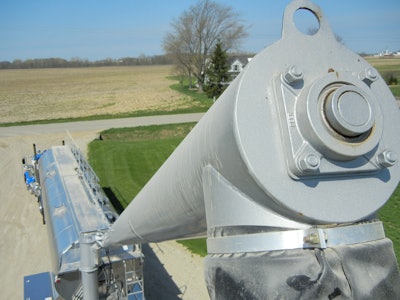
The Food Safety Modernization Act has been compared to a freight train barreling down the tracks. We may not know exactly what it will look like or when it will be here, but you can hear it coming. It’s a frightening sound to many, but there is no course diversion, and no one to slam on the brakes. It will be up to individual facilities to prepare themselves to avoid getting hit. But luckily, no one is alone in this fight; there are associations, academics and others working to help them off the tracks.
Commitment to customers
For the proposed transportation rule, the industry has a big ally: the manufacturers of feed bodies and trailers. They’ve developed features that will make compliance easier, and will continue to innovate once the finalities of the law are known.
“We are driven to provide solutions to our customer base,” Jim Ross, owner and director of sales and service of CEI Equipment, says. “As they are confronted with challenges, we are going to respond as their feed transportation solution.”
Feed bodies have come a long way since they were introduced as alternatives to bags in the 1930s. The market has demanded changes in safety and sanitation, and the manufacturers have obliged with both standard and customizable features that suit any situation.
“We have partnered with our customers, to make sure they get the things they need,” said Travis J. Hensley, national sales manager for Hensley Feed Transportation Equipment. “Anytime you let the free market reign, you usually end up with the innovations you need and a thriving economy. Instead of telling [our customers] what will work for them, we listen to their needs, and develop a solution that works.”
Air flush-outs
Flushing the feed body regularly, certainly between shipments of feed that will go to different livestock, will be a necessary step to ensure compliance with FSMA.
An air flush or “dry clean” is a feature offered by many manufacturers and may circumvent the need to do full flushes. A pressurized air system is attached to the top of the truck or trailer. The driver then uses a nozzle to break up any deposits within the individual chambers, allowing the stuck grain to flow down to the still running auger.
This is one of the easiest ways to keep the interior of feed bodies free of any extra material, while adding value to shipments. Some equipment manufacturers also offer a chance to remove additional debris once the truck has returned to the feed mill.
“We’ve attached nozzles to key positions, so when a feed mill has central vacuum systems, they can blow down one end and have a vacuum on the other,” Terry Medemblik, president of Walinga USA, Inc., explains.
Modern feed body interiors are designed to ensure that as little material is left over as possible. Designs that encourage the flow of material to the auger, and fewer seams and rivets for the material toget stuck on, means less time spent unloading and doing air flushes.
“We’ve improved the flow ability of the tank, so that a majority of the feed will flow out, and if not, we offer an air cleanout,” says Hensley. “We have also reduced the amount of compartments that are in the tank itself. Feed, no matter what ration or type of livestock, has a tendency to hang up in the corners of the compartments. With fewer compartments, there are fewer corners for the feed to hang up on,” he continues.
Liners are available for feed manufacturers who wish for even less cleanup. They virtually eliminate any obstacle that feed can get stuck on, leaving a clear path to the auger below.
Augers
Augers have also been improved; not only unloading trailers faster than ever before, but with tighter fits that leave less of the material behind to remove.
“We’ve designed our troughs to sit as tight as possible to the trough auger,” Medemblik says. “The auger has very little flex, combined with the tightness to the trough, giving you the maximum cleanout.”
The more feed that leaves the trailer through the augers, the less that will be left over to flush out, so the driver can spend more time moving feed.
“It doesn’t take the place of flushing, but it helps to reduce the carryover,” Doug Tecken, product manager at Sudenga Industries, Inc., points out. “It does a very good job getting material to the vertical, and keeping it there. After a demonstration with a 35-pound/cubic-foot Land O’ Lakes finishing ration, when we do a cleanout, there’s less than a gallon or two of material that comes out. This is very little considering the size of the feed body.”
Sanitizing trailers and tires
Poultry producers have long had to deal with the ravages of various strains of avian influenza, which can quickly wipe out an entire flock of birds.
This has led to the development of increasingly advanced biosecurity measures, which often involve the washing and sanitation of vehicles as they enter the farm. With the Porcine Epidemic Diarrhea Virus (PEDv) already responsible for the deaths of millions of pigs, the pork industry is switching to similar programs.
“They want a trailer that is disinfected before they enter the farm, and when it leaves,” Hensley said. “One of our customers, a large turkey and hog producer in western Ohio, runs their feed trailers through a disinfecting wash, bake the trailer, sprays them a second time and bake them again — just to make sure the virus is kept at bay. It’s time-consuming and expensive, but this process has been effective.”
A system that sprays disinfectant onto the tires before going on to a farm and when leaving is a common option. The tires are usually the only portion of the truck that comes in contact with the ground, and the dirt that it collects can house pathogens.
“There is a tank on our trailer with an electric pump on it with spray nozzles located over the tires,” says Roger Malin, sales manager for CEI Equipment. “Once the unit comes off the farm, the driver activates the pump, which douses the tires over a few rotations. It is a fairly simple process, but an effective one.”
