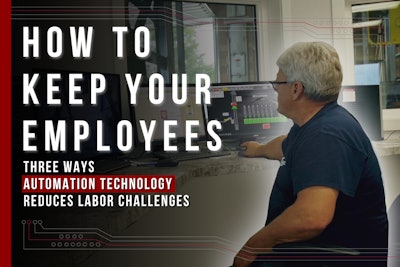
Labor has been and continues to be one of the largest challenges for feed and grain facilities. According to the USDA, from 2007 to 2019 labor force participation for those ages 25-65 decreased almost 3% in non-metro areas. While this may indicate a lack of people available to work in rural communities, it also indicates fewer people in those communities are choosing to work.
Recruitment is one significant challenge, but training and retention of employees also contribute to the overall labor challenges we have seen impact efficiency and productivity of facilities. Here’s how automation technology can help you and your facility overcome some of these labor challenges:
- Decrease Manual Processes
- Decrease Time Spent on Training & Onboarding
- Increase Employee Morale & Safety
Decrease Manual Processes
Tracking down orders written on a piece of paper, finding the latest version of the spreadsheet, pulling levers, manually weighing up product, and running up and down the catwalk multiple times a day to move trucks to loadout. What do these tasks have in common? Manual labor. Someone who is there physically to just complete the task. Automation technology can help reduce the amount of time your employees spend doing these important, but repetitive tasks. Investing in automation technology in your facility, both the equipment and the business side of your operation, can reduce the number of people you need to simply run the mill and reallocate their time to doing work that moves your facility forward. Instead of simply making the facility run.
Decrease Time Spent on Training & Onboarding
A long-time employee is looking to retire in the next 3 years. Great in theory, but he is the only guy who knows the mill like the back of his hand and is the point person for questions and problems that arise. He is the only guy who knows where the levers connect to and what ingredient bins they connect. How do you start replacing that individual? It is a common situation many facilities encounter. Insight, years of experience and overall mechanical knowledge can be transferred, but it often takes many years of mentorship and the right person to take it on. With the next generation of workforce more technology focused, utilizing automation technology, like customized HMI controls, in your facility with decrease training time and help simplify the processes in your facility. Hopefully, making training and onboarding a less daunting and stressful transition.
Increase Employee Morale & Safety
Our workforce has aged, in parallel with the median age of farmers in the United States. The demands of manually running a feed mill have taken a toll on our current workforce. Tasks that used to be simple, like loading bags manually into the mixer or walking up stairs to the catwalks, now have become more challenging and tasking for our employees. Implementing automation technology, although it does require onboarding and training on the platforms, can significantly improve employee morale and safety within facilities. Instead of being physically taxing, the job is now mentally stimulating and allows for more energy to enjoy life outside of the mill.
The pressure to produce more with less isn’t going away. While the goal of implementing automation technology isn’t to completely replace the workforce, there is value in reallocating the time and energy of your workforce onto tasks that will move your business into the next generation.
Interested in exploring how automation technology can reduce your labor challenges? Visit easy-automation.com or call 507-728-8214 and ask for our sales team. We value your partnership and look forward to solving your equipment and automation challenges with you.