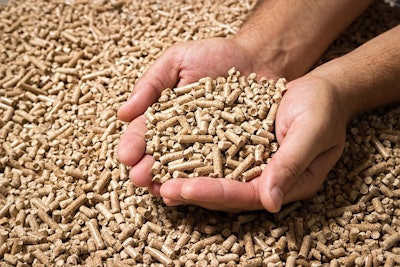
Post-pelleting liquid application can make it easier to add many essential ingredients to animal feed, including essential enzymes, vitamins and minerals.
Accurate, uniform coating, however, can be a challenge. Pellet breakage and product loss can also be a challenge in post-pelleting liquid application. A few considerations can help to improve this process, especially if you are newly installing a post-pelling liquid application system.
What is Post-Pelleting Liquid Application?
Post-pelleting liquid application describes different methods to coat animal feed or foods for human consumption after the ingredients have gone through pelleting. During the pelleting process, compressed materials move through a die to form a cylinder, or a pellet. The pelleting process uses heat and steam to help compress the materials and also kill bacteria.
High temperatures can destroy some enzymes, vitamins, minerals, or flavors, so post-pelleting liquid application allows these additives to coat the pellet after the heating process. These ingredients are usually added in very small amounts, as little as 40 to 250 grams per ton of feed, so a high level of accuracy is very important. With such small amounts, uniform coating is also essential. Too much coating on one pellet means too little coating on another, and either can be ineffective.
4 Steps for Effective Post-Pelleting Liquid Application
Step 1: Process Assessment
To make your post-pelleting liquid application accurate and reliable, it’s important to assess the pelleting process and liquid ingredients first. For example, if you are working with heat-sensitive ingredients, liquid application must occur after the pellets have cooled. Assessing the operation can also show where you can most easily and accurately measure the flow of feed pellets. To accurately dispense liquid ingredients, you’ll need to accurately measure the pellets being coated.
Gather documents on your pelleting process, or make a written list outlining the process. Blueprints with measurements can help your post-pelleting liquid application equipment supplier design the optimal equipment and also place it most effectively in the plant. A written list of liquid ingredient characteristics, including its susceptibility to heat, viscosity, and fat or oil content, among others, will also be important. Your liquid ingredient supplier should be able to provide this list.
Step 2: Accurate Dry Ingredients Measurement
As previously mentioned, it’s important to accurately measure the pellets in order to accurately measure the liquid coating. There are several ways to achieve this and which is best will depend on your facility and process. Your process assessment in the previous step will be important here.
Volumetric measuring is one relatively low-cost, low-maintenance solution to accurate measurement. Using a surge hopper or a buffer hopper with low and high level switches will help to accurately measure ingredients and make calibration easy. A weigh belt might also present an effective solution.
With this method, a surge bin dispenses ingredients onto a belt or mixing screw, and a load cell measures the ingredients. However, these systems can be difficult to calibrate and require a large space. Impact scales are another method, using force to measure flow. These devices are much smaller, but are only effective for continuous flow applications. Bulk density must also remain constant.
An experienced equipment manufacturer will be able to explain these solutions in more detail, and help you find the optimal solution for your needs.
Step 3: Accurate Liquid Ingredients Measurement
As you might expect, there are also multiple ways to accurately measure and dispense liquid ingredients. This system will vary depending on the type of liquid ingredients you’re working with, the layout of your facility, your application method, and more.
Volumetric measurement is, again, a popular solution. These systems typically use a positive displacement pump to dispense liquid ingredients based on time or pulses. With these systems, it’s especially important that the dry flow measurement system is accurate. Loss-in-weight measurement also uses a positive displacement pump to dispense liquids accurately, and this will also show when the liquid levels are low. Flow meters are the most common method for measuring liquid ingredients, though the accuracy and level of maintenance and calibration required will vary depending on the quality of the construction.
Step 4: Uniform Coating
Accurate measurement won’t be very useful if the pellets aren’t coating in an uniform manner. Or, if the coating equipment frequently clogs or requires excessive maintenance, the time- and cost-saving optimizations across the rest of the system may be lost. Here again, the more information you have on your facility layout and ingredient characteristics, the better your equipment design will be.
There are many ways to apply liquid coatings. Some of the most common methods include a mixing screw, spray chamber, rotary atomizer, or paddle mixer. With each of these methods, the footprint and facility arrangement, as well as the liquid coating characteristics, will all be important.
Certain liquid coating processes will promote retention and uniformity for some ingredients, but not others. A rotary atomizer system is ideal for liquid mixtures that tend to clog spray nozzles, since the system does not require spray nozzles.
With all liquid coating systems, it’s advisable to remove fines prior to coating, as these small pieces will disproportionately absorb the coating.
Though we’ve simplified this process somewhat to provide an overview, each of these steps is important to design the right post-pelleting liquid application system. Different facilities, ingredients, and different types of pellets may require special considerations. Talk to an engineer to learn more about liquid coating systems and discuss specifications for your project.