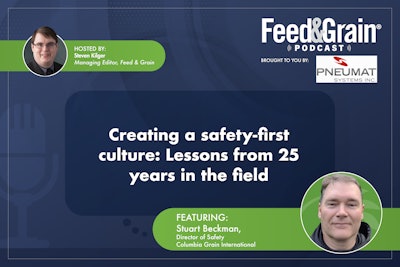
In this episode of the Feed & Grain Podcast, host Steven Kilger speaks with Stuart Beckman, the director of safety at Columbia Grain International. Drawing from over two decades of experience, including military service and safety leadership, Stuart shares his unique approach to fostering an effective safety culture. Discover key insights into his "show a little, do a little" training philosophy and learn how hands-on instruction can elevate safety standards in grain handling operations. Don’t miss this deep dive into proven safety practices and engaging employees in proactive safety initiatives.
Steven Kilger - 00:00
Hello! My name Steven Kilger, I’m the managing Editor for Feed & Grain Magazine and the host of the Feed Grain Podcast. Thank you so much for joining me today as we dive deep into the issues affecting the Feed Manufacturing, Grain Handling and allied industries.
Today’s episode is brought to you by The BinWhip from Pneumat Systems. The powerful Dual Impact BinWhip removes the toughest buildup and blockages in industrial storage silos – without hazardous silo entry. Learn more today at binwhip.com.
Today's podcast guest is Stuart Beckman, director of safety for Columbia Grain International. Stuart is here to talk about his views on creating an effective safety culture, safety initiatives he’s been implementing at Columbia Grain International, and how he gets employees involved in the whole process.
I hope you enjoy the interview, if you want to help out with the podcast and are listening to this in a podcasting app please rate us and subscribe! If you’re listening online signup for the Feed & Grain Newsletter Industry Watch to see when new podcasts drop and stay up to date with all of the news from around the industry.
Now onto the show. Hi Stuart, thanks so much for joining me today.
Stuart Beckman - 02:11 Steven, thanks for having me. Glad to be here.
Kilger – 02:13
No, happy to. It's always, well I mean especially this time of year, right, it's safety season. It's when we should really be paying attention to it so it's always really nice to have kind of a safety expert on to talk about some of this stuff. Can you just tell our readers a little bit about yourself and what you're doing right now?
Beckman – 02:40
My name is Stuart Beckman. I've been in this industry for close to 25 years now. So a number of years I've been the director of safety here at Columbia Grain for about the last four months. But previously I was a director of safety for many years and a safety manager and an operations manager and also spent some time in the military. So I've got a pretty good background of working with people and problem solving and enhancing safety at the grain businesses. So it's fun.
Kilger - 03:06 Yeah, what two decades I think I saw in your in the little press release announcing your kind of arrival at Columbian Grain. Two decades plus the military expense. How has that shaped how you think about safety in the grain industry?
Beckman - 03:26 You know Stephen I spent 30 years in the North Dakota Army National Guard some of it was full-time service and deployment some of it was part-time but for five of those years I was an actual military instructor and I actually taught at the University of North Dakota The Army ROTC program, so I taught young Army cadets in ROTC and I spent some time working with the state's officer candidate school in Camp Grafton and actually taught officer candidates as well. You know, the thing that I learned the most from being an Army instructor was we had a simple premise on how we would train our folks and it's six simple words and it is, we show a little And then we do a little. And all that means is if we're going to do a task, we're going to break that task down, we're going to show the guys how to do it, and then we're going to let them perform that task, right? So if it's if it's cleaning up a weapon, if it's Goal point if it's doing some other military task we show a little bit of it and we let them do it and that's how they learn and really but the point is we need to do the same thing in the grain business right we have all these trainings either powerpoints or maybe some videos whatever the training is but people learn and operations employees learn best if we show them We talk about confined space or bin entry operations. But besides doing the training through your PowerPoint or whatever your methodology is, we need to take them out in the plant and show them how to do it as well.
Beckman - 05:16 And we can break those tasks up. We can do, we can show how to calibrate and bump test and air monitor and do a little hands-on training. We can actually get them into their harnesses, talk about their safety equipment and gear and how to properly use that gear. And then we really need to take them out in the plant and fill out our permits. And then instruct the guys, hey, what are the jobs and the primary roles and responsibilities for your entry supervisors, your entrants and the tenants? And that's how we learn. So the best advice is more hands-on training, show a little, do a little and practice and the guys will learn and understand those tasks.
