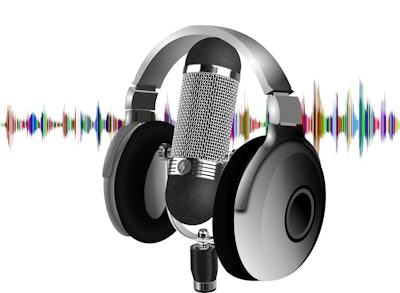
In this episode of the Feed & Grain Podcast, Steven Kilger, managing editor for Feed & Grain, interviews Greg Franzen and Mark Herbert from Faithful+Gould, a global consulting firm that serves as an independent third-party client advocate for agribusiness construction projects. Franzen is the agrifood sector lead, while Herbert is the project controls manager.
They discuss what feed manufacturers and grain handlers should focus on when starting a construction project, the importance of seeking outside help, and what to prepare for and keep track of during a construction project. They also talk about the challenges of dealing with changes during construction projects.
Transcript
Steven Kilger:
Hello everyone!
Welcome to the Feed & Grain Podcast, and thank you for listening. My name is Steven Kilger, managing editor for Feed & Grain and your host.
We have a fantastic show for you today. Greg Franzen, agrifood sector lead at Faithful+Gould, and Mark Herbert, project controls manager Faithful+Gould, stopped by to talk about what grain handlers and feed manufacturers should focus on when they start a construction project. It's a big topic, but there’s lots of great information on when you should seek outside help, what to prepare for and keep track of during a construction project, and lots more. It’s always fun to talk and I hope you enjoy it as much as I did.
But before we get to that, I’ve got to do a bit of housekeeping.
If you're listening to this podcast within a podcast app, please consider subscribing. If you have an idea for a topic you would like me to cover, or someone in the animal feed, grain handling or related industries … let me know.
This podcast’s page on feedandgrain.com has a button right under the title that will let you send an email directly. I’d love to hear from you.
All right on to my talk with Greg and Mark.
Kilger:
Hi, Greg, Mark! Thanks so much for coming and talking to me today.
Greg Franzen:
Hello, Steven.
Kilger:
Well, like I said earlier, when we were talking off mike, I first saw you guys at this last year's GEAPS Exchange, he gave a really great talk about kind of all the particulars that go into making a construction plan for a new, build new greenfield construction, and how to kind of get all that put together. So everyone, at the end of the process, everyone is hopefully as happy as they can be. It's as close as everything is as close as it as possible with these constructions. I covered a lot of construction processes, and they never exactly go down on paper, do they?
Franzen:
No, there always seems to be some form of change, so that's it's pretty common. Most of the success of a project is how your your team is able to deal with change.
Kilger:
Before we get too far to that, though, can you guys just tell me what you do? You work for a company called Faithful+Gould, which is a construction consulting company, correct?
Franzen:
Yeah, we are. Faithful+Gould is a global consulting firm, and 99.9% of the time, we sit on the side of the client in construction project. We serve as that independent third party client advocate. Our mission is really to help the client maximize their interest in their capital project, so that's what we do.
Kilger:
Excellent. And what do you guys specifically do for the company?
Franzen:
Well, Mark, I'll let you introduce yourself and your role.
Mark Herbert:
Yeah, thanks. So my name is Mark Herbert. I am a planning and scheduling professional through the association for the advancement of cause engineering. I'm also a professional construction engineer in the state of Minnesota. I help clients build things in a nutshell, but the reality is that we plan and schedule and manage costs for the large infrastructure projects. In this particular case, I'm more focused on the sort of agriculture or industrial agriculture sector, for example a large fertilizer production facility or wastewater treatment plant for ethanol production ... many of those types of things are a grain transfer facility.
These are millions and millions and millions of dollars, and I try to step in and help the client manage the process, where are they know, what they want at the end, but how do you get to the end? How do you take the keys and unlock the door and walk into the facility. I walk with the client through that process on who they're hiring, when they're hiring, when they're building, when they're constructing, when they're designing, and all that fun stuff.
Franzen:
And my name is Greg Franzen. Mark and I both sit in the Minneapolis office and I oversee our agrifood project work in the U.S. Agrifood is anything that includes anything from the agribusiness projects -- like for clients that typically would attend or participate in GEAPS -- and also food manufacturing. That's sort of my role in the company. Our mission is to really be flexible and help the clients where they need help: fill in gaps for resources or provide a team of people to help or provide a cost estimate. That's what we do in the agrifood sector, as we call it.
Kilger:
Well, it's great because I've interviewed a lot of facility managers, regional managers, that kind of thing and feed in grain handling, and while a lot of them kind of get pushed to the forefront of these big construction projects, in reality, it's not their norm, it's not usually their normal job. It's usually such a big thing that doesn't happen all that often, so it's, it's really nice to hear that's what you're here for. You're here help them with something they probably will only do once or twice in their careers and also don't have a ton of experience with, right?
Franzen:
No, and that's a good point. Many times we work for clients, and they're, for instance, their operations director might be responsible for a very large project in addition to their day job. It puts a tremendous load on people. Our objective is to support people, and through implementing good construction processes, to help them be successful and delivering their project. You're leading into one of the first items we wanted to talk about, which was a project charter. What is the project charter? Does it make sense to continue?
Kilger:
Yeah, definitely. That was my first question. Because during your presentation at GEAPS, you guys mentioned project charter, and kind of those initial steps of initiating it. So for all our listeners that might not know or might not have an experience with that, can you kind of explain what a project charter is and what it does, and why it's an important part of the overall construction process?
Franzen:
Sure, the project charter is really the initial initial step in the formation of a project. Really, it sets the standard for assessing the baseline for what the need is, what's the business case? Then how do we achieve that need in business case through a project. Company leadership should really appoint an internal sponsor that has the authority and responsibility to initiate the development of that project project charter.
