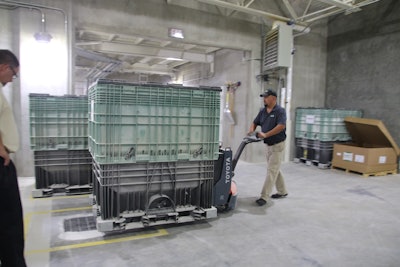
It is rather amazing the number of small to medium feed mills (often home mixers at farms) that operate without a forklift.
I'm not talking about a hand-operated pallet jack that simply move loaded pallets from one place to another — and always on very flat and hard surface. Instead, I am referring to the forklift that can lift pallets up to a considerable height. Mills without a forklift often store pallets of products, always in paper 50-pound bags, or just transfer the mixed feed directly to an on-site silo to be used for feeding the farm's animals.
So, why would such feed mills need to lift pallets? After all, a pallet jack is about $10,000, whereas a forklift is easily in the range of $50,000 plus fuel to operate as opposed to muscle power! The answer is big bags carrying 2,000 pounds each. These bags usually have an opening at the end to unload their cargo. So, in order to unload them, one needs to lift them up — hence the need for a forklift to handle big bags.
Why use bigger bags?
Next, we need to answer why we should use big bags as opposed to stacks of 50-pound paper bags. Especially in countries where labor abounds and is inexpensive.
Well, in this latter case I must admit that having an expensive forklift may be counterintuitive, but such countries are not the focus of our discussion. Here we refer to regions where labor (that is experienced labor) is both expensive and high demand — and always in short supply. In this case, a big-bag offers a singular advantage: costs savings.
As a general rule of thumb, a ton of animal feed products costs about $25 when offered in a big-bag container as opposed to 50-pound paper bags. Of course, big bags are not free, but the cost of filling and sewing 40 paper bags, then stacking them up, and securing them with plastic roll film is higher compared to using big bags.
In terms of marketing, paper bags — often with a company logo and color scheme offer certain marketing advantages, but that is another story that usually concerns larger commercial feed mills that offer products to the open market.
How forklifts can save money
Going back to our forklift for the smaller feed mill, we need to handle 50,000/25=2,000 tons to justify the expense. Admittedly, this is a rather steep number for small feed mills receiving or delivering products in big bags. In my experience, however, there is another $25 that can be saved by having an in-house forklift.
Most international, interstate and national trucks do not have a hydraulic back door to facilitate the use of a pallet jack. Equally, most small feed mills do not have a docking platform to accept direct deliveries from such trucks. Thus, there is an intermediate transportation cost while pallets of products are transferred from large trucks to those more suitable to deliver products at small feed mills. The extra work is easily another $25/ton going up to $50/ton as total savings.
Finally, now that a smaller feed mill can receive big bags directly from large trucks, there is no reason to buy from local nutrition suppliers that need to charge their own margins. Instead, smaller feed mills can shop around from larger suppliers from a wider radius. If they can organize their orders in full-truck shipments (often buying several raw materials from a large supplier), then the whole transportation cost can decrease even further. Thus, the original $50/ton can go even up to $100/ton — and this has been the average experience of mine across many regions. Now, dividing 50,000/100 gives 500 tons, which is a more appealing number.
An oversimplified example of cost savings
Let's assume a 1,000-sow farm has its own feed mill and buys premixes (basemixes) to be included at 50 pound/ton.
Now, assuming for simplicity all feeds in the farm are made using the same inclusion rate premixes, we can calculate the annual consumption of premixes as follows: Each sow produces on average 28 market pigs (more or less in your case), with a final weight of 280 pounds, and a whole-farm feed conversion rate around 3:1. With these numbers we calculate that his farm will need to manufacture close to 12,000 tons of feed.
Now, multiplying this with 2.5% we get 300 tons of premix. In other words, in two years the cost of the forklift will have been retrieved, assuming a bit extra for fuel/electricity/battery. Of course, forklifts last longer than that and if we discount fuel, maintenance, etc. we have a savings of 300x100=$30,000/year (from which we can deduct the above expenses) — all other things remaining equal, which never do.
Of course, this oversimplified example is just a point of discussion with your feed mill manager and purchasing department. You may be positively surprised with the savings offered by such simple purchase (OK, you also need a trained driver) in the long run.
Of course, in certain regions you can rent or even lease such equipment, but that is something you need to discuss with your accountant. All in all, in more cases than not, you can take advantage of little-known profit sink holes in handling raw materials in bags as opposed to bulk.