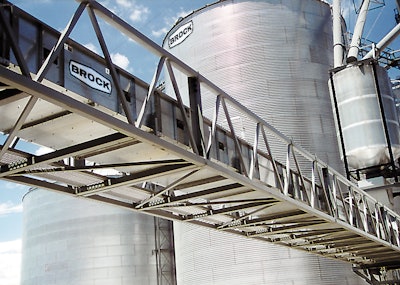
Moving grain is one of the most important steps to complete the cycle of taking grain from field to market. With the quantity of grain being produced and shipped around the world, moving grain safely and efficiently is more crucial than ever.
Moving large quantities of grain efficiently
When you need to move thousands of bushels of grain an hour, one of the most efficient tools is a Brock® Enclosed Roller-Belt Conveyor. These systems have capacities up to 57,800 bushels per hour (1468 metric tons per hour) and are able to start under full load.
Moving grain to multiple bins or silos
With Brock’s conveyor intermediate discharge unit, one enclosed roller-belt conveyor system can have multiple discharge points to easily service many bins or silos. It works with Brock enclosed roller-belt conveyors in belt widths from 26 to 54 inches (650 to 1350 mm) and speeds from 400 to 700 feet per minute (2.0 to 3.6 meters per second).
As your grain handling needs change, the Brock conveyor system is designed to grow with your business. If you decide to add a bin in the future, you don’t have to start over with a completely new system. The Brock intermediate discharge unit can be retrofitted to an existing Brock enclosed roller-belt conveyor.
Innovative no-touch design
Some belt conveyors offload grain to intermediate bins using a plow blade that scrapes the grain from the belt. An important benefit to the Brock discharge car is that it never comes in contact with the belt. The system uses a horizontally moving discharge car that slides under the grain flow to divert the stream to intermediate bins or silos. All impact points and discharge chutes are fully lined with urethane for long life. The Brock discharge section transfers grain from both sides of the belt to a single discharge under the conveyor.
Simple maintenance
An electric-powered dual rack and pinion drive controls the discharge car. The system is simple in design, which also makes it easy to maintain and service. The Brock discharge unit has fewer moving parts than other discharge systems to provide reliable operation.
Weather-tight, dust-proof design
Roller-belt conveyors are enclosed to contain grain dust and to minimize explosion hazards. A distinct peak on the top of the Brock conveyor allows for snow and water runoff, and protects your product from the elements.
Smooth operation
Another unique feature of the Brock enclosed roller-belt conveyor is the design and construction of their idler pulleys. They use full-length shafts with positive locking tapered bushings for uniform weight balance and long equipment life. The smooth operation of their continuous belts is also very gentle on grain. Unlike an auger or drag conveyor, there's nothing pushing, pulling or dragging the grain, which minimizes grain crushing or cracking.
Energy savings
Brock conveyors are computer-matched to the motor drive and gear reducers to maximize efficient, energy-saving operation. All of the variables are calculated including belt size, length, speed, incline and number of discharges to build a highly customized conveyor system for each application.
Modular installation
How do you install a large, enclosed roller-belt conveyor system and keep your costs down? Continuing the legacy of Henry Ford and his advancements in assembly line manufacturing, Brock preassembles their enclosed roller-belt conveyors in 20-foot (6-m) sections in the factory for faster and more economical installation in the field.
Complete grain systems from Brock
Brock grain handling equipment, supporting structures, drying systems and storage bins work together to provide easy operation and long-lasting reliability. Your local Brock dealer designs installations using pre-engineered Brock solutions to move grain efficiently and with easy expansion in mind. Brock dealers not only provide site planning, system design and construction, they also deliver seamless support for all Brock components.
To build a custom enclosed roller-belt conveyor system that can help you move grain anywhere it needs to go, learn more at brockgrain.com/AB.