The purpose of the charter is to provide company authorization for the expenditure of resources on the project. It should include the name and description of the project, name of the sponsor and project manager, who would be responsible for the project. It should include some of the other project team. Team members provide a brief description of the business case. Define the general scope of work of the project and also the expected goals, objectives and deliverables of the project. You will also want to include some project milestones like start date, completion date. Then identify project risks or constraints that may exist. That's really a pretty quick overview of a project charter. It doesn't have to be complicated but does need to be somewhat comprehensive.
Kilger:
Yeah, it's really important, especially with the way ag organizations are often constructed. To me, because a lot of them are co-ops, which have boards and all these things that make the final approval, but this seems like it lets both sides, the contractor and the company, get things done, to know who's in charge on day-to-day stuff. Right, with without that board approval. Am I getting that right?
Franzen:
It's really meant to be an internal document for the business to come together and agree on. Typically, boards of directors are approving large projects. This charter would be something that a board level would review and approve and agree to or comment on. It's that initial document to say, okay, this seems like a good idea. We'll provide funding up to a certain value until you take it to this next stage. That's how the charter gets you started.
Kilger:
Very interesting. During your GEAPS presentation, another thing I found really interesting, especially for the companies that have a lot of facilities and may have done this more than once, can you talk a little bit about the importance of documenting and implementing the lessons learned from the previous projects? I found that really fascinating part of your original presentation?
Franzen:
Sure, I think Mark and I are going to take team on this one, but take the first stab at that. So from lessons learned, we all understand what lessons learned are. From the time you were a little kid, it's like put your hand on the hot stove once and hopefully, that's a reminder not to do that, again, because it hurt.
All of us have that built into us. Our experiences are one of the best teachers. Lead capturing lessons learned is simply a method of an organized method to capture those lessons that we've learned through the course of the project and to document them then store them in a way that they can be easily resolved, easily pulled up by many others.
Document management is really important. To have good document management and communicating to others in the business where you know, these lessons learned are, and then also applying the lessons learned to the appropriate time in project development, and so accessibility. We have to get the information or the experience out of our head onto paper. We're more appropriately documented electronically, so that we can share that experience with others and others can benefit from the experience we all have. It's getting the information out of our head so we have it digitally. Then storing the information in a centralized location, like in a SharePoint, and making it available to others that have projects for coordinating. You know, the naming convention is that type of lessons learned is -- does it have to do with electrical systems, mechanical systems, civil, whatever.
So organizing in a proper way, and then implementing it. At the beginning of a project would be a good time to review lessons learned from previous projects. Also during the design engineering might be a good time, value engineering workshops, procurement, and strict construction kickoff, and project close out. All those steps sort of need to work together to apply lessons learned. And then Mark, you had another thought here on mediation arbitration.
Herbert:
Just to add to what you were saying, talking about importance, why is it important? Unfortunately, claims happen a lot, not a lot in these projects, but claims often happen for one reason or another. You wind up going through mediation, arbitration, God forbid litigation. Having this documentation for current project is also good because of legal proceedings. Things often happen years after the project's already done sometimes, so the details are lost in the time. Capturing those are very important just for that. Then taking a step further and talking about from one project to the next. Understanding how long similar scopes took, durations, how many people it took, whatever you want to measure, to complete the project. When these arguments start to rear their ugly head, you might have a better footing on, hey, the plan is right and the execution is wrong.
Because when you don't have that, that documentation and lessons learned coming in from older projects, it really becomes an argument of, hey, maybe the plan was flawed and our execution was good. There's a bit of an argument there. Having the document, lessons learned, supports the idea of the owner saying, "nope, we had a good plan, it was your execution that did not fulfill plan." That speaks to the importance of documentation and implementing lessons learned.
Another one, Greg was mentioning it earlier, about the passing the knowledge down, when throughout human history, a lot of it's been verbal and oral traditions being passed down through people. And it's kind of the same way here, where you're looking for the most experienced people when you're starting these projects. I'm not saying that's bad. In fact, it's very good to do.
But in a long CIDA (Council for Interior Design Accreditation), we should be looking for the most experienced documentation of other projects and coupling those two. I'm not saying that knowledge is a substitute for human experience, because it's not. But it will shore up the idea of having the experienced people with the historical knowledge outside of their own, that makes for a complete picture for project planning on any project and just make things sail. It's like night and day when you're going through the process. Once you have that foundation, the idea that people come and go, turnover can get high. I know everybody says well, it's just you know, people are changing jobs all the time these days. I've been around long enough to know that kind of the way it's always been. That's just life. So, having the documentation allows you, whether you get those experienced people or not, to still let you transfer that knowledge.
Kilger:
It's a good reminder for anyone starting a project, because it's such an easy thing to forget, right? Anyone who's been involved with something that like this, a big project where you have so much going on, it's so easy to forget, or tell yourself, you're going to do it later and then completely forget to document anything. But it comes up all the time. I mean, my experiences with magazine issues, right? Where we have a really good documentation system and thank goodness, we did because you never know what's going to come up. So, just today someone was asking me for an article from 2017 that I had to go in and find. Really, we wouldn't be able to respond. So it's something we don't think about it especially when you're starting a big project but such an important little part of it. I think people need to be reminded of that.
Hey, everyone, this is Steven again. I'm just here to tell you my conversation with Greg and Mark went really long, so we're splitting it up into two podcasts. But the good news is, I'm actually going to start producing three Feed and Grain podcasts a month. We'll be dropping a podcast on the 7th, 15th and 30th of every month. We hope you enjoy the extra podcasts. Thank you for listening. Stay safe out there. We'll be back very soon. Bye!