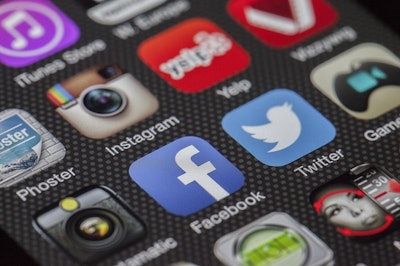
Just as web technology has invaded other industries, providing unparalleled access to data, agriculture is no different. What started out as the exclusive realm of desktop computers has very quickly expanded into a new arena of web applications, or “apps” as they are commonly referred.
Improving the quality of interactions
Grain producers and grain facility operators have been quick to embrace emerging technology developed by Myriad Mobile, which reported in November that its 5-month-old Bushel app had been used by more than 180 grain elevator locations and 20,000 growers in seven states: Colorado, Kansas, Iowa, Minnesota, Montana, North Dakota and South Dakota. The app logged more than 400,000 screen views with 75% of the elevators’ customers adopting the technology.
That’s an exceptionally high adoption rate for mobile apps, which didn’t surprise Ryan Raguse, chairman and co-founder of Myriad Mobile and Bushel.
“The ability for growers to track scale tickets, contracts, price later contracts, prepays, cash bids, futures, news and notifications is a huge benefit for them,” he explained. “To do that either at home or while sitting on a tractor in the middle of a field provides great flexibility.”
In the past, growers relied on home computers to access data. Today, growers don’t even need stellar internet access to get the Bushel app to work. The software is native to the device, which means the app simply downloads a small data file to populate the screen rather than downloading large graphic files.
In developing the app, Myriad Mobile assumed that it would reduce phone calls to grain operations; but no noticeable decline occurred. However, the interactions were faster and more to the point after growers had already educated themselves by reviewing data before making the calls.
“Growers use the app as an administrative assistant to access data so that when they call the facility, they are doing so to get advice. The quality of interactions is much higher,” Raguse explained.
Developed at a cost of $1.5 million, not only can the app plug into any grain elevator and provide data to growers, but it can be used to push notifications to them announcing expanded hours or problems, such as a leg down at the plant. Growers will soon be able to pay invoices and sign contracts through the Bushel app. In addition, the Bushel team is working on a grain offer system.
The cost to use the app is free to growers, and grain facilities pay a monthly subscription fee. It works on Android and Apple systems as well as web browsers. Secure login uses the grower’s phone number and text authentication. No registration or passwords are required and the grower stays logged in for a year.
Making contracts simpler
Greenstone’s MyGrower integrates with agri-business ERP software used by co-ops and elevators to pull data from contracts, settlements, tickets, invoices and prepaid amounts in real time. Companies have flexibility in determining what information can be shared with growers.
“Farmers access account data without having to call the mill or elevator, which reduces the amount of staff time needed to research and convey information,” said Mark Norris, a strategic growth analyst.
Growers can make on-the-spot decisions beneficial to their businesses. For example, if a grower is harvesting a field and the first truck comes to the elevator with high moisture content, the app can alert the farmer immediately so that he can allow the field to dry out a few more days, said Pat Mahapatra, Greenstone general manager. “If the grower could only access data at night when he returned home, it could be problematic,” he added.
MyGrower allows data to be pulled from different databases and combined into one report. Customers can determine how long to make data available to their growers, whether for the current season or several years. Access to historical information is especially important around tax time.
In 2015, Greenstone saw a high percentage of growers using smartphones to access weather information, news and music while spending hours on a combine. So, creating an app for Android and Apple devices made sense.
“We decided if we present data to growers directly to their phones, they will find value in it,” Mahapatra added. “Now growers don’t have to go home to spend an hour and a half printing invoices and looking at statements. They can do it on the fly, in the field, without being shackled to a computer at 8 p.m.”
Upcoming releases to the MyGrower app will feature two-way communication to approve contracts or order fertilizer. Greenstone is working to allow growers to sign binding contracts directly from the app, similar to how home buyers electronically sign loan documents.