Beckman - 05:56 And it'll be great training and your guys will be engaged.
Kilger - 06:00 Yeah, you don't really think about it when you're thinking about your position, which is director of safety, right? And it's so much of a teaching position in a way, isn't it? It's teaching people how to be safe and keeping on them. It's those same kind of skill sets that you don't really think about when you're just looking at your job overall, but it's probably the most important part of it, right?
Beckman - 06:24 It is. It's coaching and mentoring, right? It's coaching and mentoring and being a resource for the guys out in the field and for those locations. So important, important to be able to do that.
Kilger - 06:35 And the hands-on thing is so important because you know we can watch all the videos you want online and think you know the entire process but till you're in the actual facility doing it you really can't you really just don't have it it's an idea and it just won't really stick in your head until you see it in action.
Beckman - 06:52 Yeah once you practice it and you've figured out hey this doesn't work but this concept does work guys will learn it they'll remember it and they'll execute it safely.
Kilger - 07:02 Mm-hmm exactly and so you're relatively new at your position four months you said you've already done a gap analysis at CGI of their safety programs what have you kind of learned so far what are some areas for improvement you guys are going to be working on and how are you going to address them?
Beckman - 07:22 You know, I'm glad I've had four months and there's a lot to look at, right? A new brain business, all their safety policies, procedures, their training, so it's taken a while to go through all that. But, you know, I just want to make sure we're following OSHA standards and guidance and I want to make sure we're following industry best practices. You know, Columbia recently had an incident where we had a rail car derailment and in some operations there. We are going to take that a step further and we are going to have a training on what to inspect in rail yards. We have a lot of newer employees or newer supervisors that don't really know what to look for when they step into a rail yard. What is safe?
Beckman - 08:07 What is unsafe? What is the right gauge? How should the track look? How many spikes? What is the condition of the ties and drainage? There's a lot to consider and we just want to make sure that our rail yards are safe and ready for operations. We want to make sure that the guys know how to inspect and properly use the rail fall systems to keep the guys safe when working on top of rail cars.
Beckman - 08:29 So we know we're going to make some improvements around rail safety. Another thing I wanted to do, we wanted to make sure and have a way that our employees can report unsafe conditions or unsafe hazards and maybe even when employees are not following procedures and that's going to help our employees engage and look for hazards and then obviously we're going to take corrective action so we want to encourage reporting. So it's not only reporting near misses, but it's reporting these behavioral based safety observations around conditions or behaviors. And obviously we want to make sure that the guys feel comfortable reporting incidents and accidents because we learn from them. We're going to learn from them and we're going to share that knowledge. And we're going to share that knowledge through a monthly safety call that we have gotten started now.
Beckman - 09:28 And that monthly safety call is really important because I think it's our way to get people engaged in safety and have a discussion that's focused on safety. One of the things, Stephen, we do or kind of how I've set up that call is I make sure our top corporate leadership is on that call to start us out because leadership and safety starts from the top. And all of our folks in Columbia believe that and want to make sure safety is our top priority. So it's great to have our presidents, vice presidents, our corporate leadership on that call. Next, I want to make sure I give some time to food safety and human resources. They've got some things that they'll want to talk about on the call too, and we want to give them a venue or an avenue, I guess, to be able to talk about some things that are of concerns to them. And then I really want to get into the safety portion of the call, Steve, and then talk about our incidents and accidents.
Beckman - 10:23 Because we investigate them, we learn from them, we figure out what went wrong, and then we figure out a way to control the hazard and prevent that from happening in the future. So really important that we have a way to be able to share this with our guys and teach them. Obviously, again, newer employees and things. We just need to take the time to coach and mentor and guide them. Just a couple more things about the call that I really like. I like to share hazard pictures, right? We can hear something, but if we hear something and see something, our guys will remember it.
Beckman - 10:59 Our operations staff will remember it. So to show hazard pictures of inadequate machine guarding or a fall hazard or electrical hazard, whatever it is, that gives the guys more knowledge and understanding. So when they look through their plan, if they see something similar, well guess what? We've got to take some corrective action. And really the last thing I like to do in those calls, Stephen, is I like to call out our guys for the good things they're doing out in our facilities. They're figuring out how to solve problems and make processes better and more efficient and safer. So I like to make sure we call out those guys, let them talk about how they're troubleshooting some of this stuff and some of the problem solving they're doing and the great work that they're doing for our business.