Washing programs
Sudenga’s Tecken suggests developing a washing program with your company’s drivers.
“I’m a big believer in washing programs,” said Tecken. “Have policies for your operators, whether it is washing every day or every load. This will eliminate any material coming off the trailer or the tires, along with making the equipment last longer and look nicer. It may take time, but you’ll come out ahead by doing so.”
Feed bodies can be designed to have fewer trouble spots for material to become stuck. This benefits in house washing programs, and is appreciated by farms that require vehicles go through a full wash before entering.
“A protective coating that makes it easier to clean your equipment; it helps eliminate the nooks and crannies that are difficult to clean out,” Ross adds.
Moving feed is an inherently dusty business, and some older spouts don’t do much to control dust and spillage. So, Walinga has also worked on minimizing the amount of area that material can land on.
“We’ve minimized the area where you can have residual material splash up and lay on the roof and dividers,” Medemblik explains.
Changing times
While FSMA is coming like a freight train, most feed manufacturers should not be afraid of it. Biosecurity and sanitation have been on the radar for years, and most facilities are already in, or close to, compliance.
“People have started to become very aware of biosecurity,” Hensley explained. “Other countries may be farther ahead than we are, but it is coming down the pike.”
“I don’t think it’s going to revolutionize our industry,” Ross ventured. “I think it will broaden the scope of things already being done,”
Whatever comes from the final ruling, rest assured your preferred feed body manufacturers have made great strides over the last 10 years. Many available features will help you stay in compliance with FSMA, while still saving time and money on your transportation needs.
“As operators start looking at the transportation aspect of FSMA, the feed trailer is now playing a far more critical role in the equation,” said Medemblik. “We’ve been telling our customers for a long time; the feed trailer is no longer a necessary evil — it can help you accomplish whatever your goals are.”
Technology, Innovation Make Feed Transportation Safer for Operators
The Food Safety Modernization Act has brought sanitation features to the forefront across the industry, but it is far from the only thing that feed body manufacturers have been tinkering with over the past few years. Several innovations to improve safety, capacity and traceability, are either already available or are on the horizon for the industry. So, what should feed manufacturers be excited for? Some of the industry’s experts weigh in with their personal favorites.
Sudenga Industries, Inc.
“The TRAM Restraint System has been a big development for preventing falls,” says Doug Tecken, product manager at Sudenga Industries, Inc. “When attached, it will follow the driver along the roof of the feed body, giving them protection no matter where they are. It’s a significant improvement to driver safety.”
“But what I’m most excited about is the new Atlas, because of the unloading speed,” Tecken added. “It averages 7,000 pounds/minute, and that’s across the whole trailer. The rear compartments are even faster, getting up to about 8,500 pounds/minute.”
Walinga USA, Inc.
“When it comes to fall restraint fall arrest we have several different avenues,” Terry Medemblik, president of Walinga USA, Inc., explains. “The TRAM system is a body harness with a lanyard that attaches to an arm that lifts and slides along the roof assembly. Another is air operated folding hand rails that are attached to the roof assembly, as well. The operator switches them on at ground level and by the time he climbs the ladder, the hand rail is up.”
“When the driver pulls onto the farm, and there are overhead power lines a voltage sensor can be a life saver,” Medemblik continues. “When drivers start to swing the boom auger over to the bin, if they get to close to a power line an audible alarm will go off. The closer it gets, the louder the alarm will sound. If these warnings are ignored, the system will automatically shut down the auger controls.”
“Another area we have seen a fair bit of concern expressed by our customers is ‘roll overs,’ as this is also a safety issue in transportation, it suffices to say that we have also addressed this in the past with our customers with the introduction of a Low Center of Gravity ‘wedge style’ tank several years ago, and then perfecting the design, as the concern has grown stronger in the past year, with a newer, more conducive low center of gravity trailer,” Medemblik says. “This unit coupled with roll stability provided by the suspension suppliers has greatly assisted in achieving the end goal of minimizing ‘roll overs.’”
CEI Equipment
“The most significant item we’ve added over the past few years is a sliding arm fall-restraint device,” explains Roger Malin, sales manager for CEI Equipment. “This gives you fall protection both into and off of the trailer, covering the front back and both the sides. Although there are not a large number of accidental falls; when they do occur it can be very serious.”
“There’s an industry trend to lower center of gravity trailers to enhance stability and reduce rollovers,” Jim Ross, owner and director of sales and service of CEI Equipment, says. “We’ve introduced the PACER NSL as a solution to significantly lower the center of gravity while maintaining adequate ground clearance.”
Hensley Feed Transportation Equipment
“Fall restraint protection on top,” Travis J. Hensley, national sales manager for Hensley Feed Transportation Equipment names as his favorite safety feature. “For one particular customer, we’ve started installing grates to keep people from slipping inside.”
“We’ve added roll stability, pretty much standard in the industry,” Hensley said. “Though it’s not particular to Hensley it was invented right here in northern Indiana, by the BendixCorp.”
“The big deal for us is the center of gravity,” Hensley states. “We were the first to introduce the low center of gravity trailer, and that is our latest and greatest. For the last year and a half we’ve been working on this project, to both bring it to market and perfect it. It’s a big deal because these tankers have always been heavy; rollovers have always been a problem, but feed trailer manufacturers have been sticking their heads in the sand until now, us included.”