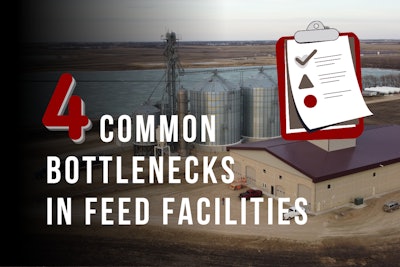
While many of us may dream of building a new facility with all the latest technology and new equipment, that might not be in the five-year plan for many of us. The next step is to take a critical look at what we have at our facility and identify the bottlenecks that would make an impact on overall throughput.
Each facility is different in terms of the challenges they experience, but from our experience, these are the four most common bottlenecks for feed mills:
- Ingredient Weigh Up Time
- Equipment Optimization
- Rolling and Grinding System
- Loadout Process
Ingredient Weigh Up Time
Arguably one of the most common bottlenecks in facilities, ingredient weigh up time compounds not only each batch, but day after day in facilities. Even if our lag time is 30 seconds per batch, that can amount to 2 hours per day, and 730 hours per year of lost time due to lack of efficiency.
A few solutions we recommend looking into include investing in an additional scale(s), both minor and/or micro, evaluating auger size by ingredient type to ensure maximum speed without compromising accuracy for large inclusion type feeds, and looking at average weigh up time by ingredient to determine which ingredients are taking the longest and start there.
Rolling and Grinding
How many times has your mill been at a standstill waiting for your rolling or grinding system to catch up or fill an ingredient bin?
If you haven’t automated your rolling or grinding equipment, we strongly recommend it.
Utilizing “Bin Keep Full” automation logic helps eliminate the chance of running out of ingredients that require rolling and grinding. Finding the sweet spot between running equipment at max capacity and a plug or breakdown can also be a challenge.
Allowing automation to keep a consistent speed to reduce breakdowns and overloading of machines for less breakdowns in the future.
Equipment Optimization
How hard are your pieces of equipment working for you?
Are you running all your augers at the same rate or are they customized based on ingredient type and inclusion rate?
We recommend setting up your variable frequency drives (VFDs) to change based on ingredient type to ensure that you are taking advantage of moving lighter products faster and leaving heavier products on a lower rate. In addition to fine-tuning VFDs, one other area we often see time lost is in the clean out process.
How long does your cleanout process take? We want to make sure the downstream equipment after the batching system is set so proper cleanout can be accomplished, but also not in excess.
If it only takes your system 60 seconds to clean out, we don’t need to have it set at 90 seconds. You’d be surprised how much time can be made up in this process.
Loadout Process
The ultimate loadout mistake we all want to avoid is putting two different formulas in the same bin. Mixing feed in a loadout bin results in time wasted and tough conversations.
Simply having visibility of loadout bins via a screen in the office eliminates confusion about which loadout bins are available and what orders or formulas are in each bin.
Once you can confirm what orders or formulas are in each bin you can capitalize on open space and route the same formula into that bin and maximize bin space.
Fine tuning the loadout process for a facility can truly save time and headaches. Whether that looks like manual lorry or remote tablet loadout, automation can help alleviate some of these headaches.
Interested in exploring these solutions? Visit easy-automation.com or call 507-728-8214 and ask for our sales team. We value your partnership and look forward to solving your equipment and automation challenges with you.