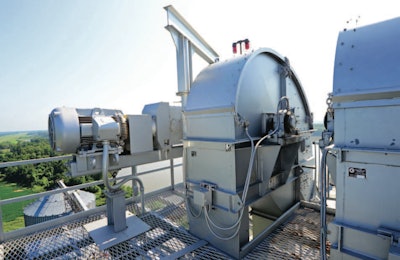
In all aspects of business, having dependable equipment is crucial to ensuring optimal performance and profitability. This couldn’t be truer in the feed and grain industry where time and productivity is of the essence. However, the conditions to which electric motors are exposed to in this environment are very different from typical electric motor applications like warehouses or manufacturing facilities.
The most common electric motor failure in the industry is by far bearing failures. In feed and grain facility applications, these failures can be attributed to a number of factors. The most common is exposure to weather and the elements. For instance, the auger motors found on the legs of grain bins is one example of an outdoor application where shelter is typically not provided. In order for these motors to provide a respectable service life, it is imperative that they feature proper shaft sealing and moisture protection.
Troubleshooting lubrication problems
Not always is weather or moisture to blame for bearing failures. Correct lubrication and maintenance is key to ensuring long service life for any electric motor. Some common questions fielded over the years surrounding lubrication include:
- Why do some motors have grease fittings and some do not?
- How often should I add grease to my motor?
- What kind of grease should I use?
- Why is there a puddle of oil coming out of the grease relief?
Motors with grease fittings feature regreasable bearings, while motors without grease fittings feature double sealed, lubricated for life bearings. Do regreasable bearings last longer than sealed bearings? The answer to this question all depends on the greasing frequency, and if the correct, or compatible, grease is being applied.
For an electric motor that is running 24/7/365, itmay only need to have grease reapplied once or twice a year. The standard grease for most all electric motor manufacturers is Polyrex EM. If incompatible grease is applied, the physical and chemical structure will be altered and one of two things will happen:
- A reaction will occur preventing the base oil from being released, so the grease hardens like clay.
- A reaction will occur causing the base oil to be released from the chemical structure producing an oil puddle.
Overcoming voltage sag
Another set of common problems found in feed and grain industry applications is low supply voltage at the motor and voltage sag. Voltage sag is usually the result of starting multiple motors at one time. Performing a staggered starting sequence will help to prevent a voltage sag situation from occurring. Low voltage situations, on the other hand, are common largely because of the rural nature of this industry and being far from the power source on the grid. It is a good idea to meter the voltage before connecting a motor or piece of equipment to ensure that adequate line voltage is available.
In rural areas it is not uncommon to see 230-volt service actually meter closer to 200 to 208 volts. Trying to operate a motor outside of its allowable voltage limits can cause welded switch contacts, failed start capacitors, and even premature winding failures.
To prevent these types of problems, it is a good idea to meter the voltage before connecting a motor or piece of equipment. If a low voltage situation is discovered, there are electric motors designed to accept 200 to 208 volts. The best practice is to always contact a local motor shop or the equipment supplier for advice on how to proceed if the voltage is lower than the specified requirements.