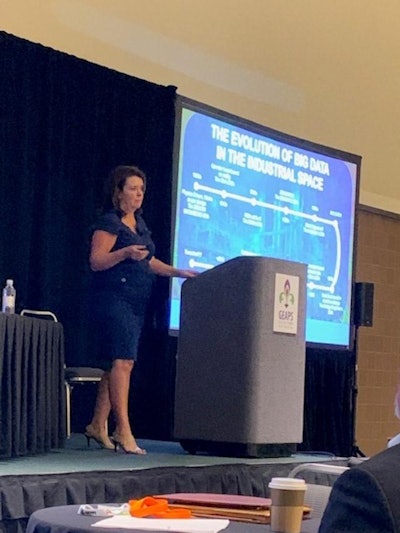
Big data has continuously evolved and grown since the 1800s, and the same challenges continue to exist today: how do I deploy new technology?
During the early 2000s, the Industrial Internet of Things (IIoT) exploded. With wired and wireless sensor technologies, collecting real-time data from equipment and stored grain is possible.
During a Monday morning session at GEAPS Exchange 2019 in New Orleans, Rachel Tormbetta, software engineering director with General Electric Digital, said every business is trying to solve productivity problems and agriculture is no different.
No matter where you’re at in the agriculture supply chain, there’s data that can help you make business decisions. Tormbetta says starting this journey is not easy, but it does need to be started.
“You’ve got to think differently and as a team,” she says. “Today we have to work differently. Some are scared to go on this journey, but those younger people coming up in your industry are expecting to use data to make decisions.”
Digital transformation must deliver outcomes. “If IIoT is going to deliver the value promised, there must be a focus on outcome realization,” she says.
What are the outcomes you seek? “What are you spending the most money on?” asks Tormbetta. “If one of your belts goes down, it might seem like four hours of lost productivity to you, but drivers are waiting and their farmers are waiting – and that all costs money. But using data collection, you could prevent that problem to begin with.”
Everyone wants increased throughput and decreased downtime.
“Imagine if you can see the weather coming in or the temperature in your silos,” she says. “You can now use data and technology to help you predict what’s going to happen more accurately and help you make better business decisions.”
The first step of the journey is getting the assets connected. “Most grain businesses have their assets connected, but now you have to understand what to do with that data – how to store it, how to move it, how to analyze it.”
Once the data is connected you can run reports. You can also get text alerts before a crisis occurs. Instead of reacting – data can help you be proactive.
“Imaging being able to control your environment through analytics by proactively controlling machines such as environmental control system,” she says. “For example, turn on fans when temperature is too hot. In this scenario, fans only run when needed, which means low cost energy consumption. This is predictive versus protective maintenance.
Where to start
First develop a plan. The first step is to implement an automation team consisting of a facility manager, on-staff engineer, information technology (IT) and a trusted worker. “Bring them in early in the process and they’ll be your best friends.”
Identify systems that not up to standards or not working. Prioritize their value and your operation process. If there’s a system failure, engage the automation team before calling a service company and look for automation opportunities to solve root causes versus symptoms.
Do your homework – there are so many solutions out there. Make sure they fully understand your industry and your business. “You need trusted partners to help the data be meaningful to your operation," she says. "Be sure to check their references."
Finally, develop your plan and have ways to measure it along the way. “You need to measure outcomes in order to insure success,” says Tormbetta. “Measure as you proceed through the process and you can make corrections and adjustments along the journey.”