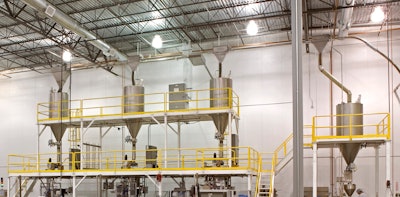
Nutritional supplement companies for animal livestock, such as beef and dairy cattle, swine and poultry, produce and convey precise formulations. Farmers, ranchers, and producers rely on these feed supplements to enhance animal health and productivity.
This requires correct formulation of various trace vitamins, minerals, and micro-ingredients in accurate proportions in accord with regulatory guidelines, including FDA's Center for Veterinary Medicine (CVM) which is responsible for the regulation of animal feed products. Typically, these premixes or compounds are produced in a relatively fine or semi-powdered form that allows farmers to easily mix them with their own grain or fodder to formulate their own rations.
However, conveying and mixing these feed supplement formulations, which vary by species, age, and other factors can be challenging and inefficient with traditional air conveyors. High-speed conveyance, particularly through bends, can cause product separation and potentially degrade product integrity.
Fortunately, industry innovation has made available a gentler alternative that contains precise formulations and pre-mixed blends during product and ingredient transfer: tubular cable conveyors, which cost-effectively safeguard product integrity.
Such cable and tube transfer systems can safely move all kinds of powders including pre-blended mixes with ingredients of varying bulk densities. This is accomplished with cable and tube technology that contains the mixed ingredients in between discs, which keeps all contents secure during movement.
The approach also offers more options for dry and wet tube conveyor cleaning than traditional pneumatic equipment, which can enhance production by minimizing downtime necessary for cleaning.
Additionally, compared to high-speed pneumatic systems, cable and tube transfer systems use smaller, more energy-efficient motors, which provide significant energy savings and a quieter work setting.
Limitations of Air Conveyors
High-dollar value nutritional feed supplements can be prone to product separation
and degradation when conveyed at high velocity by air-power, such as in pneumatic and aeromechanical systems.
Pneumatic conveyor systems utilize air by creating air pressure above or below the atmospheric level. These systems use filters that require regular replacement. The two main types of pneumatic conveyors – dilute phase and dense phase – differ by speed and pressure, and both can be configured as a pressure or vacuum system.
In dilute phase conveying, feed supplement product and ingredients would be suspended in the air and transported through the conveying pipe at extremely high velocities of typically 3,400-5,000 feet/minute.
Product separation is a particular risk at bends and sweeps where it can be forced through constricted areas and quickly change direction. In such cases, various ingredients and micro-ingredients with different bulk densities can segregate. Valuable product and ingredients can also be damaged, if fragile.
Dense phase pneumatic conveyor systems, where the nutritional supplement feed product and ingredients are not suspended in air if heavy or abrasive, function at lower velocity than dilute phase. However, with air speeds of about 700-1,500ft/min. materials can still separate.
While aeromechanical conveyors have a different method of conveyance, these enclosed, high-capacity mechanical systems can also degrade some product and ingredients. With these systems, a wire rope with evenly spaced discs within a tube travels at high speed, running in sprockets at each end of the conveyor. This generates an internal air stream traveling at the same high velocity as the discs that carry product along in the tube.
However, these conveyors may also force vulnerable materials through stressful phases during transport, which could impair their integrity.
Protecting Product & Profitability
A gentler alternative to protect sensitive, high-value animal feed nutritional supplement products is to utilize tubular cable conveyors.
“Tubular cable conveyors move product through a sealed tube using a coated, flexible stainless-steel drag cable pulled through on a loop. Solid circular discs (flights) are attached to the cable, which push the product at low speed through the tube without the use of air, preserving product integrity,” says Karl Seidel, Marketing Director of Cablevey Conveyors. The Oskaloosa, Iowa-based company is premium, specialty material moving, mechanical conveyor manufacturer that has designed, engineered, and serviced enclosed cable and disc tube conveyors for almost 50 years, and is in more than 66 countries.
In the food industry, the conveyors are utilized for products such as powdered supplements and foodstuffs, pet food, nuts, cereal, coffee, snacks, beans, and seeds. The systems can convey up to 2000 cubic feet per hour (56m3/hr.) of powders, granules, shavings, crumbles, regrind, flakes, pellets, chunks, parts, and prills with numerous layouts using multiple inlets and outlets.
Since the material is carried between the flights, nutritional supplement product for livestock in premixed or blended form, as well as inputs, are safely conveyed. The evenly-spaced discs fully contain powders and mixed ingredients of varying bulk densities with virtually no product separation or degradation during movement.
Because margins in the livestock industry can be thin, nutritional supplements must be reliably and cost-effectively conveyed at high volume, while maintaining cleanliness.
In this regard, the cable and tube powder transfer systems provide clean handling via the evenly-spaced discs pulled by cable. This minimizes any potential contamination of product and inputs as well as the processing plant. When cleaning is factored in, closed-system tubular cable conveyor systems are also less expensive to own and operate than pneumatic equipment.
In regard to maintaining cleanliness, tubular drag cable conveyor systems offer more options for dry and wet tube conveyor cleaning than pneumatic equipment. These include brush boxes, urethane wipers, air knives, inline sponges, inline bristle brushes, and multi-step, essentially automated Clean-In-Place (CIP) wet cleaning.
Since pneumatic systems convey product at high velocity, this typically requires larger, power-hungry motors that run fans, blowers and rotary valves. In a dense phase system, a pressure tank requiring compressed air consumes additional power.
In terms of noise level, pneumatic conveying systems also generate considerable noise. Aero-mechanical systems, running at high speed, generate considerable motor and disc noise as well.
Given that smaller motors are used, tubular cable systems utilize much less energy and are quieter overall. A low speed tubular cable system is quiet enough to easily have a conversation around it while it is running. In regards to energy, it utilizes about one-tenth that of pneumatic systems. For dense phase models, the electricity savings by using a tubular conveyor can be sizable, with 1-year ROI in some cases.
As livestock nutritional supplement companies seek to protect product integrity and margins, tubular cable systems can be a tool for enhancing profitability for many years to come.
For more information, click here.