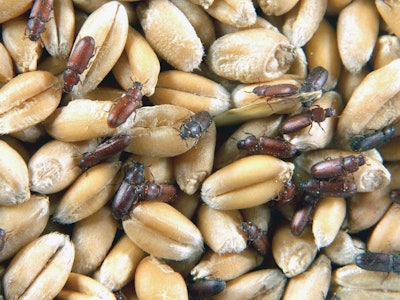
Of all the grain quality management aspects that a handling facility must contend with, insect control can be, excuse the pun, the biggest pest. Despite a manager’s best efforts to sample incoming grain for bugs, and clean the loading, transfer and storage equipment, insects always come back. In order to ensure pest-free delivery to the customer or end user, nearly all grain in commercial storage today will eventually be fumigated. But due to several factors, such as suspected insect resistance to phosphine and potential health risks posed on employees mishandling the chemicals, many companies today are seeking proactive pest control methods.
Facility sanitation is key to preventing pest population explosion, but the task of keeping an entire grain handling facility spot-free — especially during the busy harvest season — can be daunting.
To help prioritize facility sanitation efforts, researchers from the USDA-ARS in Manhattan, KS, and Kansas State University recently conducted an experiment to isolate the effectiveness of sanitation and insecticide treatments in elevator leg boot pits. Previous field studies conducted by the USDA-ARS’s Stored Product Insect Research Unit identified residual grain in the boot pit as having the second highest insect population density in a facility. That’s a problem because all grain that enters an elevator passes through the boot pit just before going into storage. Mark E. Casada, research agricultural engineer, USDA-ARS, explained, “By design of the elevator, virtually all grain goes through the boot, so if you have an infestation there, it’s the key place where your clean incoming grain has the opportunity to be contaminated by infested grain.”
A study published in the Journal of Stored Product Research in April, titled “Stored-grain insect population commingling densities in wheat and corn from pilot-scale bucket elevator boots,” recommended cleaning boot pits and applying residual insecticide on a monthly basis. The authors, Dennis R. Tilley, Bhadriraju Subramanyam, Mark E. Casada and Frank H. Arthur, based their recommendation on a series of trials using a model-scale modified elevator leg to comingle uninfested corn and wheat with infested grain residing in a removable boot pit.
One might wonder where the payoff lies in researching a well-known fact about grain elevators: Boot pits are dirty and hard to clean. But their aim was to provide more data on a focused aspect of an integrated pest management program — one that Arthur, research entomologist, USDA-ARS, said includes facility sanitation, aeration, fumigation and bin monitoring.
“Insecticides ... may help mitigate the spread of the insects, but cleaning is going to have the biggest impact,” Arthur said. “This study is meant to promote sanitation and cleaning facility-wide, but we’re emphasizing that this is an important dispersal point that managers should pay attention to.”
Confined space concerns
Recently OSHA has put renewed emphasis on requiring confined space entry permits in the grain industry. According to the National Grain and Feed Association, OSHA has issued numerous citations where boot pits were considered confined spaces.
Douglas Products, based in Liberty, MO, is a manufacturer of specialty chemical products for agriculture and other industries. Its CEO, Bill Fuller, said many of their grain customers have instituted a “no confined space entry” policy, preventing employees from going into the boot pits for cleaning.
“Of course they know the value of cleaning out the boot pit, but the problem is it now [may be a Permit Required Confined Space],” Fuller began. “A lot of the major elevators don’t want their employees in a confined space, so the boot pit may or may not get cleaned out often.”
John Mueller, president of Food Protection Services, based in Westfield, IN, suggested hiring a qualified service provider to manage pest control, including boot pit cleaning. Food Protection Services is a founding member of the Food Protection Alliance, a consortium of 14 companies whose mission is to provide safeguards and value-preservation services for commodities and finished products throughout the food supply chain.
“Due to OSHA’s changes regarding confined spaces in grain handling, we treat [every boot pit] like it’s a confined space and use atmospheric monitors to take readings both before we enter the confined space and while we’re in it,” said Mueller.
The Food Protection Alliance offers training to grain handling companies on proper procedures for entering any Permit Required Confined Space and stresses that the alternative to entering a boot pit for regular cleaning may be even more dangerous.
Once an infestation has passed from the boot pit into a storage bin, Mueller said, “any companies that prohibit confined space entry are now left having to fumigate by going in through the [bin] roof, which has its own inherent challenges.”
Fuller said he hoped the newly published report will convince grain managers to keep up with boot pit sanitation, despite the potential challenges they may face.
