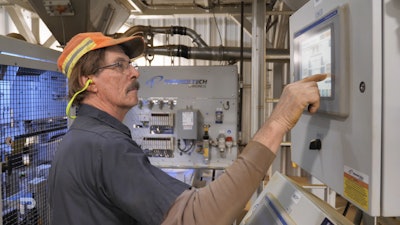
Founded in 1956, United Animal Health, Sheridan, IN, offers livestock nutrition and health products and is dedicated to providing research-based solutions that create value for its partners in animal agriculture.
With more than half a century of experience, United Animal Health sets itself apart from the competition by offering superior service and high-quality products.
Equipment as an ally for future growth
United Animal Health has changed immensely over the past 20 years, especially the Gridley facility which has been repurposed into a blending facility. This important change has brought value to the company, allowing it to attain future growth.
“We have grown internationally," says John Stella, plant manager. "The motivation behind the change here at Gridley was the facility was getting old."
By growing internally, this meant upgrading their packaging operations with new equipment, better suited for the free-flowing products they handle and allowing them to reach better production rates.
“It needed to be updated by bringing in this new equipment. Making the revisions and changes here has made this facility a viable option for United as we move forward.” adds Stella.
No more “losing money in the dust”
To ensure success, United Animal Health required a company with extensive knowledge of the agriculture and animal feed packaging industry. They turned to Premier Tech because they understood the unique challenges associated with the industry, especially those related to free-flowing materials and product loss.
Containing fine particles in our system is critical to achieving maximum efficiency and controlling dust. Improvements made in this area bring value to United Animal Health and our customers explains Jon Wilson, production supervisor.
The equipment Premier Tech installed at United Animal Health is a PTH open-mouth bagger. This simple yet reliable cell comes in a compact footprint with a user-friendly interface.
The bag placer moves a single bag from the stack of bags in the bag magazine to the bag opening section. The bag is opened and hung onto the spout. The gusset of the bag remains closed and dust-controlled filling of the bag is completed. Bag top control is maintained by the robotic ANDY auto exit ensuring reliable delivery of the filled bag to the sewing system.
“The one challenge that we've had was product loss because too much product comes out of the bag when you're filling it,” says Walter Ney, project manager. “Now, we have less than 1/2 a percent of product loss. If you look at our dust collector the amount of dust that's going into that dust collector is minimal, almost null.”.
For packaging of large amounts of bulk material, Premier Tech also installed a big bag filling machine. The equipment is engineered in such a way that the entire filling process can be completed with the operator remaining in one position thus increasing productivity. Again, efficient control over dust emission was crucial in this part of the process.
“At the Gridley facility, in the past, we filled totes at an elevated level," says Scott Ringger, QA/QC regulatory manager. "Typically, it took more than one individual, very dusty conditions. Today, it’s on the ground level, and typically it would take only one individual to fill those totes in a dust-free environment. The conditions today are much safer than in the past”
The new packaging system was engineered with flexibility in mind as different recipes are filled in different sized bags. With a user-friendly interface, the new bagging machines can package numerous feed products and recipes in various sized bags quickly and simply.
“The equipment here has given us the opportunity to package that like we never would have been able to do before," says Stella.
There, every step of the way
The installation of new equipment can sometimes be perceived as challenging by plant operators as they have come to be used to a way of working and might be worried about the underlying learning curve.
“I think for the most part our guys, including myself, where a little bit intimidated by the equipment after visiting the factory, but Premier Tech did a nice job getting us started and getting the bags per minute that we expected to get," says Ney.
Premier Tech is committed to supporting its customers throughout the equipment purchasing process and offers the most comprehensive programs in the industry to support its customers in the lifecycle of the equipment, including around-the-clock free technical support 24/7.
“I’ve been around for a long time and have not seen a company that does as well with support," says Jon Wilson, product supervisor.