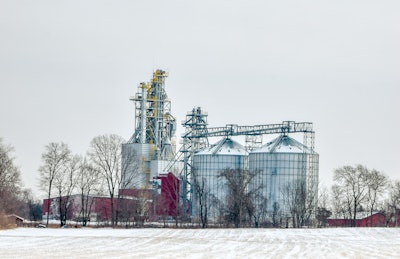
When feed manufacturers and grain elevators think about the ways they come in contact with the government — local, state and federal — what comes to mind are the regulations and permits required to run their businesses. But few companies find themselves affected by government intervention in the same way Hoover Feeds of Goshen, IN, was.
“My dad David Hoover started Hoover Feeds in 1974 on our farm,” said Herb Hoover, owner of Hoover Feeds. “We were just using soybean meal and mineral premixes back then, but it was kind of new at the time for dairy. Eventually, we got large enough to lease a feed mill for five years and then bought a mill in Goshen, IN, downtown.”
“We knew about the possibility of Hwy. 33 expanding when we bought the mill 19 years ago,” said Hoover. “Periodically, talks about expanding the road would come back in full force, but something would happen and you wouldn’t hear anything.”
Until 2014, 15 years after the mill was initially purchased, word finally came — Hwy. 33 was expanding.
A chance to build anew
No company wants to be forced to move its operations. It should be a carefully thought out decision, executed at the ideal time for the business. But things move quickly when the government knocks and serves you an eviction notice. In the four years since Hoover Feeds learned it would have to leave its downtown location, they found a new site, waded through the regulations needed to build a new facility, chose a plan, selected two builders and constructed a facility large enough to support their current and future consumer base.
“While working through this whole eminent domain process with the state, there [were] things we didn’t expect to deal with,” explained Hoover. “But we were at capacity at the other mill, so once we were on the same page with the state, we were able to plan a new facility that could meet our needs.”
Eminent domain requires the government to pay fair market value for land, and Hoover agrees that the compensation was fair; however, it still only covered a portion of the new facility’s cost. The new facility plan featured both a grain elevator that could take in grain from surrounding farmers — something lacking at the downtown location where bulk product had to be trucked in — and a feed mill that could process grain into one of the company’s product lines, along with enough storage and space to keep product on hand.
The site selected for the new mill was a defunct farmstead on the outskirts of town, away from the busier narrow roads of downtown Goshen where traffic could grind to a halt during rush hour.
“The new location has really opened up traffic flow,” Hoover said. “You don’t feel closed in like we were in town, as though you’re always in somebody’s way. With all this openness we feel like we’re operating the way we should be.”
Separate companies handled the engineering and construction of the new location. Clear Creek & Associates, Goshen, IN, engineered the site and grain elevator; Hochstetler Grain Equipment, Nappanee, IN, built the grain storage and elevator; while AGRA Industries, Inc., Merrill, WI, engineered, built and provided much of the equipment for the feed mill. With so many different crews on-site during the build, and feed manufacturing continuing at the downtown location, the build was chaotic at times.
“For a while we had two contractors on-site, two sets of vehicles, equipment and workers and mud everywhere,” said Hoover. “But everything worked out, and we were able to start making all our feed here Memorial Day weekend 2017.”
Going with the grain
“We didn’t dry grain at our last location,” explained Hoover. “But if we were going to be out in the country, we wanted more access to local corn, which meant adding a dryer.”
Chief Agri-Industrial, Grand Island, NE, provided the continuous mixed-flow grain dryer — the center of Hoover Feeds’ grain handling operation, capable of drying 2,850 bushels/hour. Brock Grain Systems, Milford, IN, supplied two stiffened grain bins and two hopper bottom bins, which store an equal amount of wet and dry grain for a combined 610,000 bushels of storage.
All of the conveying equipment on the grain side of the facility was provided by Brock Grain Systems. Grain is moved to the bin by a 15,750-bushel/hour elevator leg with buckets by Tapco Inc. of St. Louis, MO, into a distributor. The grain is then sent directly from storage to the mill by two 15,000-bushel/hour drag conveyors.
For the plant automation, Hoover Feeds relied on its existing relationship with Repete Corporation, Sussex, WI, who also handled automation at their old facility. The mill manufactures pellet, meal and textured feeds for the local dairy farm operations, so automation of the process is important to quickly change the type of feed being manufactured.
“We had worked with Repete before and they have always been very accommodating, so we went with them again,” Hoover explained.
Feeding growth
The new mill can manufacture 250 to 400 tons/day running one full shift and employs 16 people, including drivers.
“Once we receive all the raw ingredients they go into producing either meal, pellet or texture feed,” Hoover explained. “Our pellet and textured feed are our niche in the feed business.”
Hoover Feeds didn’t have to start completely from scratch with the move. They were able to bring some of the machinery from the old mill with them, including one pellet mill by Bliss Industries, LLC, Ponca City, OK, capable of milling a combined 25 tons/hour and sits beside one brand-new pellet mill. Bliss also provided the pellet cooler, pellet crumbler and Bühler Inc., Minneapolis, MN, vertical hammer mill.
Hoover Feeds also brought the textured mixer, steam flaker and flaking mill from the downtown mill, and a new dryer-cooler for the flaked corn was purchased from B.N.W. industries, Tippecanoe, IN, while Scott Equipment Co., New Prague, MN, built the mixers.
The mill tower holds 72 square bins and 46 ingredient bins, supplied by AGRA Industries, Inc., for approximately 1,500 tons of ingredient storage and 450 tons of load-out capacity. The mill can receive 7,500 bushels/hour.
A majority of the feed produced at the new mill is bulk feed, and in order to deliver it to the dairy farms who make up their customer base, Hoover Feeds operates a fleet of Hensley Fabricating & Equipment Co., Inc., Tippecanoe, IN, vehicles. The fleet consists of four auger-semis, three triaxle straight trucks, two tandem straight trucks, one box truck and one hopper-bottom trailer for hauling ingredients.
Feed bodies can be loaded in as little as 10 minutes depending on the type of feed being carried. The mill has three truck bays, one specifically for textured feeds, one for receiving and one for other bulk feeds.
Community ties
Hoover Feeds has been a part of Elkhart County, Indiana, for over 40 years and a staple of downtown Goshen for almost 20. The customer facing portion of the new mill is a mixture of new and old — an homage to the homestead that stood in the downtown location before it.
Most of the homestead was torn down, but Hoover Feeds decided to restore the barn on the site to act as a drive-through pickup for bags of feed. They shored up the barn to make it stable, and opened it up so vehicles could fit inside.
“Around 95% of the feed we make is bulk, but we have about 350 customers throughout the delivery chain and farmers who walk in the store to pick up feed,” said Hoover. “The barn on-site was restored to easily allow farmers to drive in and load bagged products.”
The barn also provided wood for the front office’s rustic theme, where customers come in to order their feed and enjoy a cup of coffee.
When David Hoover started Hoover Feeds with his son Herb on their farm in 1974, it was a family business — it still is today. Though Herb’s father is currently enjoying his retirement, he’s still involved with the mill and Herb’s sons work alongside him on the mill floor, learning the trade from their dad. Care has been put into every design choice from the barnwood accents in the office on-site to the red paneling on the mill itself. Hoover Feeds’ new mill is built to last and continue to be a part of the community it was founded in.
“While the process of building a feed mill and moving the business created some stressful situations, I relied on my great employees, strong family and most important, my faith in God,” said Hoover.