“We don’t want grain managers to be discouraged from cleaning and treating that boot pit,” said Fuller. “This study is a good reminder that [the boot pit] is an area that can contaminate your whole facility. It’s worth the [permitting] hassle and the hard work to get in there regularly.”
Cleaning recommendations
Whether handled by a professional service or your staff, Casada and Arthur’s general recommendations start with removing all grain out of the boot pit and cleaning up any spilled grain in the area around it.
“All sanitation must start with a broom and a shovel,” said Dick Bigler, commodity services manager for Douglas Products. “Starting with the grounds around the facility, it is necessary to keep the weeds down, make sure there is no dunnage or trash piled up around the facility and make sure that all spilled grain is picked up off the ground.”
In addition to cleaning the boot pit and surrounding areas, Casada and Arthur urge grain handlers to clean out all transfer equipment, such as conveyor belts and elevator buckets, depending on accessibility and how much residual grain is present.
“Understand that ‘clean’ to an insect and ‘clean’ to a person are two different things,” Food Protection Services’ Mueller said. “Most stored product insects can thrive on very little grain. Your objective is to clean in a manner to leave no residue. When cleaning is complete, choose a residual insecticide to get your empty bin [or boot pit] condition to zero insects. Remember, one fertile pair of weevils can produce millions of offspring. Getting to zero is your goal.”
Insecticide recommendations
Insecticides are an effective tool in getting a pest population to “zero.” The USDA-ARS/K-State conducted trials spraying ß-Cyfluthrin on their model boot pit, and recommended the treatment as a complement to monthly boot pit cleaning.
Insecticides may be applied directly to grain during the filling process, on the inside of the bin walls before being filled, or fogged into the atmosphere of a bin to reach the hard-to-spray area at the top, according to Douglas’ Bigler.
Note that all insecticide and grain protectant products must be applied at labeled dosage rates. The label is considered federal law and any action inconsistent with the label is a violation of EPA regulations.
Randy Scott, market development manager for specialty products for Central Life Sciences, based in Schaumburg, IL, said the chemistry his company offers the grain industry works two ways.
“Diacon® IGR is an Insect Growth Regulator and Centynal® is a contact insecticide,” Scott said. “In better than 90% of insect management situations, Diacon, when used with sanitation, proper loading, aeration and monitoring [SLAM], will be all the insecticide needed. When properly applied to the grain stream during transfer, Diacon can provide 12 to 18 months of control. The true weevils [Sitophilus spp.] are able to isolate themselves from the effects of Diacon, and that is where Centynal comes in.”
Centynal is a product that kills all insects on contact, and can be applied directly on grain or as a crack and crevice spray. “It has a much shorter residual, delivering 90 to 120 days of control,” Scott said. “Centynal and Diacon have no restrictions as to how grain can be used after treatment, including exporting worldwide. [Some products] can only be used on walls and surfaces, so always read and follow the labels.”
Douglas Products is close to introducing two labels for use on grain. “[We are] in the process of registering two new products: Deltec, an insecticide, and PreTec, an IGR, and both will be labeled for direct application to grain. We anticipate approval by the end of the year.”
Timing recommendations
While some grain managers argue their staff is already pressed for time, it’s important to keep up with sanitation practices in order for them to be effective. “The frequency of [boot pit] cleaning is important because of the insects’ lifecycle,” Casada began. “Most stored product beetles require six weeks or so to complete their life cycle, so cleaning at monthly intervals will disrupt that life cycle”
Ideally, a bin should be thoroughly cleaned every time a facility is shut down for maintenance, but that might not be an option for high-volume export terminals or country elevators during harvest season.
Casada said during busier times “a population explosion should not normally occur within a two-month period; so if you’re cleaning within the one- to two-month range, you’ll still be ahead of the game.”
Douglas Products’ Fuller added, “The practical answer [to how often to clean the boot pit] is ‘whenever you get the opportunity.’ If cost wasn’t an issue, facilities would have dozens of conveyors and transfer equipment, but they don’t. They’ve got one. They’re constantly in use, so you’ve got to take every opportunity to clean it out.”
Making boot pit sanitation a top priority can help reduce the presence and spread of insects and may ultimately decrease the frequency of fumigations. Despite the potential regulatory hurdle of entering a confined space, practically speaking, it should be conducted at least bimonthly.
But Arthur and Casada stressed that their research results do not serve as an end-all solution to controlling pests and maintaining grain quality. It’s merely one piece of the puzzle.
“Cleaning may not eliminate all danger of insect infestation,” Casada stated. “Typically some insects will come in with the grain — it’s not all going to come in clean. So, the point we’re emphasizing is that boot pit cleaning is just one aspect. You still have to manage the grain, but if you reduce the movement of insects from the boot, that’s a great start.”