“Say a grower wants to deliver 30,000 bushels of wheat next year. In the past, he had to call in to work out a time frame for delivery, perhaps establish a price and create an agreement to sell X bushels of grain. The merchandiser had to write up a contract and key it into the system. From there, it had to be printed, copied, faxed, scanned or held for the farmer to sign,” Norris explained.
“Our app will send digital notification to the grower, who will log in to review pending contracts. He signs it through a digital process, which then updates the record and eliminates the need for a grain elevator to follow up on pending contracts.”
Some growers are managing up to 40 different contracts, which is a lot of paperwork to manage, he added, noting the app will save time, postage and physical storage space by moving everything to a cloud-based system.
Safety training made fun
Nationwide Insurance saw an opportunity to improve training by creating a virtual reality app, HazardSpotter SM, that appealed to younger tech-savvy workers for whom technology is preferred over textbooks and traditional learning methods.
In a collaborative effort among multiple departments, the staff reviewed claims data and regulation violations as well as workplace hazards so that preventive controls could be implemented.
Next, the staff interviewed customers to discover the most cost-effective, beneficial way to not only provide training, but to also ensure that it re-enforced the urgency to keep employees safe. Then, the firm hired a third-party vendor to create the interactive app.
“We want people to make mistakes in a virtual reality environment and learn from them so they won’t repeat those mistakes in a real-world situation,” said Freeburg. “Scenarios include housekeeping, preventive maintenance, hot work and more. Players are scored on their completion of the task, proper documentation, ability to identify hazards and proper use of equipment.”
HazardSpotter is set up like a typical video game played on smartphones and tablets. Users earn points as they navigate the facility and make correct choices in selecting equipment or following required procedures.
“The app starts in the office where a player receives work assignments related to a grain-handling in the boot pit area. From there, he goes through daily tasks and must pick appropriate personal protection equipment and follow established lockout/tagout procedures,” he added. “If the worker selects the wrong equipment or doesn’t follow the process correctly, his actions result in an event that ends the game. That way the worker knows disasters can happen in real life resulting in injury, death or property destruction, if he isn’t paying attention to correct procedures.”
The system works on Android and IOS devices. Freeburg said that even though the app was designed with the millennial generation in mind, older workers are having fun using it, too.
Simplifiying lockout/tagout and safety audits
One of the biggest benefits of using applications is they transform complex tasks into simple procedures. Creating a lockout/ tagout procedure can be a drawnout process requiring hours to log steps required to account for every piece of affected equipment.
AgriSphere’s app helps grain operations comply with OSHA regulations by documenting the procedure to ensure machines can’t be operated before maintenance or cleaning is performed.
“It doesn’t matter if it is a drive shaft, screw auger or belt conveyor; a component may be rotating, bending, sliding or shaking. If a worker gets clothing or body parts caught in those moving assemblies, it can lead to serious injury or death,” said CEO Frank Byers. “It is essential that people be prevented from accidentally starting equipment by either physically locking the machine or conspicuously tagging equipment to alert others that it should not be operated.”
OSHA requires step-by-step procedures be in place for all equipment with moving parts which require maintenance and service, with few exceptions. Depending upon the control mechanisms, creating that list can be daunting to account for every step, Byers explained.
“We have seen as many as 20 actions involved with applying a lock or tag on some equipment,” he added. “When you calculate the amount of mechanical, hydraulic, pneumatic or electrical equipment covered by the requirement, even a mid-size plant can have hundreds of individual procedures to catalog. It is incredibly time-consuming.”
Creating a proper lockout/tagout procedure often requires a lot of administrative time for people with head knowledge, but who may lack time or skills to sit down at a computer to assemble the procedure. The AgriSphere app does the heavy work by utilizing templates.
Once a template is set up, creating the procedure is often as simple as rearranging the steps, deleting those that don’t apply or adding a sentence or two pertinent to a particular machine. The app also allows a photo to be attached to the step to make it crystal clear what needs to be done.
