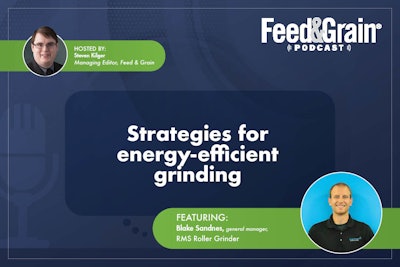
In this installment of the Feed & Grain Podcast, Steven Kilger, the managing editor of Feed & Grain Magazine, engages in a conversation with Blake Sandnes, the general manager of RMS Roller Grinder. Together, they delve into the crucial topic of enhancing energy efficiency within feed mill grinding systems.
Tune in to explore key considerations for feed mills in equipment selection, and uncover the substantial savings that can be realized through the adoption of more energy-efficient practices.
Steven Kilger: Hi, everyone, my name is Steven Kilger. I'm the managing editor of Feed & Grain Magazine and the host of the Feed & Grain Podcast. I want to thank you so much for joining me today as we dive deep into the issues affecting feed manufacturing, grain handling and other allied industries.
Today I'm speaking with Blake Sandnes general manager of RMS Roller Grinder. We're talking about the improvement of energy efficiency in feed mill grinding systems. What feed mills should be on the lookout for when they're selecting this equipment, and what kind of savings they can expect by implementing a more energy-efficient grinding process.
But before we start, if you're listening to this on a podcasting app, please rate us and subscribe. If you're listening online, sign up for the Feed & Grain newsletter, Industry Watch, to see the latest podcast and stay up to date with all the latest news from around the industry. Now on to the show.
Kilger: Hi, Blake.
Blake Sandnes: Hey, Steven, how are you?
Kilger: I'm doing all right. How are you?
Sandnes: I'm doing good. I'm doing good.
Kilger: Excellent. Can you tell me a little bit more about yourself what you do with RMS and maybe a little bit about RMS itself?
Sandnes: Sure. My name is Blake Sandnes. I've been with RMS Roller Grinder for going on 10 years. I'm currently the general manager but started in engineering with RMS, then worked in sales, and am now kind of helping to oversee a vision for where RMS is going and some of the things that we want to do. RMS is an equipment manufacturing service provider for roller mills. A lot of the industries that we serve are primarily rooted in the feed industry, the manufacturing of feed in feed mills and such and a lot of it is in ethanol plants, soybean processing, as well as breweries and distilleries. We also dabble in a lot of the industrial market.
So our roller grinders, though rooted in the ag feed industry are used in a lot of different industries as well. Not only do we manufacture it, but we also have the crews and ability to go out and service own and support the equipment wants to spend out in the field. Myself, I am grew up in the Sioux Falls area, just south of Sioux Falls, South Dakota. I have a wife by the name of Amy, and two beautiful daughters that are seven and five that keep me on my toes all the time.
Kilger: So energy efficiency is just a huge topic in the industry. Everyone's trying to squeeze a little bit more out of their process. Can you provide a little bit of an overview of current energy consumption trends in animal feed milling, specifically focusing on the grinding process?
Sandnes: As in any industry, all the input costs continue to rise. I think specifically for feed mills, they're really trying to look for ways to reduce those operating costs. One of the costs that, generally speaking, feed mills have actual control over is their energy consumption. It's in the selection of the equipment that they choose to purchase, or how they choose to upgrade it, or the controlling of the equipment. It's just an area in their day-to-day lives that they actually have some control over. The ability for them to look for ways to improve it ultimately helps them either maintain or improve their margins.
Kilger: You see a lot of it nowadays with like alternative energy sources, right? Solar panels seem to be the new frontier in feed mills, and things like that. But sometimes it's best just to reduce the energy consumption within the milling process itself. Can you talk a little bit about some of the challenges and concerns related to animal feed milling? Is there kind of only so much you can do? What's out there?
Sandnes: In some areas of the country, different energy companies can, depending on their available grid, actually require some of these high energy demand facilities like a feed mill to temporarily either limit production or face penalties in the form of peak demand charges or higher rates. They try to limit it, so that way, they're not putting too much strain on the grid at peak times of the day. That has an impact on the operations of a feed mill. Just making sure that they can get the feed produced in a day or the costs to ultimately manufacture that feed. The other thing that I think a feed mill struggles with or has to contend against is finding that balance between optimizing for feed efficiencies. Meaning, how fine they can grind feed in order to give the animal the proper and the best way to gain efficiencies, versus the cost to actually produce that. Typically, when you grind finer, that requires more energy and that also comes with a cost. So finding that balance between the most efficient way to add weight to an animal while still being able to produce feed at a reasonable cost.
