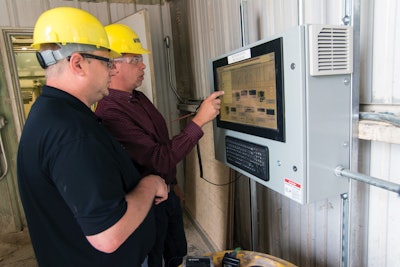
The process of turning wheat into flour is an ancient one, and remains to this day a very important one. Wheat is the most widely produced cereal in the world, mostly prepared for human consumption. The global flour market was valued at $200,497 million in 2015 and is expected to reach $270,895 million by 2022 according to Allied Market Research statistics.
Yesteryear’s millstone has made way for percussion grinders and rotary sieves in modern flour mills. As wheat is routinely ground, separated, sieved, and parceled out for purchase, great care must be taken to ensure each step of the process is executed perfectly.
U.S. flour millers must adhere to FDA Food Safety Modernization Act (FSMA) rules pertaining to preventative controls for human food, in addition to sanitary transportation and other guidelines. While flour regulations and processes vary from those of feed milling operations, both can benefit from ramping up digital and automated strategies designed to improve on food safety and ingredient handling.
Food-grade flour and the future of feed
Flour is the foundation of our breads, baked goods and fried favorites. The food-grade grain must be closely monitored in its production, and today’s smart mills and operations personnel are up to the task.
North American flour supplier and grain innovator Ardent Mills has more than 40 community flour mills and blending facilities throughout the U.S., Canada, and Puerto Rico. Seth Beyer is Ardent Mills’ plant manager in Lake City, MN, and handles all inbound and outbound shipments at the mill.
Beyer says that while flour has a simpler manufacturing process than feed, it is more heavily regulated. Therefore his team is more hands-on when it comes to testing, examining contents and possible contamination, and adhering to food safety protocols.
That said, he and others in the industry believe the gap between flour regulation and feed regulation is narrowing, particularly as more consumers desire to know what goes into the product they feed their livestock and pets.
“You’re starting to see this market change to ‘I want to know where my pet food comes from,’ and you’re seeing a more food-safe approach to animal food,” Beyer says, “But [at this time] flour milling as a human product is much more regulated.”
Despite the nuances of flour and feed milling, strategies can be adopted and implemented to improve both.
Ben Langstraat is an automation manager at Interstates, a purveyor of electrical engineering, electrical construction and control systems based in Sioux Center, IA. He explains flour mills often have a different focus on food safety compared with feed, and both provide unique challenges.
“Feed production uses regulated ingredients and has sequencing concerns when producing food for multiple species that we don’t see to the same degree in flour,” says Langstraat.
Flour mills, he adds, tend to be extremely data focused — more so than feed operations — and often employ “smart machines” to track and quantify ingredients.
“There are many in-line scales throughout flour mills that we don’t often see in feed,” says Langstraat. “Quantities of product movement are tracked in ways we don’t often see in the feed world. Many flour mills often have a focus on yield and process efficiency that we often do not see in feed. Flour mills operate in more of a continuous process with longer runs, and the data they capture is more time-based than a feed mill’s production run-based data.”
Flour and data
The “smart” machines mentioned earlier provide a wealth of data that can be monitored. Some examples of this are roll stands with temperature and vibration sensors that help with maintenance and equipment loading.
“All these smart machines and scales in modern flour mills require networking throughout the plant floor that we often don’t see at the same level as the feed industry,” says Langstraat.
The data attached is invaluable for a number of reasons — food safety and accountability to be sure, but also overall plant safety and efficiency.
Data can help solve problems, for example, by tracking ingredient movement and providing proper controls to prevent carry-over and product contamination. Langstraat believes the feed world could gain from flour’s focus on process data to also help drive plant efficiency.
“Control solutions need to be able to provide track-and-trace information in both scenarios,” says Langstraat.
“The plant controls need to act on the data available to aid operations staff in making good decisions.”
He adds, “In the past much of this logging and planning was done on paper. A simple control solution that only provides machine interlocks is no longer sufficient.”
Hazard monitoring and traceability
Automated systems and the data within can help mills achieve ideal levels of accountability, safety, and efficiency, especially as technology improves from year to year. And they can help to ease staffing pressures too, even as quality and control expectations rise.
“With the expectation that regulations and protocols for food safety will continue to increase, technology allows mills to meet those demands without adding additional staff,” says Brady Gaalswyk, vice president of Easy Automation, Inc. (EAI) in Welcome, Minnesota. EAI produces solutions in controls, software, and equipment.
Gaalswyk says in addition to ensuring food safety and requirements are met; information collected via automated processes must also be tracked in the technology’s operating system so users can go back in history to trace products from raw to finished, as this adds another layer of confidence to a product’s integrity. By implementing software that “double checks” processes that would otherwise require manual labor, Gaalswyk says facilities can meet new and ongoing requirements in an organized and efficient fashion.
Perhaps not surprisingly, the higher the level of automation a facility employs, the greater its impact.
Jason Grahek, director of business development at Knobelsdorff Electric, a full-service electrical and automation provider in Goodhue, Minnesota, left the automation side of the business for a five-year period before returning to find systems that were more interconnected than ever before.
“It was fun to depart from automation for a while and come back,” says Grahek. “[When I started in this industry] there used to be a lot of those small manufacturing cells -- portions of the facility that might have a little standalone interface. But nowadays with the plant-wide SCADA (supervisory control and data acquisition) systems you can really tie everything [together] and have complete visibility into the entire process, down to individual health bits on sensors so you know your instrumentation health, and what’s going on out in the facility for that proactive maintenance experience.”
Beyer at Ardent Mills agrees this holistic approach has helped improve food safety and facility management across the board. “We use technology to help identify risks. A lot of projects we have put in, whether hazard monitoring or temp reading, helped us identify risks sooner with smaller impact to the business, and helped push those initiatives around food safety.”
Solutions for long-term success
When it comes to implementing an automation solution, purchasers should consider hardware and software that will allow them to “future-proof” their systems, meaning design that supports future upgrades and keeps knowledgeable support close at hand. As with many products today, there’s no need to hang onto rigid legacy systems when newer, web-based solutions may come with support and a lower cost to implement.
“Your automation is the heart and brains of your facility; it is interwoven with the facility itself and has a huge impact on how you operate the productivity, the lack of downtime ... everything,” says Easy Automation’s Gaalswyk.
He adds, “[Automation] can be custom-tailored to each facility in regards to how it works and what part you have to do first. Many people think the older facilities [would cost] too much to automate. The fact is we are able to utilize a lot of existing equipment even in older mills and continue to automate more and more as changes happen over the years.”
Flour and feed facilities not currently on board with automation, or using it here or there, can better meet regulations set forth by FSMA (and experience better productivity along the way) by leveraging the help of an automation partner and smart systems.
Like the end-product they produce, a mill’s longevity and health is only as good as what’s inside. ■