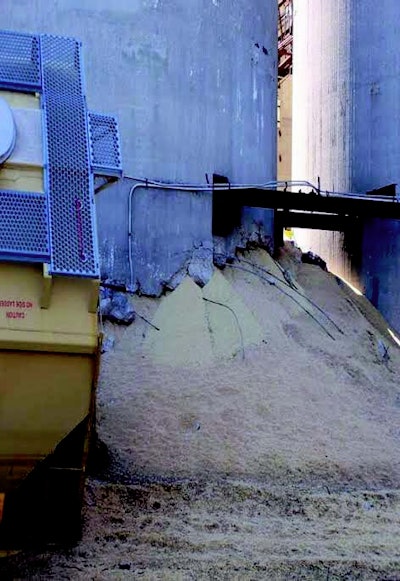
Though not often thought of as such, grain bins are the same as belt conveyors and pellet mills — pieces of equipment that must be taken care of continuously or risk failure. The difference is that when a bin fails, it can lead to more than annoyance and downtime — it can lead to millions of dollars in damage and put lives in danger. Some risks cannot be avoided, like the weather or a careless truck driver, but many are well in a company manager’s control.
The ground up
As grain towers reach higher into the sky, the loads they place on the ground magnifies. If the soil beneath the bin is too sandy or contains too much water, it can spell disaster. Calling out an expert to sample the soil before construction begins can help facilities from making the same mistake as the people who built the Leaning Tower of Pisa by making sure the soil can support the weight of a full grain bin.
“We see a fair amount of bins, especially because they’re getting taller, that aren’t always settling evenly,” explains Rodney Grossman, structural engineer at Brock Grain Systems. “Sometimes they end up leaning to one side causing damage to the bin as it tries to go obround.
Or if you have a catwalk attached to the roof, and the bin tilts, that catwalk will push and pull on the roof causing serious damage.”
The right bin for the job
Though storage bins appear to be the same from industry to industry, they are far from universal. Bins have to be designed for the type of material that will be running through them, the application used, and what type of loading and unloading will be done. Richard Kobetz, president of Sunfield Engineering, Inc., explains what can go wrong if the bin is not designed correctly.
“All kinds of different failures can happen,” says Kobetz. “A minor tearing, leakage, a little bending of one of the secondary structural elements, up to the complete catastrophic collapse of the structure.”
Construction
After the soil has been tested, the next step that can lead to critical failures is during the construction phase. When full bins are under enormous amounts of pressure, even a small mistake during construction can lead to further damage and eventually failure. Manufacturers provide directions on installation. These directions should be followed to the letter, and the manufacturer should be contacted if something doesn’t seem to be working properly. For larger bins, a trusted contractor should be hired. One that has a good reputation will have the experience to tackle issues that arise.
“We find things that boggle our minds sometimes,” says Grossman. “People will leave the anchors out, or there are stiffeners over the top of aeration tunnels for which they didn’t provide any support. These are things a knowledgeable contractor will catch.”
With the pressures involved in a fully loaded grain bin, even something as simple as the improper installation of temperature cables can lead to major damage. It is vital that all additional equipment is approved by the manufacturer/contracted company and placed in the right place on the bin. In the case of the aforementioned temperature cables, one of the more common mistakes is simply forgetting to take off the straightening weights before loading grain.
Unloading importance
Once the bin is up, it is just as important to use it properly. Many of the issues that lead to grain bin failure are caused by human error. Perhaps the most common human caused reasons cited for bin failure was improper unloading.
“When bin sidewalls fail due to excessive lateral pressure from gravity loads, it’s generally during the unloading process,” tells Kobetz. “In normal bins, withdraw of material causes over pressures.
Grain unloading is not an even process because of internal friction. It’s like a group of cars at a stop light: Once the light is green they spread out and then catch up again at the next red light. This discontinuous flow in grain causes a quaking effect. This in turn causes additional over pressures that are highly unpredictable.”
Those forces during unloading make it very important that bins are designed specific to the unloading function of that facility. It is not a simple matter to add new functionality to a bin after it is built; even small modifications can change the forces at work within a bin.