Kilger: So crazy to think about that, right? Because you hear about those programs. Not so much here, I live in southern Wisconsin, but across the nation, you do your laundry at night, away from peak time, and you get a little break. But it's crazy to think of a feed mill, with a huge electricity bill, is still thinking of and required to do that kind of cost analysis in their day-to-day operations.
Sandnes: Yeah, absolutely. It happens more often than I think people really realize and think about it. Not being able to do your job, basically, during the middle of the day, because of the amount of energy that some of these facilities are just required to run.
Kilger: Definitely, I can't imagine it's gonna be better in the future. I mean, these are going to be problems that continue to evolve and get more pressing for everyone. Energy costs money, and there's, with fossil fuels and everything else, there's more and more demand to use less and less of it. So it's a really important issue going forward. One of the big users of electricity is the grinding systems in feed mills, can you talk a little bit about how people might be able to become more sustainable by adding cost savings to their milling process based on how they run their grinding systems? You talked a little bit about fines versus a coarser grind, and things like that. Is there anything else that springs to mind?
Sandnes: I think everything kind of goes back to really reducing that cost per ton to manufacture feed in some of those areas is a design of some of the equipment. But I think this kind of goes back to more energy-efficient motors that drive configurations and the selection of the electrical starters that the facility may choose. A lot of those design configurations can impact the cost associated with producing a ton of feed, as well as just like this is a point we'll probably talk about later in the conversation, but selecting the right equipment, and then operating it only when you really need to operate it, right. It's like turning the lights off in the room, do you turn the lights off when you exit the room or do you just leave them on? It's the same for this equipment, if you're not really using it, make sure that when it's going idle it shuts off for a period of time. And so I think when feed mills and operators are thinking about the sustainability and the costs associated with that they're having to contend or have the ability to affect it in all those different ways.
Kilger: Yeah, definitely. As you mentioned earlier, motors have become more energy efficient. Can you talk about some of the other equipment that over the last 10 years, it's things may have changed quite a bit from your old grinding system that might be able to help save you some money you're at now?
Sandnes: Yeah, absolutely. And I think it's not just in the new systems. But feed mills are working much closer with their power companies themselves, really to conduct full site energy evaluations to really find out where that energy can be improved from a consumption side. Honestly, a lot of the power companies are offering some sort of rebates or incentives for feed mills that implement those types of energy-saving reductions. Some of the things that RMS has helped customers with, is the selection of different motors.
The selection of using maybe a VFD and some applications versus a standard starter, which impacts their peak demand charges. One of the styles of roller mills, specifically that RMS manufacturers, for grinding equipment is the style of a roller mill that they select, because of some of the energy charges that they may face or some initiatives that their companies have. I mean, I think it's all about reducing the friction in the grinding application to really maximize the kW per ton when you're talking about energy costs for a facility.
Kilger: Can you go a little more into detail about what changes RMS has made over the last few years to make the machines that you guys sell?
Sandnes: More efficient. So obviously, we are always supplying the motors that have the highest energy ratings that we can find. That's one big thing. So we always try to use high-efficiency motors on there. The other thing is, is really making sure that we're selecting and designing our drives in such a way that limits the number of belts and configurations like that. Anytime you add belting, you have power loss because of the power transmission from the motor to the rotating object, and in our case it would be the rollers themselves.
One of the big advancements that we've designed is actually in what we refer to as our VersaMill. Basically, the inverse of a mill is a direct drive roller mill that gets away from or eliminates all the belts completely and also has a kinetic energy recovery system. So we can take that normally lost mechanical energy, and re-distribute it back around to powering the motor. That's something we've really been working on or refining for the last three to five years and seen some pretty good success stories with customers in that regard.
Kilger: You guys worked pretty closely with Easy Automation as well. Are some of those automation systems, or process control systems, able to be implemented to help improve energy savings?
