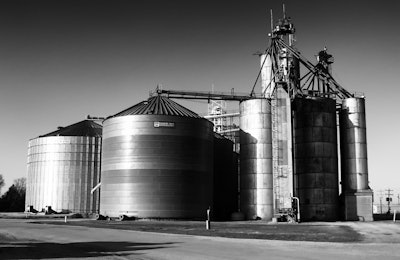
From the time grain comes out of a farmer’s field to the point where it is shipped from an elevator, everyone is trying to achieve a delicate balance in moisture content.
Too wet, and grain can wind up spoiling, clogging or causing any other number of undesirable situations. Too dry, and grain weighs less, meaning an elevator operator won’t have the same weight to sell as he or she purchased from a grower.
“The shrink is inventory you’ve lost. You’re losing money,” said Eli Troyer, owner of AgriDry in Edon, OH, which makes components and controllers for grain bins.
And there are quality issues that come with grain that isn’t stored properly.
“If you’re not monitoring your moisture levels well, it leads to other damage, like insect infestation or mold,” said Tom Runyon, president of Seedburo Equipment Co., manufacturer and distributor of handling, testing and grading equipment for the grain, feed and seed industries, based in Des Plaines, IL.
It “becomes an art,” said Scott Chant, president of Safe Grain, Inc., maker of quality control equipment for grain, in Loveland, OH. “It’s all about hitting that sweet spot and keeping it there. We have to have a strategy so you can avoid that shrink.”
Strategies differ for any number of reasons. Some elevators may measure humidity near their bins when cooling and drying grain while others do not, for example. Tools are different and goals may be different based on the region where the grain is grown or will be sold.
What remains constant, however, is that the more up-to-date the tools used to measure moisture, temperature and other variables, the more likely those numbers are to be accurate.
“There’s a lot of room for error in this system, whereas you minimize that risk with new automated equipment,” Runyon said. “You have to start with facts and good calculations to make these important decisions.”
Measure it
Grain that comes in too wet may have to be heated to get it to an optimal moisture level. The key to removing that moisture, Chant said, is the air movement through the grain.
“The air is what does the drying. You blow air through that product and it’s going to take moisture from the grain,” Chant said. “All the heat does is allow the air to absorb more moisture.”
From there, it’s all about cooling grain to a safe temperature.
Bill Sturtz, aeration division manager at Rolfes @ Boone, which sells grain temperature detection and hazard detection equipment in Boone, IA, said it’s important to cool grain to below germination temperature during storage, between 35 F and 50 F.
“The major point of shrink that I know of as a producer is at drying,” Sturtz said. “The real purpose of our equipment is to cool the grain down.”
But cooling grain also dries it, and it’s important to keep moisture content around 15.5% for corn and about 13% for soybeans.
Chant suggested getting grain to a cool, stable temperature and letting it be.
“Get your grain to the safe, desired temperature as quickly as possible and turn off the fans,” Chant said. “If you leave the fans running too long, you’re going to dry the corn or soybeans too much.”
For soybeans that wind up 2 percentage points under optimal moisture levels, for example, an operator may lose up to 35 cents/bushel. That’s money that adds up fast.
Finally, Chant said it’s important to use controllers and other equipment for what they are — tools. He says longtime operators should use their own common sense when it comes to making some decisions.
“Never allow a controller to make all your aeration decisions for you,” Chant said.
Troyer says operators looking to fine-tune their moisture measurements can monitor humidity and temperature as well. Troyer’s controller measures outside humidity, allowing an operator to take that into account when determining how much heat to apply to dry grain. A new product coming to market soon will allow humidity measurements inside the bin.
“By knowing what the equilibrium of the air is, we can change the moisture content of the grain,” Troyer said.
Carbon dioxide meters can also alert operators that something may be wrong with the stored grain.
“Elevated carbon dioxide can be an early indication of deterioration of grain,” Troyer said. “You could end up with spoilage in the bin.”
What’s the frequency?
A few years ago, many of the moisture meters on the market and used in elevators employed what’s called the capacitive method or RF dielectric method. A radio wave would be passed through a sample of grain. The radio wave changes as it interacts with water in the grain, changing the signal detected on the other end. A formula can calculate the moisture content of the grain based on the differences in the radio waves on either end.
Until about 2012, moisture meters like this used a low frequency, around 1 MHz to 15 MHz. But that frequency caused problems, specifically in freshly harvested grain. Soybeans, for example, might measure 2% lower than their actual moisture content.
For an elevator operator, that is potentially a significant problem.
“That understatement of 2% would not be taken into account in your price. That’s very expensive,” said Scott De Boef with Perten Instruments, a PerkinElmer company based in the U.S. and leading manufacturer of UGMA moisture meters. “That’s profit the elevator can’t get back.”
To compensate, many elevator operators increased their shrink discounts, reducing the price they paid the grower for the grain. But those growers weren’t always happy about that.
New meters use a much higher frequency, around 150 MHz, which De Boef says cuts the moisture reading miscalculation at least in half. But De Boef and others say that many of the elevators are still using the older technology.
“Elevators want to be accurate and fair. It’s a sensitive issue to farmers,” De Boef said. “It’s in everybody’s best interest to have the most consistent technology.”
For any of that to matter, however, Roger VanderKolk, analytical product manager at DICKEY-john, a global leader in official moisture meters, says grain buyers and sellers have to be on the same page. If an elevator operatorsuses a different type of moisture meter than a government tester or a grain buyer, that operator could lose profit.
“Accuracy breeds confidence. If you have an accurate moisture reading, you have confidence that what you put in is what you get out,” VanderKolk said. “You want to have the industry using the same tool.
“If you’re making a decision based on one technology or instrument and the person you sell it to uses another instrument, you may lose out on some weight,” Vanderkolk added.
Details, details
Up-to-date equipment may be more than half the battle when it comes to getting accurate moisture readings in grain. But that equipment is only as good as the upkeep and maintenance it receives.
The U.S. Department of Agriculture updates calibration data each year based on testing it does on that year’s grain. VanderKolk said many grain elevators do update their calibrations often, but he still sees each year a number of places that haven’t.
“Grain changes from year to year. You’d think that corn is corn, but there are always different varieties and different conditions that change the grain,” VanderKolk said. “It’s always best practice to keep calibrations up to date.”
De Boef said elevator operators can also send grain samples to USDA labs throughout the country to have them tested. If your own results differ from the lab’s results, equipment may need to be replaced or recalibrated.
It’s best, he says, to send in multiple samples to be sure an accurate evaluation is made.
“If an elevator wanted to really check his meter, that’s the way to do it,” De Boef said. “We recommend at least three different samples.”
Many of the controllers and other equipment used in elevators also require fans, vents and other bin components to be in good working order to meet targets for grain moisture. A clogged vent or nonworking fan will throw off the calculations an operator makes.
“Check your fans in manual mode,” Troyer said. “Make sure they’re turning on.”
Accurate moisture measurements mean a lot to the bottom line of both growers and elevator operators alike. But they can also be a matter of life and death.
Grain with high moisture content is more likely to cake and crust, causing problems with how it flows. Many of the grain bin deaths — there were 33 in 2013 in the U.S. — occur when someone climbs down into the bin to break up grain to help it flow.
“If you can control the temperature and moisture of your grain, you can monitor quality, prevent spoilage and keep people safe,” Troyer said.