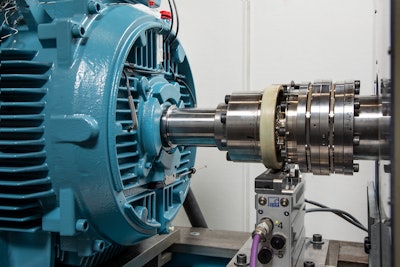
Brith Isaksson, Global Segment Manager, Food and Beverage, ABB, explains how the feed and grain industry can now ensure safety and boost energy efficiency by deploying motors that offer up to 40 percent lower energy losses compared to commonly used IE3 motors.
Brand Insights from ABB
Motors power critical applications in the milling industry, from conveyors and blowers to mills and mixers, keeping processes running smoothly, reliably, efficiently, and safely. That is why drive and motor systems consume most of the electricity in the sector, making them a logical starting point for energy savings.
Fortunately, solutions like the new generation of ultra-premium efficiency motors provide a timely and highly effective solution for optimizing processes such as milling, mixing, and packing.
Safety is paramount in the feed and grain industry, particularly in milling machines at flour mills where the explosive nature of grain dust can pose significant risks. The arrival of the world’s first IE5 Synchronous Reluctance (SynRM) Increased Safety motors now allows feed and grain manufacturers to adopt the most energy-efficient motor and drive technology while ensuring utmost safety.
Advanced efficiency
In Europe, China, and many other countries, the efficiency of electric motors is described by the International Efficiency (IE) class. Each IE class represents a higher level of efficiency, with IE1 being the least efficient and IE4 being the most efficient. IE4 has become the minimum standard for certain types of motors for new installations and upgrades in Europe since July 2023, and other regions are likely to follow.
However, these regulations exclude older motors already in use (some with even lower efficiency than IE1), causing many feed and grain production facilities to waste energy with inefficient motors. Upgrading such motors can yield immediate results.
For businesses looking to maximize energy efficiency, the latest generation of ultra-premium SynRM motor and drive packages achieve IE5 efficiency, the highest efficiency in the market. Replacing IE3 motors with IE5 SynRM models, which are designed to operate with VSDs, can reduce energy losses by up to 40%. This results in lower total energy consumption and CO2 emissions, making it part of a package that automatically provides energy efficiency beyond any regulation.
These SynRM Increased Safety motors provide all the class benefits such as ultra-premium efficiency and lower CO2 emissions, as well as reduced maintenance, and enhanced reliability due to lower running temperatures, longer lifespan, and fast return on investment (ROI).
Upgrading unlocks vast energy savings
To demonstrate the potential for significant energy savings, a leading multinational producer of sugar, starch, and fruit products partnered with ABB to boost the energy efficiency of its Belgian plant. The facility processes 21,000 tons of sugar beet daily during the four-month season. During this peak period, the production machines run 24 hours a day, using a great deal of energy over a relatively short time.
The first step was to find out where the most energy was being consumed. The sugar producer found that transporting thousands of tons of beet every day was the most energy-intensive part of the process, followed by slicing and pressing machines. They determined that the slicing machines had the best potential for savings. The sugar producer replaced six old low-voltage electric motors with IE5 SynRM ultra-premium motors and drives, providing significant energy-saving opportunities.
This motor-exchange project has resulted in a 27% reduction in overall costs for the sugar producer and a reduction of just under 120 tons of CO2 emissions.
Certified for safety
Utilizing motor-drive packages with ATEX certification is crucial for applications in explosive atmospheres, a common condition in feed and grain milling. However, a suitable SynRM motor was previously unavailable. With the introduction of SynRM Increased Safety motors, feed and grain producers now have access to the most energy-efficient motor and drive technology available. ABB leads the industry with ATEX and IECEx-certified SynRM motors suitable for explosive atmospheres.
Cost-efficient replacement
The motors can also contribute to a more cost-effective installation. For instance, in Zone 1 – a hazardous area where explosive gas and air mixtures are likely to occur in normal operation – the cooler operating design of SynRM motors could enable an increased safety motor to replace the conventional flameproof motor, utilizing a special enclosure. In Zone 2 – a hazardous area where explosive atmospheres are unlikely during normal operation but are possible in accidents or abnormal conditions – the motors’ improved load capacity, which allows for more power delivery within the same size as an induction motor, is significant. This could enable the use of a smaller and more affordable motor for the same purpose.
SynRM motors are also a great entry point for businesses looking to modernize their assets, offering a seamless upgrade solution. Since they share the same size as induction motors, the replacement process is easy and causes minimal disruption to operations. The motors are also compatible with ABB Ability™ Digital Powertrain, allowing remote monitoring of electrical motor-driven systems.
Long-term savings
Lowering energy consumption decreases initial costs and reduces the total cost of ownership (TCO) over a motor’s lifetime. Although less efficient motors might come with lower initial costs, TCO analysis reveals that approximately 97 percent of a SynRM motor’s TCO results from electricity usage over its operational life.
Maintenance accounts for only one percent, while the motor’s initial cost makes up the remaining two percent. Plus, once the motor has paid for itself, it continues to produce savings throughout its operational life.
Opportunities are here and now
Rising demand requires swift energy efficiency measures in the energy-intensive feed and grain milling sector. The necessary technology is readily available, offering a superb opportunity to address the climate emergency and enable significant financial savings. The key is to use it and to use it now.
Learn more about the energy efficiency possibilities of ABB’s IE5 SynRM Increased Safety SynRM Motors here.