Sandnes: That's a big part of it is making sure that all these individual pieces of equipment are connected through a system like Easy Automation, and making sure that they're operating in sync with each other. But also kind of going back to, if they're not being utilized, the ability to know that will allow the shut down of the grinder because the bin is full. And we don't expect to have to grind for the next hour versus keeping it running over a period of time. And just the ability to interconnect all those pieces. Equipment is a big part. Easy automation, as you mentioned, is a company that we've worked closely with to be able to really maximize and get peak performance out of our grinding equipment.
Kilger: With the example with the lights, right, it's a lot easier if you don't have to remember to turn on and off the lights at all, you just have a little sensor that turns off for you, you don't have to worry about it.
Sandnes: That's why they have automatic lights in so many rooms nowadays, because it's so much more energy efficient, those little things can be applied to the industrial market as well. We just don't think like that, typically. But I think that's becoming more and more of a conversation point in consideration for these feed mills that are being built and developed.
Kilger: When you walk into a feed mill. Now, this is a little bit of a tangent, but all their lights are still going up to these second, third, fourth floors and where no one is, and it's just a distributor or whatever up there. All the lights are beaming down when you visit and you're like, yeah, there's don't need to be on right now. Back on topic. So what advice would you get when selecting grinding equipment? Say I have a new mill coming online? I'm shopping for grinding equipment and things like that, what factors would you consider if you were in that situation and you were picking out new grinding equipment? What should feed mill managers be thinking about during that time?
Sandnes: It always goes back to what your current objectives for the equipment you need now, but you also have to think about the future state as well. 15 years out, in regards to what types of materials am I going to be grinding? Primarily it's corn for a lot of applications. But there are applications where maybe it's not just corn, but it's also more on the tonnage. So how many tons do we feel like, we're going to have to produce in an hour a week or a day? And thinking about that in such a way from a sizing of an equipment perspective, making sure that you're sizing it for today to get the job done today, but also for the future. That's one of the things that I think we do a good job of is kind of going through that with the customer and asking those questions.
We select that right piece of equipment, so you're not building too big of a roller mill for the current state and future state that you're just kind of wasting energy. On other things is just going back to the design of it, right, making sure that you're using the most energy-efficient designs out there in the market. There are always equipment manufacturers and companies out there that are coming out with new technologies, you have to really do your homework, ask the questions, go visit them, be there with them to really understand how is this gonna work for me and my feed mill and the initiatives that we're trying to accomplish?
Kilger: You mentioned earlier that you had already had some customers, upgrading systems or using systems. Do you have any examples you can share with us any stories, any outcomes, or kind of benefits that you've seen from people upgrading their systems?
Sandnes: There are always customers that have maybe had some older legacy roller mills that may have been 15-20 years old. And again, it's like any equipment that's been out there for 15-20 years. The energy savings from just putting on more energy-efficient motors or the design is there. But one of the ones that sticks out to me is we had a customer who had a standard roller mill. They flipped over from using that standard roller mill and selected it to go with a VersaMill, not from primarily the energy consumption side, but because of the versatility that they were looking for in their application.
However one of the benefits that they saw and received was a reduction of about one kW per ton, which ultimately resulted in about $20,000 a year in annual energy savings for them because of what their rates are. The other nice thing because of this reduction in energy costs, and the system they selected, they also received a rebate from their power company that they work closely with which has a big impact on their business and their bottom line.
Kilger: Those numbers don't seem huge, but they add up really quickly to really big savings. I mean, $20,000, that's half of someone's salary. Those are all the questions I have. What did what did I miss? Anything else you'd like to talk about that you feel you didn't cover?
Sandnes: No, I think you asked a lot of the main driving questions that feed mills are asking or shouldn't be asking it considering in regards to the grinding methods and energy consumption.
Kilger: It's hard to imagine what an old oil mill is, right? Because you mentioned, you know, 15-20 years, probably anything over the 10 years is, heck, anything over five years, be considered out of date now, which is, I think, hard for a lot of people to wrap their heads around, especially with some of the older mills out there who have been using the same equipment for a long time. So there are a lot of opportunities for them to upgrade and then have that equipment slowly pay for itself.
Well, thank you so much for talking to me today. I really appreciate it, and I hope you'll come back soon.
Sandnes: Absolutely. I appreciate the opportunity to talk with you and look forward to talking on other topics again in the future.
Kilger: All right. Bye, everyone.