Beckman - 11:43 So I think these monthly safety calls are very good. And just the last thing I want to mention about something we need to make some improvements on, and I think this goes for every grain business out there. We have what we call critical safety devices. Or some people call them hazard monitoring and it's the things, you know, the three tools that we have typically with critical safety devices are alignment sensors so we don't have a leg belt rubbing on the casing or anything to build up heat because of the combustible dust, right? We don't want a fire or an explosion so we want to make sure rub blocks and alignment sensors are operable. We want to make sure that we have bearing thermocouples so we know if we're getting hot bearings or things are operating normally or not. Speed sensors on the tail pulley of the leg just to make sure we don't have a plug condition where we're going to burn a belt in half and have some type of fire or explosion. Beckman - 12:39 So I think we just need to set some standards around critical safety devices, how we maintain them, set points, and these are just some of the initial improvements that I feel we have to do at Columbia.
Kilger - 12:52 Well, yeah, I mean, I think the most important, I mean, the call sounds great because from what I understand, at least from, you know, kind of an outside observer in the industry is one of the most important things to any safety plan is making it kind of open and non, you know, non-judgmental. Obviously you take care of problems you have, but people shouldn't be afraid of bringing you their concerns and things. Cause the moment it goes to like a punishment action is the moment people stop reporting anything. So like this call sounds great where you can kind of see what's happening. I'm sure there's tons of people that are on the call and be like, Oh yeah, I see that picture. And they're like, Oh yeah, that's something that's happening here too. Sure.
Kilger - 13:35 There's tons of people who are really grateful that they're getting, you know, called out and a little pat on the back for doing their jobs and going almost above beyond and being like, Hey, this is a safety issue that I'm going to report and bring to everybody's attention.
Beckman - 13:51 For sure, we've got to share these things, we've got to give the guys the platform to share some of these learnings and understand our processes better. And again, our people are the problem solvers in our business. They're going to think of better ways to do things many times than I will. So we really want them involved and it's great to share that on those calls.
Kilger - 14:12 Especially because you have I think 48 grain facilities, 10 processing plants, a huge network that you're in charge of. So those people on the floor are the ones that actually see it day to day. They're the ones that know those dangerous situations and all those hazards. So it's great to get them involved. Is that kind of the key then to maintaining such a good safety culture in such a large network of facilities and plants?
Beckman - 14:39 For sure, right? We want to encourage reporting, we want to get the guys involved. People make mistakes, even really good people make mistakes, right? So we have to learn and understand. That's the most important thing. We shouldn't punish. We've got to learn and understand what happened and what went wrong and then we can correct that in the future.
Beckman - 14:56 But, you know, with all the facilities that Columbia Grain has, you know, one of the things that's really important, we need to set our standards, right? We need to set our standards. We need to write good policy safety policies and have the right training that goes along with it. But the hard part that comes with that is Columbia Green's got different facilities, right? We have barge loading locations, truck loaders, rail loaders, we even have some export facilities. And then we've got pulse plants and edible bean plants. So some of our location, a lot of our locations do different things.
Beckman - 15:32 We have to have standards, but when standards Don't always apply to every one of those businesses, sometimes we need to come up with a better way to protect our people and we do that through what we call JHA's right job hazard analysis where we look at the steps, we make sure and look at the steps, what are the hazards and then how do we mitigate and control those hazards. So it is hard, it's not easy making sure that we've got our policies covered across the network of facilities we own and operate but that's part of the challenge.
Kilger - 16:03 Mm hmm. Yeah. Well, even as you mentioned earlier, your rail facilities, like not everyone has to deal with those hazards, but a rail yard can be a very dangerous place if you don't know what you're doing and you're not keeping an eye on things, you're not keeping things safe. So every facility kind of has those little challenges, their own little they all work their own way. So when you when you visit one of your facilities, what's the first Safety wise, who do you talk to? What's your kind of step when you are visiting a facility?
Beckman - 16:43 You know, I would just say this, you know, I want to come with a purpose, right? So every time I go to a facility, I've got a purpose. And really, to me, there's three reasons when and why I visit a facility. And one is really a courtesy safety visit. It's to get to know the people, the location, the processes, And I want to be a resource. I want to see what challenges the guys may have or our operations leadership may have at the location. If they've got problems, they don't understand a program.