“If the step requires switch No. 3 to be shut off, you can take a picture of that specific switch and its location on an electric panel, and then attach it to that step,” said Byers. “The app offers a lot of flexibility so people don’t sit behind a computer typing one step after another for months.”
Once the procedure is built, the app allows users to access the information online or print it out for storage in a binder. The master copy is stored in the app so future changes are easy to complete.
“This is especially beneficial for a central safety director who can review, approve and update the lockout/tagout procedural information without having to drive to a facility,” he added. “Our application can also be used to track and manage permit-required confined spaces as well as the specific regulatory requirements for documenting employee interaction and atmospheric testing for those spaces.”
Managers use the app to determine whether a scenario meets the regulator requirements to identify a permit-required confined space.
“Real or potential atmospheric hazards, among other factors, define the need to label a space or piece of equipment as a permit-required confined space,” said Byers. “The app allows managers to create a matrix of confined and permit-required confined spaces for their facility.”
Users can enter atmospheric data on a routine basis if they are actively engaged in an atmospheric characterization program to declassify certain permit-required confined spaces. The safety director will be notified that an evaluation can be completed to downgrade the space so it doesn’t require a permit based on the historical atmospheric testing data.
The confined space/permitrequired confined space application matrix also feeds a digital Permit Required Confined Space Entry Permit Form which can be completed via tablet or computer, or printed if required.
Safety supervisors also appreciate the app’s audit management feature using the cloud-based program to take pictures, cite specific OSHA regulations, attach notes and create corrective actions right on their tablets.
“It is not uncommon for an audit to have more than 100 line items, ranging from simple items to more complex compliance issues,” said Byers. “Managers can refer to the app to evaluate pending problems, formulate a plan to address compliance issues, ensure issues are being resolved, or whether items need to be added to a capital project. They can manipulate, track and document all the corrective action taken right from the app and even show it to
OSHA inspectors via reporting, if required.
As technology advances from year to year, whatever the pain points growers and grain operators experience today are likely to disappear as more people hear those magical words – “there’s an app for that!”
MobileDefender keeps workers safe
Accounting is a vital function of apps, but devices can also be used to improve worker safety. SecuraTrac's MobileDefender is a cloud-based enterprise portal used by grain operations to keep track of staff and whether they are healthy and working. It detects falls and unresponsive workers so that help can be summoned.
The mobile personal emergency response system (mPERS) works by simply pushing a button and activating a speaker on the device. It works two ways:
First, a worker wears a device on a belt or lanyard. When in trouble, pushing a button immediately communicates with satellite and cellular towers to triangulate the worker’s location within 5 to 10 feet. Information is relayed to an emergency response center where trained staff communicates directly with the worker to determine the problem.
Second, if a worker falls, the device senses movement, the speed at which it occurred and whether the device begins moving again. If no movement is detected within 15 seconds, the device notifies the response center.
The device even works if someone is in a silo or grain bin surrounded by metal and concrete. MobileDefender is set to send a signal over cellular networks updating its location every 5 to 20 minutes, and retains that information as a "breadcrumb." So, even if communication is impossible and the device has not "pinged" the response center within 15 minutes, crews can be dispatched to the last known location to assess the situation. Companies can set up devices to either communicate immediately with 911 or call safety team members first.
Battery life is typically 48 to 72 hours before a charge is necessary. However, the automatic updates can be turned off and the device placed in deep hibernation so that it checks in once a day at midnight unless the SOS button is activated. In those instances, batteries can last up to 45 days.
"Fall detection is the biggest benefit of using MobileDefender," said CEO Chris Holbert. "The device looks at the impact of the fall to determine if it is 'soft,' like landing in a bed of grain, or 'hard,' like falling on grass or concrete."
False notifications are prevented because the device only activates if it senses a change of angle greater than 70 degrees and remains immobile for 15 seconds. Even then, MobileDefender emits a high-pitched noise for five seconds to alert the worker who can pick up the device and tap the SOS button once to cancel the alarm.