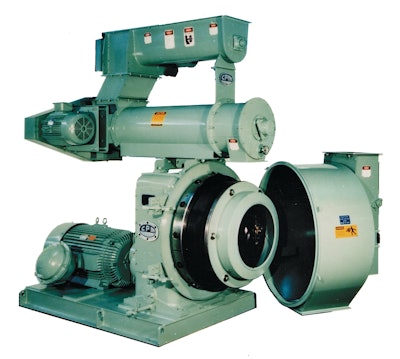
Pelleting is at the heart of the integrated poultry industry. In addition, the swine industry, commercial feed industry, and co-products industry heavily rely on pellet mills. Plant managers are always between a rock (nutritionists) and a hard place (stakeholders). Managers are continually pushed to get feed out the door quickly and with minimal fines. This is not to forget the additional safety factors (OSHA) and food safety factors (FSMA) that demand operations continually improvement.
We typically characterize pelleting two ways: production rate and quality. Unfortunately, these two are not symbiotic, and in fact, they have an inverse relationship. There is a well-recognized list of factors which influence pellet quality. These parameters include: formulation; conditioning; die specifications; particle size; throughput; and cooling.
What is not mentioned in most literature as a factor for pellet production is personnel and documentation.
A pellet mill (which is new or with a new set of rolls and die) is a baseline for measuring outputs. Yes, a break-in period should occur for some short period (e.g. 50 tons), however, once this is completed a pellet mill is a fixed machine and it does not change for some time if set as per the OEM reference guide. A pellet mill is just a machine — a tool if you will. If it does nothing, it does not change. External factors are all that we have to operate, monitor, manage, and document what happens.
Scenario
Here is a “play by play” audit situation:
Plant Manager: Production capacity has decreased significantly over the last 3 weeks.
Auditor: Has anything changed with in the formula?
Plant Manager: No. Same formula, we got DDGs from over in Illinois instead of Nebraska and saved a bunch on shipping.
Auditor: Let us open the door and check the rolls and the die. Did you notice the die holes are rolled over with tramp metal in here?
Plant Manager: How is that? The die is new?
Auditor: When was it installed?
Plant Manager: I don’t know. Let me look. Oh, 6 months ago.
Auditor: So we have about 100,000 tons on this die. Who is operating the pellet mill at night?
Plant Manager: Paul, we just hired him a month ago.
As many of you may have already addressed items which influenced production rate and pellet quality, there is compounding effect of all of them together which also is overlooked. The feedmill received different DDGs (formula/purchasing), the die was rolled over with tramp metal (not checking magnets OR raw ingredient problem) on a seasoned die (i.e. well used), with a novice operator (which more probable than not over tightened the rolls to reduce slip).
Management is so often stretched thin dealing with not only operations in the mill, but logistics with incoming raw ingredients and outgoing feed, governmental regulations (OSHA, FSMA, EPA), human resources, live operations, and many others. An excellent tool for one to use is a pellet mill journal log (Table 1). A journal is very functional in many areas to maximize an operation:
- OEM Discussion
- Maintenance
- Nutritionist
- Purchasing
- Personnel
OEM Discussion
This is a two-way street in discussions. As a general rule, OEMs want to have a satisfied customer. If a difficult situation arises, a detailed journal and maintenance log can go a long way coming to a resolution.
Maintenance
Maintenance can be the difference between being successful or just getting by. Having a detailed pellet mill journal and maintenance log will allow management to evaluate outside of just costs/ton but also answer questions such as, “Do we need to reevaluate the budget for a new machine?,” “Can we source spare parts which are better?,” “Throughput is off, did maintenance make adjustments?”
Nutritionist
A nutritionist drives many decisions, but is responsible for formulation, which has a significant effect on production capacity and pellet quality. Data showing formulation changes which are inconsistent and frequent may be cost more regarding production “uptime” than what least cost formulation is trying to save.
Purchasing
Discussion of material sourcing, which has an effect on pellet operation, is critical. As new crop/old crop transitions occur, and those different sources are arriving, it is vital for operations to know ahead of time for preparation. If there is better purchasing opportunities for sub standard ingredients, this is good to know as well.
Personnel
Understanding who and what is occurring over a period of time can support management in discovering situations which may or may not be occurring.
Jase Locke, territory manager for South Central US with Andritz, Inc., states, “When customers contact us regarding pelleting issues, it is typically one of two questions: ‘Why has my production level decreased’ or ‘Why has pellet quality dropped?’” Locke continued, “I will ask a series of questions as to the situation, such as how many tons are on the die and rolls or have you had a formula change. Most manufacturers are not only looking for production capacity, but increasing production efficiency.”
Scott Anderson, general sales manager with CPM Roskamp addresses inquiries from customers stating, “We are addressing issues with pelleting as mechanical concerns and application issues. We know right now in January, companies are having a difficult time achieving conditioning temperatures”. Anderson also added, “We are also seeing the particle size of many of co-products varying quite substantially, not just DDGs. The results are a significant negative effect on pellet production.”
Action Items
Do you have and use the OEM manual? If not, get it. Once again, when you contact an OEM and advise them that production is reduced or pellet quality is poor, have data ready to discuss. A short list of OEM questions that will be asked include:
- Was there a formula change?
- Did you receive ANY raw ingredient from a different source?
- How old or what is the condition of the die and rolls?
- Did you open the door and look?
- Did you have any changes to the steam system?
- Did you change or add boiler water chemicals/treatment?
- What is the steam pressure at the pellet mill? At the boiler?
- Did you change grind size of the cereal?
- Was there a personnel change?
- What is the moisture content of the meal going into the machine? Out of the pellet cooler?
- Where did you collect your samples at? Did YOU collect the sample last time?
- Finally, what has Maintenance staff done to the machine?
Conclusions
There are so many items influencing the pelleting process, we must strive to improve the process, and documenting what the circumstances is most critical. If we don’t measure it, we can not manage it. Reach out to the OEM of your pellet mill. If something is wrong and they do not know the situation, they can not address it or support you.