Beckman - 17:12 They're not sure how to handle this issue out in the facility. I want to be a resource and I want to help them out. If you go in and do a safety assessment, that will be a little more formal, but it should be a learning process. We want to make sure and go through some of their record keeping, some of their OSHA logs, some of their training, how much training have they completed or are they on task with their training calendar. Another thing, I want to make sure and have a discussion around the incidents that they are having at their location. Have we implemented the right corrective actions and taken some action? That's the most important thing.
Beckman - 17:53 If we have an issue, we've taken some action and we did something to correct that or fix it. I get involved in some of the incidents as well. If there's a serious incident, injury, accident, whatever, I'll be a part of the incident investigation process. I always make sure I take the time to also walk a facility. To me, it's super important to walk a facility and just look at conditions, check out the facility and meet some of the guys out in the facility. We want to meet and talk with those operations folks out in our facilities and I want to talk and engage them. I want to talk to them a little bit, thank them, I want to see what their challenges are, and they may not open up to me on my first visit, but by the second or third time I visit, they kind of know who I am, and they feel comfortable, you know, talking about some of their challenges, and we learn
Beckman - 18:57 so much, talking about this actually is a key important process, because combustion started, we end this industry. To me, that's really important that we run clean facilities, so I want the facility to be looking good and we don't have to put a lot of combustible dust. We're cleaning, we're making sure things are in good shape, but I also want to see that it's well maintained, right? So that's our line of defense. Keep it clean, keep it well maintained, and if we're doing our preventive maintenance and doing that well, you know our risk of an event is very low. So that's kind of my keys when I go visit a facility, Steven.
Kilger - 19:34 No, those are great. And a lot of the things you've been talking about today, it's just really about getting people involved, right? It's about safety culture. It involves everybody. And so it sounds like you're really focusing on making it so people are comfortable and willing to come to you with safety issues.
Beckman - 19:58 It's super important, right? We need to be a culture where we learn. We're not out there to punish people. We want to know the mistakes people are making. Like I said earlier, people make mistakes, good people make mistakes, but let's learn from it. That's the most important takeaway. Let's not punish, but let's learn.
Beckman - 20:14 So again, rolling out a behavioral-based safety observation program is going to be good. We're going to learn some things. The guys will report unsafe conditions and behaviors as well. We are going to encourage the near-miss reporting. I think there is a little mystery around near-miss reporting so there is going to be an educational part of this where we are going to talk about what is really a near-miss and how do we report it and how do we learn from it so that will be part of building that culture. I would like to say this, one of the things That I want to make sure that we accomplish this year is do a safety stand down, right? We want to do a safety stand down and show the guys the importance and the high level of the high level of importance that safety is for our business.
Beckman - 21:03 So we're going to we're going to cease operations. We're going to find some days that the guys will actually shut down the plant. We're going to focus on safety, do some safety training. We are going to invite families in and have a picnic, we might have a guest speaker. We are going to talk about the importance of safety, our commitment to safety and again the number one thing we want to have happen at the end of the day is they are going to go home to what is important to them and that is their families. We just want to make sure that we have a good safety culture and I think we involve our families. I'll say this, Stephen, you know, the one great thing about Columbia grain, we are a large formidable sizable grain company, but we're small enough where everyone knows everyone and it's more of a family atmosphere and that's, and that's wonderful for our safety culture.
Kilger - 21:51 Yeah. I mean, that's kind of great about the grain industry in general is a lot of companies, while they can't be very big and they can move a lot of grain, they are ultimately still a lot of, you know, they feel like They're small still. The industry itself still sometimes feels like it's small and you get to know people and you get to actually have honest conversations and talk to people, which is great. And bringing in the families is, I think, genius because like you said, safety at the job site affects your entire family, right? No one wants to have to have that call. No one wants to have to talk to a family where someone's been hurt. And just bringing in entire families to know that you're both caring and also like that this is important because sometimes you know that safety message does hit a little bit harder when you're sitting next to your kids versus when you're sitting there with your buddies at work just talking.
Beckman - 22:48 Agree 100% and for the wives and the spouses and the loved ones to hear our commitment to safety and the training that we do with our employees, how important it is and their well-being is our number one concern, right? We want them going home to their loved ones. I think that message resonates and it's great to have families be a part of that, kind of that stand down day.
Kilger - 23:10 Yeah, all right, edit this Steve, edit this out. Stuart, I think we've covered the question point five where you emphasize building strong safety culture and identifying interesting safety issues. Do you have anything else you want to add to that or should we just move on to the last question?
Beckman - 23:28 I'd like to just add one other thing to that if I could.
Kilger - 23:31 Yeah, sure. Do you want me to ask?
