= Event At-A-Glance =
How efficiency, innovation and sustainability will shape the feed industry of tomorrow
Co-located with IPPE 2023 | Atlanta, GA, USA
January 24, 2023 | 8 a.m. –Noon | Room B203
Fee: $95 early bird | $125 after Jan. 6, 2023
View the full agenda here: www.feedmillofthefuture.com
How to register: To attend the Feed Mill of the Future Conference, attendees must first register to attend IPPE. Register today for the lowest ticket price, go to www.ippexpo.org, and visit the “Education Programs” for details.
Feed mill operations efficiency might impact the overall sustainability of animal protein production more than you think. Gero Zimmermann, head of Technology, Animal Nutrition for Bühler, said pelleting line optimization alone can reduce energy consumption by up to 20%, resulting in a significant decrease in carbon emissions.
In this Feed & Grain Chat, Zimmermann shares how feed millers can achieve operational excellence and contribute to animal agriculture sustainability with solutions like adaptable hammermill and grinding options, digital sensor integration and predictive modeling.
Transcription of Feed & Grain Chat with Gero Zimmerman, Head of Technology, Animal Nutrition for Bühler.
Elise Schafer, editor of Feed & Grain: Hi everyone, welcome to Feed & Grain Chat. I'm your host Elise Schafer, editor of Feed & Grain. This edition of Feed & Grain Chat is brought to you by WATT Global Media and Feedandgrain.com is your source for the latest news, product and equipment information for the grain handling and feed manufacturing industries.
Today, I'm joined on Zoom by Gero Zimmermann, head of Technology, Animal Nutrition for Bühler. He's here to discuss how improving the efficiency of grain processing equipment can help reduce carbon footprints at the feed mill. Hi, Gero. Welcome to Feed & Grain Chat!
Gero Zimmermann, Head of Technology, Animal Nutrition for Bühler: Hi, Elise. Thank you for having me.
Schafer: Yes, thank you for coming on! Well, let's get right into it. As the animal protein production supply chain works toward greater sustainability, can you address how feed mill operations efficiency plays a role in the overall equation?
Zimmermann: Well, especially considering the fact that feed production accounts for one-third the carbon footprint of the animal protein supply chain and that 96% of this one-third are related to raw materials, one could easily come to the wrong conclusion that not much can be done on the level of the feed mill itself. But this is certainly a wrong conclusion.
What the facts are telling us is that we not only have to come up with more efficient machines, energy recovery systems and everything which helps the feed miller to reduce Scope 1 and 2 emissions, but that maybe, above all, we have to think about how we can make better use of the raw materials. And we are certain that advanced process control systems and digital solutions digitalization actually enable us to achieve this goal both directly by increasing the operational excellence, but also indirectly by enabling the use of more sustainable and alternative raw materials, such as local crops, for instance, or a single-cell proteins.
Schafer: When we look at the entire feed manufacturing process, grinding is one of the most energy consuming steps. How can mill operators make the most of that grinding equipment and get more output with less energy.
Zimmermann: Yeah, naturally a highly efficient grinding process requires highly efficient grinding machine. This is one key element and what has to be avoided in any case is over grinding so that raw materials are ground to a finer granulation than actually needed for this in this specific case. So what is a must is to have, for instance, a hammer mill which is adaptable to the specific requirements of this application. Adaptability in this sense means it has to have a modular concept. It has to have options like re-grind chambers, impact plates, rotor sizes, so design elements, which allow to find the right machine configuration for this specific application, and if this configuration is found, the machine runs at the most efficient level and the grinding line also always is optimized in the sense.
And then of course, let's say what can be done on top of that is to maintain the machine at this operating point by installing sensors, for instance, measuring the intake air of the machine and adjusting the feeder so the product flows through the machine so that clogging of debris is avoided, which in turn means that the machine is more available. We have seen cases over the last years where we achieve higher machine adaptability in the range of 30%, so certainly more throughput on the same machine, higher efficiency.
And this is also quite an interesting approach with saying over the long run constantly and consistently achieve a higher efficiency on the grinding line. And of course also let's say on top of the digital sensors can help to monitor the status of the machine and the status of the wear parts, so that let's say the right moment and time can be found to do a service on the machine or to exchange or to replace the wear parts.
Schafer: Wonderful. Now, you spoke about sensors on the grinding and hammermill. Can you describe how the use of digital sensors throughout the feed mill process can help optimize facility operations and help reduce carbon footprints.
Zimmermann: Digital sensors in the first place can provide a higher transparency and insights into the process, and also, let's say product quality in a given moment and into ambient conditions. So, by just providing this kind of information to a skilled operator, this operator for sure can find a better setting, can improve efficiency, can reduce the carbon footprint.
But specifically, if the sensor setup is combined with a predictive model, digital twin you could also name it, and a machine learning algorithm, then the same system and hardware basically can provide recommendations also to a non-skilled operator or an operator with less experience. With this kind of decision support systems, having different skill levels in your in your staff, you can run the feed mill on average at a much higher [efficiency] level than without such a system.
And at its highest development stage, of course, is the system does all these optimizations independent of the operator, so fully automatic process control system. We have seen cases in pelleting lines where we install such systems where the process runs much more stable than before, throughputs of 20% higher than before, energy levels 10 to 20% less than before and with a very consistent end-product quality.
If you translate this, for instance, for such a pelleting line — let's say a typical pelleting line with a yearly throughput or production capacity of 100,000 tons — if you translate this into the carbon CO2 reduction, this is equal to something at the level of 3,000 tons less CO2 and these 3,000 tons of CO2 will turn into the drawdown capacity of roundabout 130,000 trees. And this is just for one line, so if your factory has a couple of such lines, this is quite an achievement and a way to make a significant impact on the sustainability topic.
Schafer: Gero, thank you so much for sharing your insights with us here today! And if you're interested in the topics we discussed here, consider joining us at the Feed Mill of the Future Conference held at IPPE in Atlanta on January 24.
Gero will be speaking there on a panel titled Feed’s Role in Animal Ag’s Path to Net Zero Carbon Emissions. For more information and to view the full program, visit feedmillofthefuture.com. That's all for today's Feed & Grain Chat. Thank you for joining and I hope to see you next time.
Sponsored by:
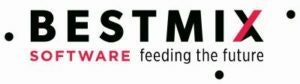

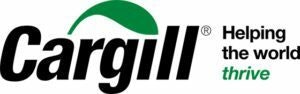