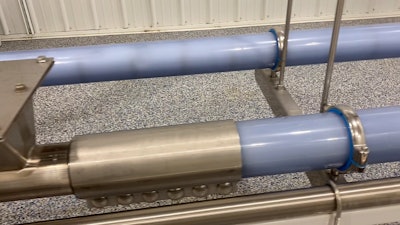
When feed processors blend materials to produce food for fish, cattle, swine, and poultry, they use conveyors to move product in pellet, flake, chunk, and powder form. To meet strict safety and compliance standards, such as the Federal Food, Drug, and Cosmetic Act, these processors now utilize ATP testing to monitor equipment surfaces for microbial growth.
Add to this the need to minimize cross contamination of products or ingredients with allergens after production changeovers, and more processors are realizing that the traditional means of cleaning conveying equipment may not be sufficient to meet today’s rigorous compliance requirements.
In the feed processing industry, when conventional conveyors need to be disassembled, cleaned, and reassembled to reach all exposed internal surfaces, potential downtime can extend to days. If this proves too onerous, some processors dedicate separate conveyor lines to specific products, which increases capital equipment costs, labor, and the production space required.
As an alternative to speed the process, feed processors are turning to tubular drag conveyor systems, which gently move product through a sealed, enclosed tube using a drag cable and circular discs pulled through on a loop -- ideal for delicate items.
Because tubular cable conveyors are enclosed, these systems can be quickly and effectively flooded with water, flushed, rinsed, cleansed, and thoroughly sanitized without disassembly – a process called “wet cleaning.”
Clear tubes can be chosen as an option for the conveyor system to provide greater visibility into the cleanliness of the equipment and the cleaning process as it occurs.
For added food safety, processors can choose to add a unique inspection option that enables the running of a small, lighted camera system internally through the tubes, with video viewable on a smartphone via an app. Usually, this level of inspection is performed on an as-needed basis to further verify or document cleanliness.
This clear tube system is transparent except where the clamps are located, so feed processors and packagers can visually check at any time, and the internal camera system enables seeing “every nook and cranny from the inside”. This, along with regular ATP testing, provides processors with the confidence that they are reliably meeting all necessary QA and food safety standards.
Compared to air conveyor systems, the approach can also run significantly more product an hour with less downtime and less potential breakage.
For the feed processing industry, the wet cleaning capability is advantageous when dealing with a wide variety of products. As processors respond to the need for greater safety, flexibility, and efficiency, tubular conveyors with the ability to wet clean are an important tool to consider.
Del Williams is a technical writer based in Torrance, CA