Beckman - 23:34 Yeah, if you don't mind.
Kilger - 23:35 Yeah, so you guys are doing so much to emphasize building kind of this safety culture and getting your employees involved and getting them to report, be part of these meetings, be part of the solution. Is there anything else you're doing to be proactive and kind of having employees identify and address safety issues?
Beckman - 23:58 I just want to mention this, before I started with Columbia, and this was a great idea that they've had for a couple of years now, Columbia has implemented safety action teams, or we call them SAT teams, safety action teams, and it's made up of operations managers from different locations. They do quarterly safety and operations assessments at other locations within Columbia and it's great to get our operations managers out to another site, meet the employees, walk the facility, look through some record keeping and training paperwork and it builds a peer-to-peer relationship And as we talk about in this business, obviously different people have different eyes on the facility finding hazards and suggesting solutions, right? So we've got a lot of people with different levels of experience and it's just great that we have these safety action teams out there looking at our facilities, networking with other operations managers, and then, hey, we report on the findings and see if there's a correlation between our three regions. Good to get these people involved and we do a little training with them as well. It's just been a really helpful process and good for our culture.
Kilger - 25:15 Yeah, I think so. Definitely has because I mean, you're doing all this, which a lot of companies are doing, you know, these kinds of safety programs and this kind of safety culture, but I mean, it's not uncommon to see some that are, you know, obviously doing it on a surface level and just doing it kind of for show. So it sounds like you're, you guys are really investing in this and that's what we'd like to see. Cause like I said, the goal is always everybody gets home at the end of the day, everyone's safe, everyone's doing well. And sometimes it just takes stuff like an outside perspective coming in and being like, Oh, this, you know, this cord on the ground, actually, that's a tripping hazard or. This is an unguarded conveyor belt. What are you guys doing?
Kilger - 25:59 I mean, when you're working there every day, you just, you don't always see it.
Beckman - 26:04 Yep. You overlook some of that. So to have different eyes is super helpful. And it's just, it's been a, been a great relationship and great to have those teams looking at our locations. Awesome.
Kilger - 26:16 So what are your, your plans for 2025, the rest of 2024, 2025? Harvest is nearing kind of completion and it's going to be, It's going to be a good time to start implementing even more safety initiatives. What's CGI's plans for the coming year?
Beckman - 26:34 Yeah, so I'm actually finalizing these plans for next year, for 2025 this week, so great topic for us to talk about, but just kind of the plans that I have, I wanted to lay out some corporate safety goals, so goals for the safety team at Columbia Grain, which includes me, and I wanted to have location goals so that our location managers and our operations managers Have skin in the game, let's call it having skin in the safety game, and make sure that we're keeping that our high priority, our number one priority. But some of those goals would be, obviously, we're going to have some goals for the locations around behavioral based safety, number of observations, and then taking corrective action there. We're going to have some goals around near miss reporting. So that'll be good. We have a goal around sending Our operations employees to attend our OSHA course so starting in late December and in 2025 we're going to have all of our operations team members go through a 10-hour OSHA course and I think that speaks volumes for developing our future leaders, right? We're going to empower them, we're going to give them some knowledge, we're going to give them some OSHA training so they'll understand When we talk about machine guarding, you know it's really important and there's some OSHA standards around that and walking and working surfaces and confined spaces
Beckman - 28:01 and things anyway gives those guys some knowledge. We're going to take that Steven a step further and we're going to send our operations managers and location managers to a 30 hour OSHA course. Let's give those guys some real skills. Let's develop these leaders. Really excited to implement some OSHA training for 2025. Hey, we've got a number of corporate safety goals we're working on. As I mentioned a couple of times, we're going to roll out the new behavior-based safety program, the updated rail safety training, we're going to improve our fall protection training, We need to roll out an incident reporting and investigation standard. As well, we're going to make some improvements around the hazmon or a critical safety device program.
Beckman - 29:02 And then really, we do need to spend some time as well on our onboarding process. So we hired new employees, obviously, and right now our process maybe is a bit disjointed. We've got some different checklists between human resources, between safety and operations, We need to come together with a little more streamlined and effective plan to help our location managers train our new employees and just make sure they're set up for success. And we've got some more safety initiatives than that, but those are the higher level things we're going to be working on. And I do think it will make a difference. And lastly, Stephen, I just want to say it's called a safety improvement plan because that's key to this, right? Every year we need to improve.
