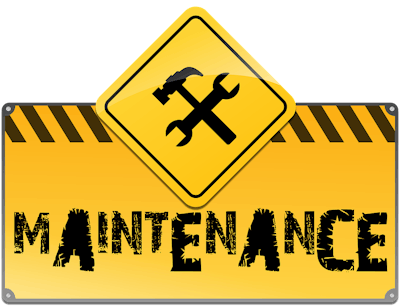
Maintenance programs shouldn’t be an afterthought or a burden. Having the right preventive maintenance program for your facility can save you thousands of dollars in lost productivity.
PM programs can also increase your reliability, especially in high-use times such as harvest where downtime can cost your triple or more, says Frank Byers, president and CEO of AgriSphere, LLC, Mahomet, IL.
“A breakdown can reduce a company’s competitiveness by not being able to respond to market opportunities due to down shipping and transfer lines, as well as driving off patrons when receiving capabilities are limited,” says Byers.
If you don’t properly inspect and maintain equipment, it can lead to catastrophic failures which may result in extreme and costly damage to assets, injuries to personnel, compliance and liability issues, says Byers.
“Routine unexpected downtime can also lead to emergency repair and operational situations which can have a negative impact on employee morale and company image,” he says. “A full-strength facility is capable of capturing opportunity when and how it presents itself. Operating at full efficiency can save money over operating at partial efficiency.”
The bottom line – it’s all about preventing a costly breakdown and saving you money, says Alan Berndtson, director of sales, Feed, Food and Agriculture, for WEM Automation in New Berlin, WI.
“A good PM program will save you money,” he says. “Breakdowns can have far-reaching ramifications. This is an investment in your facility.”
Parts of the program
Too many think preventive maintenance (PM) is only about lubrication, greasing, and replacing fluids, but it’s much more than that.
“In addition to lubrication, PM includes other tools that will give us warning that failure is going to occur,” says Ed LaPreze, sales and marketing director with Pepper Maintenance, Minier, IL. “These tools can include daily walk throughs, infrared, vibration analysis, ultrasound and other predictive tools.”
Ultrasonic lubrication will give a warning on bearing failures and reduce the amount of lubrication that needs to be applied. Infrared will reduce electrical costs and find failures early. Vibration analysis will find failures very early and give information to assist in making the equipment run more reliably and efficiently.
While these predictive tools are important, lubrication is still a key component and should be treated as crucial part of any preventive maintenance program.
“Often lubrication is an entry-level task performed by the least experienced personnel,” says Byers. “By assigning more experienced and well-trained staff to perform lubrication, you can enhance the impact of lubrication by ensuring it’s done properly and not in a manner which will burn a bearing or blow out a seal.”
An experienced eye can also catch other maintenance- and equipment-related issues, especially in or on infrequently visited areas or equipment, that a less experienced employee may walk right by.
Employees in general are an important piece of the puzzle. Labor is a big line item and there can be temptation to not replace a lost maintenance person.
“Often the mentality of management is that we can survive without one maintenance guy for a bit,” says James Ramey, application engineer with Repete, Sussex, WI. “The reality is the maintenance people that are left will switch their focus to keeping the plant running and not looking for what will keep it from running.”
LaPreze agrees. “Often grain facilities start budget reductions in the maintenance department, reducing staff and limiting funds available for repairs,” he says. “This is the opposite of what we should be doing. Less staff leaves fewer man hours available to do routine maintenance and repairs. Reliability will save a company more money than reduction in budgets will.”
It’s also good idea to establish lines of delineation for your staff so they know what – or what not – to work on.
“Knowing when it is time to engage a contractor or specialty firm can help prevent further damage to a system when maintenance is performed by inexperienced or unprepared staff,” says Byers. “By doing so, proper specialty tools and equipment can be brought to bear by the contractors which may not be justifiable to keep in house.”
What your program should tell you
Every piece of equipment in your facility should be a part of your PM program. Daily walk-throughs and lubrication should be performed on all equipment. Other tools should be used on critical equipment – those pieces that will cause a plant to stop production, have hard-to-obtain parts, or safety implications if they fail.
A good maintenance software program will provide you with the life cycle costs of each piece of equipment, says LaPreze. In addition, the program will show the history of lubrication and repairs and a list of parts to make it easier to order replacements when necessary.
Berndtson says your maintenance software should also interface with your automation software so you can track exact run times. It should also include instructions with alerts to retain standard operating procedures when maintaining equipment.
Having access to timely, accurate, and complete historical and real-time data helps draw a complete picture and is one of the benefits of having a comprehensive maintenance program.
“Data can help you identify trends, investigate and discover root causes for conditions, and provide justification for continual improvement initiatives,” says Byers.
Of course, in some cases record keeping is a compliance issue. The Occupational Safety and Health Administration as well as many food safety programs require accurate and comprehensive maintenance record keeping to maintain compliance.
“For example, in some programs, you can create an alert for scheduled cleaning times to help with sanitation needs,” says Berndtson. “When it comes to programs like Safe Feed/Safe Food, documentation is a big piece of compliance.”
It’s all about the records
Of course, to make any computerized maintenance management software (CMMS) useful, there must be time spent entering data.
“All those old moldy files that most maintenance departments have sitting in an antique file cabinet need to be entered,” says Ramey. “This will probably represent 40 to 60 hours of data entry.”
Ramey says it’s tempting to just enter data in as you go, but that philosophy can backfire.
“The maintenance team usually only pulls files if there’s a problem,” he explains. “And during a breakdown they won’t take the time to enter the information.”
Ensuring your employees are well trained and understand the CMMS and what it can do goes a long way toward having a successful program.
“Buy-in from the team is critical,” says Ramey. “If they don’t use the software, it won’t help the facility.”
Recordkeeping for all maintenance activities is one of the most critical parts of a successful program.
“Records allow you to monetize the equipment and record all repairs made,” says LaPreze. “Records can indicate when changes to maintenance programs need to be made or if it would be more cost effective to replace the equipment. Small differences may be making a large impact that would not be detected without good records.”
The best way to get employees to comply: make it easy for them, says Berndtson.
“There are a lot of programs out there,” he says. “Some are broad and encompassing but may not be the easiest to use. If it’s too time consuming or hard to use, it won’t be utilized correctly.”
Finding the best CMMS for your facility
The features of any CMMS should be customized to an individual facility.
“No one program fits all,” says LaPreze. “Every plant is unique and should be addressed on an individual basis.”
When selecting a program, keep some of these features in mind:
- Ability to track and report data in a user-friendly framework
- Ability to tap into PLC or hazard monitoring data and correlate it to maintenance data
- Mobility to allow field usage to ensure accurate and timely data and verification is always
- available
- Historians to help predict a failure before it becomes critical
- Accommodation of safety and food safety models
- Push-notifications, alarms, and “take action” functionality to create safeguards within your program and for your equipment
- Flexibility
“Flexibility is important,” says Berndtson. “Each piece of equipment has its own needs and requires its own individual report. Some will need alerts based on volumes or hours or actuation.”
Regardless of the type of PM program and software you choose, it’s critical to your bottom line to be using one.
“You’ll get your investment back,” says Berndtson. “If you use the program and maintain the data, your payback will happen within a year by preventing just one critical failure.”