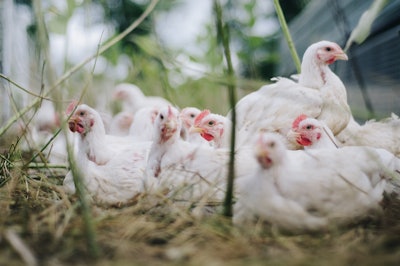
Mycotoxins are toxic compounds produced by certain molds that may be colonizing in grains in the field, when grains are stored improperly, when complete feeds are manufactured with too much moisture, or when complete feeds are exposed to too much moisture during storage.
Mycotoxins seldom occur in isolation. One mold is capable of producing several mycotoxins, therefore, several molds can contaminate one feed ingredient and several ingredients make up a poultry ration.
All poultry species are affected by mycotoxins, but various poultry species respond differently to mycotoxin challenges.
“For example, broilers and turkeys are relatively resistant to the mycotoxins fumonisin B1 and deoxynivalenol (DON) where other livestock are much more susceptible,” says Dr. Dennis Nuzback, DVM, PhD, with Phibro. “However, there are other mycotoxins that are much more toxic to poultry such as aflatoxins, T-2 Toxin and ochratoxin A.”
There have been more than 200 compounds identified as mycotoxins. The industry has a good understanding of the six major mycotoxins: aflatoxins, fumonisins, deoxynivalenol and its secondary metabolites, zearalenone, T-2 Toxin and ochratoxin A.
“There are also ‘emerging mycotoxins’ that have been more recently discovered and analytical techniques have been developed for their detection, but more work is needed to characterize their specific toxicities in poultry,” explains Dr. Nuzback.
Monitoring your mill
Should every feed mill test every load of grain for mycotoxins before they enter the storage bins? Of course not. And most mills are not set up to put this type of program in place.
So, what is a feasible, effective plan for managing toxins entering your mill?
Know the potential threat. “Being aware of the mycotoxin risk level from where the feedstuffs originated can help feed producers to be prepared for a potential risk,” says Dr. Alexandra Weaver, global technical support with the Alltech Mycotoxin Management team.
Mycotoxin issues are generally regional problems. “For example, ochratoxin A is more prevalent in grains produced in the Southern U.S.,” says Dr. Nuzback. “If grains are sourced knowing the originating geographies, that may prove helpful. With the availability of trucking services, however, the buyer still needs to beware.”
Buy grains from reputable suppliers. “Often times, contaminated grain sources are brought into the mill because the price was too good to be true,” says Dr. Nuzback.
Set up a testing program. “Testing programs for mycotoxins are one of the most important methods for monitoring mycotoxin risk,” explains Dr. Weaver. “Setting up a program that allows for routine analysis of feedstuffs/feeds for multiple mycotoxins is critical for understanding the risk at the mill.”
Components of the monitoring program should include:
■ Quality sampling techniques in order to get the most representative sample for analysis.
■ Routine sampling. Taking samples over time can provide more information on the mill’s baseline or varying mycotoxin risk rather than collecting one sample here or there.
This may include “quick screen” testing such as moisture testing, black light scans of samples from received loads of grain and on-site test strips that can detect problem loads in three minutes.
Periodic samples could be sent to local commercial labs for mycotoxin analyses and results logged by suppliers to help identify reputable suppliers.
“Once the word gets out that a mill is scrutinizing incoming loads, suppliers will be less likely to dump poor quality grains your direction,” says Dr. Nuzback.
Manage moisture. Good storage practices and cleaning programs are important for minimizing mycotoxin risk.
The best way to minimize the potential for mold growth in a feed mill is to add “moisture concentration” as a part of a quality control program for incoming grains.
“Ideally, mold growth is minimized when incoming grains contain less than 13% moisture,” says Dr. Nuzback.
“But practically, many mills use less than 15% moisture as a cutoff,” he continues. “Attention should be paid to final feed moisture and storage conditions of the finished feed in order to minimize mold growth from that point on.”
Testing is key
When molds are visually identified in a grain source, that’s a good indication there was a problem with grain storage somewhere. Only one third of mold species, however, will actually produce mycotoxins, says Dr. Nuzback.
Some of the grains with the highest mycotoxin concentrations can’t be visibly distinguished from the cleanest of grain sources. Knowing this, it becomes obvious how valuable mycotoxin testing is when establishing a grain purchasing quality control program. ■
Lower moisture is key to reducing potential mold growth
■ Properly drying grains at harvest is critical. If drying is delayed or if drying is not fully completed (if at >15% moisture), mold growth may occur which could lead to mycotoxin production.
■ Provide quality storage systems. Mycotoxin risk in storage silos/bags may be increased if these systems are not of proper quality. If there are any holes or damage then moisture, oxygen, rodents, insects or other contaminants may enter into the stored feedstuff. Molds that are already present in the feedstuff may begin to grow and produce mycotoxins, or new molds may be brought into the system.
■ Use fans to help reduce condensation (after a feedstuff has gone into storage at a proper moisture) and maintain average temperatures.
■ Keep mill components clean. If a routine cleaning program is not followed, there may be a buildup of crusts which can house molds, moisture, insects, etc. This may exasperate the problem.
For more information, check out "Go with the Grain: Managing mycotoxins for a healthier feed mill."
Information provided by Alltech