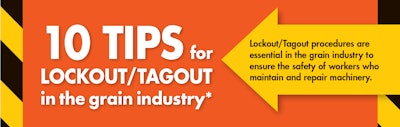
Infographic by Tess Stukenberg
Download the full Infographic here.
Log in to view the full article
Subscribe to Magazine
Lockout/Tagout procedures are essential in the grain industry to ensure the safety of workers who maintain and repair machinery.
Subscribe to MagazineDownload the full Infographic here.