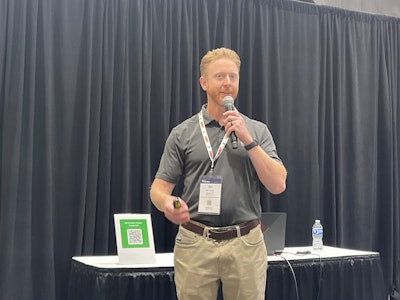
Bill Kreke, technical sales manager, Tritech. discussed both the importance and challenges of fall protection in grain facilities during a 2024 GEAPS Exchange Innovation Station presentation, Fall Protection Program Management.
Preventing falls is crucial because they consistently rank within the top five workplace fatalities and are the number one cited OSHA violation. Kreke stated that falls are pervasive because people often underestimate the risk in various situations, and mitigating the hazard proves difficult.
Kreke outlined a comprehensive fall protection program, including steps, key roles and a timeline, as an effective approach to preventing falls in grain handling facilities. For guidance on developing a program, Kreke recommended turning to ANSI/ASSP Z359, a fall protection and fall restraint standard.
"If you're the safety manager and administrator of that program, Z359.2 in particular spells it out for you," said Kreke.
Fall protection standards and roles
The standard addresses fall protection equipment and systems for climbing, work positioning, fall arrest, rescue, evacuation, and other fall hazards. It also covers training and how to identify and mitigate hazards to prevent injuries when working at heights.
ANSI Z359 states that every company with fall hazards must fulfill three key roles:
- Administrator: The person in charge of developing and implementing the program.
- Competent person: The direct supervisor of the work and the enforcer of the program.
- Authorized person: The program's users who require training on the proper use of fall protection equipment and tie-off points, etc.
Another common role in a fall protection program, though not required, is a qualified person. The qualified person does not necessarily have to be an employee of the company.
"They can be a contractor or with an engineering firm, but essentially, they are responsible for designing the fall protection systems used, reviewing anchor points, ensuring that the structure any fall protection is anchored to can support the fall arrest loads, and similar tasks," Kreke said. "The definition of a qualified person is someone who's been through education, certification, or both, in fall protection. Ultimately, you're looking at a professional engineer."
Program steps
A comprehensive fall protection program involves a hazard assessment process, identifying work areas with fall hazards, requires an engineer, and consideration of loads and anchor points in the design of fall protection systems.
"We're looking at work over four feet, such as wells, edges, any sort of equipment maintenance, someone who has to climb to get to truck access loading, railcar load-out, or rooftops," Kreke said. "Once you have those hazards identified, you've got to get an engineer involved."
The engineer, or qualified person, is responsible for determining anchor point strength for fall protection systems. While the industry commonly believes that all anchor points must support 5,000 pounds, this is not the case.
OSHA states that a qualified person can design a fall protection system to maintain a safety factor of two to one.
For example, "Most Safety Restraint Lines (SRL) and lanyards actually deploy at about 1,350 pounds, and the safety factor of two is only 2,700 pounds, so when that anchor point is engineered, you don't actually have to have the full 5,000 in every case because the engineer has reviewed that structure to make sure it's going to work."
Kreke emphasized that a fall protection program requires regular maintenance and ongoing commitment. Fall protection equipment must be inspected annually and recertified every five years.