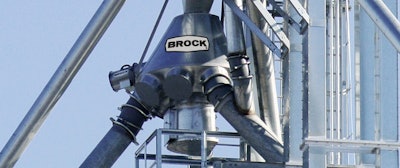
There are many considerations when designing a new grain handling system. Grain handling capacities, system expandability, maintenance requirements, equipment durability and service support all play important roles.
Sizing grain handling systems to meet capacity needs
One of the most important factors when choosing grain handling equipment is knowing your throughput requirements and balancing the needs for realistic capacity and future expansion.
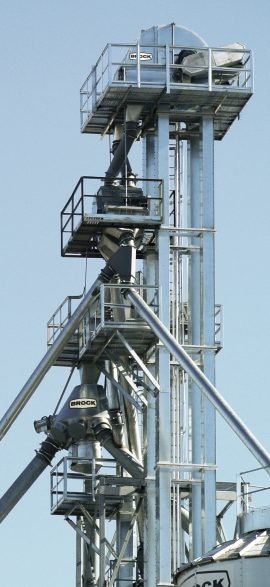
Beware of overstated capacities
Some manufacturers claim grain handling capacities at optimal conditions using grain at a 15 percent moisture level. Real-world applications must account for heavier, wetter grain that does not flow as readily.
Brock Grain Systems takes this variability into account when stating throughputs. If a Brock commercial bucket elevator or drag conveyor is rated to deliver 30,000 bushels (800 metric tons)* of grain per hour, you can be confident it can meet that capacity during everyday conditions, not just optimal ones.
* Capacities based on water level plus 10% for dry, free flowing, grains with a 48 lb/ft³ (768 kg/m³) material density.
Avoiding bottlenecks
A good grain system designer will make sure all components work together seamlessly to meet capacity throughputs. Brock Grain Systems and their dealers use advanced tools to design and appropriately size complete grain handling systems. Elevator buckets are spaced to maximize capacity with high moisture grain. Drag conveyor chains are appropriately sized for bushel requirements to provide long life. Roller-belt conveyors are computer matched to the motor drive and gear reducers. This attention to detail ensures that you are not overworking any part of your grain handling system and that there are no weak links that could limit overall capacity.
Checking the details
Not all grain handling equipment is created equally. Even small differences in equipment design can add up to significant savings over the life of the system. Look for features that increase productivity, reduce maintenance, and make the system last longer.
Bucket elevators
If elevator trunking starts to separate prematurely, buckets can catch on the exposed edges and damage the system. Brock trunking flanges are solid-welded on the inside and outside. This closes the gaps so no moisture, dirt or debris can get inside the trunking. This extra welding is an important feature to ensure long life. If grain falls back down the bucket elevator, it is like taking one step forward and two steps back. Brock bucket elevators are designed with a bonnet discharge throat and profile that keeps elevated materials discharged properly, minimizing material back-legging.
Distributors
Many distributors have flat areas that are prone to collecting grain dust and other material. These can be trouble spots that can rust out before your eyes. Brock uses a unique inverted cone design at the inlet that prevents material and moisture from building up on the distributor bottom, preventing premature failure. Brock distributors are easy to operate. Unlike some grain distributors that rely on manual spout switching, Brock uses a cable latching system. You don’t have to lift an inner spout to move to another outlet.
Drag conveyors
As drag conveyors age, their chains can loosen and have a tendency to ride up off the bottom of the conveyor. This reduces capacity and efficiency. Brock engineers developed 10° angled flights that keep their drag conveyor chain from riding up on the grain. The flights act like a bulldozer blade to keep the bottom clean and prevent possible material build up. Brock provides a full line of horizontal and incline drag conveyors in a range of sizes to provide ultimate flexibility when designing a grain or material handling system.
Enclosed roller-belt conveyors
Enclosed roller-belt conveyors have high capacities and are very gentle on grain. Brock’s roller-belt conveyors are enclosed to contain grain dust and to protect your product from the elements. A distinct peak on the top of the conveyor allows for snow and water runoff. Another unique feature of the Brock enclosed roller-belt conveyor is the design and construction of their idler pulleys. They use full-length shafts with positive locking tapered bushings for uniform weight balance and long equipment life.
Intermediate discharge units
With Brock’s conveyor intermediate discharge unit, one enclosed roller-belt conveyor system can have multiple discharge points to easily service many bins or silos. One important distinction about the Brock discharge car is that it never comes in contact with the belt. The Brock discharge section transfers grain from both sides of the belt to a single discharge under the conveyor.
Complete grain systems from Brock
Brock grain handling equipment, supporting structures, drying systems and storage bins work together to provide easy operation and long-lasting reliability. Your local Brock dealer designs installations using pre-engineered Brock solutions to move grain efficiently and with easy expansion in mind. Brock dealers not only provide site planning, system design and construction, they also deliver seamless support for all Brock components.
To get a complete grain system from one reliable source, contact Brock to find your nearest Brock dealer.
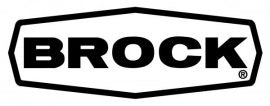