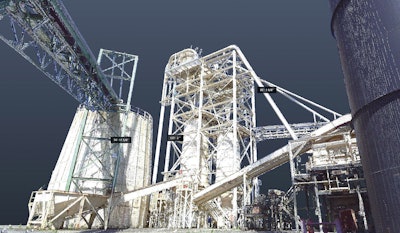
While not necessarily a new technology, high-definition surveying – or laser scanning – has become an economic choice used by design-build firms to capture a highly detailed 3D image of a project.
Instead of using traditional surveying tools, lasers are used, creating higher accuracy and safer working environments during assessment phases of the project. Once data is captured, it can be used for analysis, creating a model, comparing drawings for quality assurance and creating a future record.
Measuring at the speed of light
Laser scanners have a 360-degree view. They are designed to measure and record a series of points along the exposed surface in the environment around it.
“3D laser scanning is being used to measure structures in high detail,” says Larry Kleinkemper, AIA, with Lanmar Services in Round Rock, TX.
Kleinkemper explains that the laser scanner uses LiDAR — Light Detection and Ranging.
“The scanners project a small beam of infrared light, the light travels to a surface and is reflected back to the scanner,” he says. “By dividing the amount of time it takes for the light to travel from the instrument and return from the reflection of the surface by the speed of light, we can tell the distance the light has traveled.”
The laser scanner turns as it is scanning, so it sees 360 degrees.
“The only surface it can’t see is directly below it,” says Kleinkemper. “While the scanner turns, it takes millions of measurements per second.”
Unlike other methods that capture individual points one at a time, a 3D laser scanner can capture the detail of an entire building or structure.
Scans are recorded at a higher speed than traditional surveying methods. At a high resolution, 250,000 points can be documented per second, decreasing the amount of time it takes to measure points.
A laser scanner can also collect more data from areas typically missed or difficult-to-reach by traditional methods, increasing the accuracy of the survey.
Laser scanners can gather data from a safe distance away, eliminating the need to put up scaffolding and place employees in perilous situations, creating a safer work environment.
“With a laser, you can measure an object that’s 100 feet in the air from the ground,” says Kleinkemper. “As far as time goes, you can save a lot of effort. As far as safety goes, it’s invaluable.”
Another safety benefit — 3D laser scanners can be used to identify vulnerable and unsafe areas, reducing accidents and injuries.
Benefits
A major benefit of 3D imaging systems is the ability to capture existing conditions more completely and with a higher level of detail than most manual methods, says Kleinkemper.
“Laser scanning can show us many things about a structure that we may not see with our eyes,” he says. “It can show if structures are leaning, bulging, sagging or cracking. The scans tell us the dimensions and sizes. We can also see how thick a wall or roof is when we scan on both sides.”
Additionally, ranges can be measured to non-specialized targets, objects or surfaces (i.e., there is no requirement for a special type of material or the need for highly reflective surfaces).
Other benefits of using a laser scanner include:
- Increased accuracy and reduced variance in engineering and construction bids
- Reduced errors and rework
- Improved responsiveness to project changes
- Schedule reduction
- Increased worker safety
- Improved quality control
- 3D visualization and spatial analysis (i.e., line of sight)
Simply put, laser scanning will provide a more precise drawing than any other method available today. This increases efficiency because it detects errors earlier in the process, decreases rework and keeps projects on schedule.
While 3D laser scanning is fairly new and well received by some in the industry, more benefits of the technology will begin to emerge as it becomes more mainstream and more design-build firms adopt its use. ■
How laser scanning works
A 3D scanner shoots a pulse of light with a laser to the surface area being scanned then records the amount of time the reflection takes to return to the scanner.
The scanner then creates a representational point for where the pulse hits the surface being scanned. The points the scanner records in the computer form a “point cloud.”
Some scanners can also capture the color of the surface area and map that color to the points. The point cloud becomes a visible representation of the area scanned. Through a viewer program, you can navigate through, explore and see the scanned area.
Most importantly for architects and engineers, the point cloud can be measured and dimensioned. Measuring curves, high ceilings and historic facades becomes easy.
The ability to view and measure the project directly from your computer reduces the need for
additional trips to the jobsite. Fewer jobsite visits can significantly drive down project costs.
The point cloud becomes significantly more useful when the points are converted to create surface geometry. Surface geometry can be imported into BIM to provide an accurate model of existing conditions in a building or on a site.
Information provided by Lanmar Services. For more information, visit lanmarservices.com.
Other imaging tools
Thermal imaging cameras are handheld instruments that measure the heat differential of objects in the view of a camera. These tools are getting more affordable and smaller, like the smart phone attachment, FLIR One. Thermal imaging cameras can be used for electrical inspections, roof leak detection, plumbing blockages and heat loss/air infiltration.
3D/2D GPR (Ground Penetrating Radar) is an electromagnetic energy signal that penetrates through the subsurface. GPRs are comprised of three elements: control unit, antenna and power supply. Antennas feature various frequencies depending on the application it’s being used for. Higher frequency units are typically used for shallow depth, smaller targets such as those found in concrete applications.
Drones can be equipped with cameras and photogrammetery to measure a project or worksite. While not as accurate as laser scanning, drones can still save time by more easily measuring the productivity and quality of a worksite with eyes in the sky.
Artificial intelligence is much more futuristic, but it is starting to be used on some construction projects. Autonomous equipment is capable of navigation without human input. In the planning stages, AI machinery can survey a proposed construction site and gather enough information to create 3D maps, blueprints and construction plans.
CCS Group offers assessment with non-destructive technology
CCS Group offers a Structural Assessment process designed to gather structural history of a facility and use the newest non-destructive technology to provide insight, testing and data.
Encompassing a complete interior and exterior site inspection, the structural assessment report will offer information on the physical condition of the entire property, with professional recommendations.
Some of the tests covered include:
- 3D/2D GPR reinforcement steel scanning
- PSI concrete tests
- Roof beam inspection
- Hopper inspection
- Surface profiling
For more information, visit ccsgrouponline.com.