“A lot of times a facility will need to take its material out in a place that it wasn’t designed [to unload from], so they'll cut a hole in the side of the silo and stick a screw conveyor in it,” explains Michael Bailey, project and technical sales manager for Mole•Master Services Corp. “But that silo is not designed to flow that way and it puts a lot of stress on places not meant to handle it.”
This is especially true with older bins that have often been around for decades.
“Older bins were often designed to handle fewer cycles, and now go through many more cycles than they have been reinforced for,” says Greg Wurst, CEO of C-TEC AG. “Or they altered how the bin is unloaded, like adding a spout to the side to unload into a semitruck, and haven't refitted that area with properly added structure.”
New bins, on the other hand, have design improvements that make them stronger, if not impervious.
“Steel bins are typically designed to be center drawn, but bin manufacturers are starting to reinforce for the side draw in bigger bins where the loads are greater,” says Wurst. “It’s an ongoing process where they learn a little more from every failure.”
Weather
Some things are out of human control such as the weather. Keeping track of the weather and knowing the inherent risks will give facilities a better chance at beating Mother Nature.
- Wind is often thought of when a weather-related failure is brought up. This is only a concern in steel bins that are empty or only partially filled. Concrete bins, due to their sheer size and weight, are practically immune to wind unless in the late stages of decay. Steel bins can suffer anything from denting and pushed in roofs, to a complete overturn.
- Ice forming in the cracks of concrete silos can increase the rate of expansion. This type of weathering can make small cracks rapidly turn into big problems. It’s not the only thing that can happen during freezing weather. Cold with high humidity can cause damage to a grain bins in other ways, as Grossman explains.
“You can get frost buildup on the vent screens,” he warns. “If it plugs the vent, that is not a good time to be running your aeration system; it can create enough pressure to blow out the roof.”
- •Wet harvests, like the one in 2013, can cause issues for those without the dryer capacity to handle it. Wet grain weighs much more than dry, and bins are not made to be able to hold it or unload it.
“We’ve run into situations where the facility was storing a lot of wet grain without drying or aeration,and thought they could get away with it,” explains Kobetz. “Wet grain flows differently from dry grain and when it wouldn’t come out; they had multiple outlets open, a side draw and some floor draws, and tried to pull out of all of them at once. Bin walls aren’t designed for that and though it wasn’t a catastrophic failure — there were some serious cracks and deformation.”
Catastrophic events
Anytime something puts a large amount of stress on the bin, whether physical damage visible by the naked eye or not, it is vital to have a professional come out and look at the structure. This can be extreme weather, an earthquake that causes the ground beneath the bin to shift, damaging the foundation and loosening the soil beneath, or even something more common like a bin fire or grain bridge collapse. Anything that could change the integrity of the structure warrants a visit from an expert.
“With grain you often have a problem with hot spots,” warns David Laing, general manager of Mole•Master Services Corp. “The heat can stress the structure, whether it is steel or concrete, to the point where it no longer has its original strength.”
Inspections
Perhaps the simplest ways to make sure a facility doesn’t have an event that causes significant damage, downtime, serious injury or even death due to a grain bin collapse, is to instill a culture of safety into employees from upper management down. Devise a plan to monitor any potential trouble spots to make sure they are not getting worse.
“Go around and take pictures; then every six months go around again and take pictures of any trouble spots,” Wurst suggests. “You can start to benchmark it. That way you can go back and see how much [the problem] has deteriorated.”
Keep the staff on the ground in the loop. Ask them if they know of any issues or have noticed anything that is cause for alarm. They are the ones who are around the bins the most and are likely to know if a crack is new or has been there for years.
“Look for significant change in the structure,” suggests Laing. “It can be significant rust in steel or cracks, spalling, spidering, delamination of the concrete or if there is any shifting of the foundation. Call immediately if there have been any significant collapses of the material that can cause damage internally to the structure and should be examined.”
If there might be an issue with a grain bin, an expert will be able to tell if it is a serious issue or normal weathering by taking a look at photos or getting out to the bin itself. In this case it is always better to be safe than sorry.