Beckman - 29:46 Every year we need to do better. Every year we'll learn from some of these incidents and we're going to take corrective action to make sure it doesn't happen again. We should improve every year and that's what we're going to do.
Kilger - 29:56 Wow, it sounds like 2025 is going to be busy for you guys but that's great and I am really grateful that you're willing to you know come on to our podcast and talk about this because one of the great things about the grain industry is I feel like safety is on all of our minds and The more we share as an industry overall, the better, and the more we can kind of steal safety ideas from each other, the better. So I really appreciate you coming on and talking to us today about safety at CGI.
Beckman - 30:30 Let me just mention this, I like how we're wrapping up the call. I agree with you 100%. I had an old boss of mine that said, Stuart, there should be no secrets in safety, right? Our goal is to keep people safe, keep people going home, and if we can learn from other grain companies, great. We want to learn and we want to improve and I hope that some of your listeners will learn a few things from this podcast as well.
Kilger - 30:55 Me too and I hope that you'll be willing to come back on maybe in a year maybe some other time so we can talk a little bit more about how CGI how the how the safety plan is being implemented and you know maybe pick your brain about some future safety tech and things like that it's always fun to talk about.
Beckman - 31:13 Love it I'd be happy to Steve and I appreciate you having me on your show.
Kilger - 31:16 Yeah happy to have you and thank you everyone out there for listening until next time stay safe. And that's it. That's all. Thanks Stephen. Yeah, hopefully it wasn't too bad. No. How was it?
Kilger - 31:32 It went well. I really liked your answers. You did great. It'll be fun editing this and getting in there. I like the podcast format because it gives us both plenty of time to kind of just talk. I mean, the whole idea was it was supposed to be like a conversation at a trade show. I'd have on a trade show.
Kilger - 31:50 And just not having, you know, that time limit that video has sometimes where you can just, yeah, let's, let's chat. Let's tell stories. Let's, let's get involved. I really liked the podcast format for that. And I appreciate you coming on and talking to us about because you know, like I said, it's fall. It's a good time to everyone to rethink their safety plan in the coming year.
Beckman - 32:11 Yeah you know of course it's got slot harvest for most of our locations or lots of our location in corn and bean country whatever so it's busy but with the dry weather we'll wrap up here in a couple of weeks and then we need to focus on what are we going to do next year so the so the
Kilger - 32:27 planning is good to come up with our plan very soon yeah and i mean this is the most dangerous time of the year right harvest yes grains moving around Bins are being filled and emptied. It's the most dangerous time. It's busy and the moment stuff gets really busy, stuff also starts to, you know, you start to slack. Suddenly you don't put away that extension cord, you just leave it there.
Beckman - 32:51 And we get things like fatigue sets in and complacency sets in and just a lot of things can happen. But so far so good. We've had a pretty good fall run so far. Let's hope it stays that way.
Kilger - 33:04 Yeah, definitely. I mean, I have to report on those stories and it's never fun. I never liked being like, oh, someone, you know, was engulfed in a grain bin today. Like that's never a fun story to write up.
Beckman - 33:17 Yeah, bad for the business, bad for our industry, but.
Kilger - 33:21 Well, thank you again so much for talking to me. I will be in touch. I'll send you a copy of this when it's done and you'll be able to listen to it. And if there's anything off or wrong with it, Just let me know and we'll edit it or re-record or whatever you got to do.
Beckman - 33:35 Okay. All right. Very good. Hey, so Stephen, wouldn't you think you'll send that to me later this week or next week or it's no rush, but just when do you think?
Kilger - 33:45 Early next week at the latest, like Tuesday, Wednesday. I'm going to try to get it done over the next couple of days, but we'll see. I got some other editing projects I have to get done in the, have some editing projects in the chamber already. So hopefully I'll be able to finish those tomorrow, be able to work on this.
Beckman - 34:02 No rush. I'm going to travel next week to do some other safety training, whatever, but I'll have a chance to look at that maybe next Thursday, so certainly no rush, but if that works for you, that'll work for me.
Kilger - 34:14 Awesome. Thank you. And thank you so much for agreeing to talk and getting this all scheduled. I know it was a bit of a pain. It was a lot of pain for Peter. It all worked out in the end and I'm glad.
Beckman - 34:26 It certainly did. So, hey Steven, if you got anything for me, let me know. We'll chat again sometime soon, I'm sure.
Kilger - 34:31 All right. Awesome. I'll talk to you soon. All right. See you, Steven. Thank you. Bye-bye.