The Rosetown facility is home to the company’s biomass high-grading operation and future home of fiber processing. At full capacity, the facility can process material from approximately 30,000 acres of land.
Blue Sky’s new 15,000- square-foot state-of-the-art hemp central processing facility, located in Saskatoon, is capable of processing 5,500 tonnes/year of hemp seed into various superfood products. It also houses its CBD extraction and post-processing operations.
For Blue Sky Hemp Ventures, the focus on whole plant utilization is a primary differentiator.
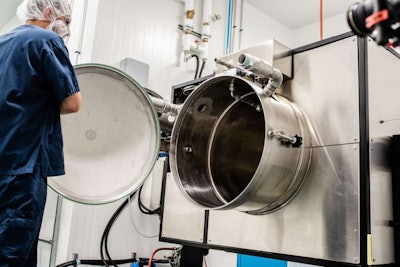
“Using the whole plant is absolutely key to producing hemp in a sustainable way,” says Potter. “There are many companies who have focused on CBD only. While this has worked in the short term due to sky high CBD prices in Canada, you only have to look to the U.S. where prices have dropped 80% in the past 12 months to see most processors will not survive.
“Our approach is different because the combination of low-cost plant material and having three uncorrelated revenue streams allows us to survive volatility and produce at a low cost,” he explains.
There are three main reasons why Blue Sky puts “whole plant” utilization at the heart of everything it does. First, by using the whole plant, hemp is made more economic for the farmer. Second, by using the whole plant, nothing is left to waste and large amounts of C02 are absorbed, leaving the company with a zero-carbon footprint.
Finally, because Blue Sky can take all the biomass from the farmer, it procures inputs at a lower cost than any of its competitors, which gives it a sustainable cost advantage while still yielding strong returns to the farmer.
It is worth noting that a large portion of Blue Sky’s growing partners are also shareholders. The company contracts 8,000 acres of farmland in Western Canada, with the potential to expand up to 20,000 acres with its farmer-partners.
How processing works
Hemp processing starts in the field with the biomass collection. There are several different approaches.
In the U.S., most hemp is grown “orchard style” for CBD only, which generally means low planting density and a focus on planting feminized seeds or seedlings and lots of manual labor and intensive drying.
But Blue Sky’s approach to harnessing the value of the whole plant, not just the CBD, has them focused on broad acre farming industrial hemp because they believe that is the safest, lowest cost and most scalable way to harness the value of the plant.
Therefore, they generally use two approaches to harvesting depending on the primary target — the flower for CBD or grain for food.
When CBD economics are the best value, the company swatches and bales the tops of the plants to maximize flower volume and potency.
“Although this approach is done earlier in the season, we still tend to recover a meaningful amount of usable grain,” says Potter.
If grain economics are the primary driver, Blue Sky generally combines for grain and captures the loose chaff to recover some value from CBD.
Once the material is harvested, the biomass (whether baled or loose chaff) goes through a proprietary reduced flower and leaf (RFL) process where individual components – flower, grain or fiber – is stripped and each component is processed further into end products.
Hemp hulling is a process of separation. Starting by separating the appropriate kernel sizes of seed, then hulling and separating again the unwanted and finer material, hulls and any remaining whole seeds from the finished hemp hearts.
“This needs to be done in such a way as to maintain the integrity of the fragile hemp heart,” explains Potter. “Forsbergs Inc., a manufacturer in the separation industry, has fitted us with a large portion of our necessary food grade equipment.”
Another supplier, Can-Seed Equipment Ltd., assisted Blue Sky with designing its state-of-the-art facility.
There are many approaches to CBD extraction. Blue Sky uses a cryogenic ethanol extraction approach.
“This process was chosen due to its safety record, since ethanol has a well-established history in food and botanical processing,” says Potter.
Primary CBD extraction produces a CBD ‘crude oil’ which is about 50% CBD by volume. Blue Sky can also further process the crude oil to CBD distillate (up to 90% CBD by volume).
“Soon we will bring on our CBD isolate capability, allowing us to produce a 99% pure CBD powder,” Potter says.
Automation efficiencies
Blue Sky has heavily invested in automating its facility, with the help of two Canadian companies, OneStep Automation and Impact Energy Services.
“Automated start and shutdown sequences and instrumentation feedback from multiple sensors really make the line operation efficient and effective,” says Potter. “Backups and plugs are sensed quickly and enables the operators to rectify issues by pinpointing error locations.”
The biggest challenge of processing hemp in Canada is the regulatory environment, says Potter.
“We would argue that industrial hemp in Canada, governed by Health Canada, is vastly over-regulated and is currently putting Canadian hemp farmers and processors at a disadvantage relative to other producing countries like the U.S.,” he says.
The other primary challenge, and source of excitement, is that hemp processing technology is in its infancy.
“Rapid change is exciting, but also a challenge because it requires large capital and attention to remain at the forefront,” says Potter.
With its food and extraction facilities now running, Blue Sky is set to focus on developing fiber conditioning systems, allowing the company to supply hemp fiber and hurd to makers of industrial products and textiles, and potentially be used as renewable energy source, plastic displacement and wood pulp alternative.
Blue Sky’s goal over the next 12 months is to work toward global expansion.
“We have a demonstrated facility and process that we can replicate quickly and at a low cost around the world,” says Potter. “The sky is truly the limit.” ■