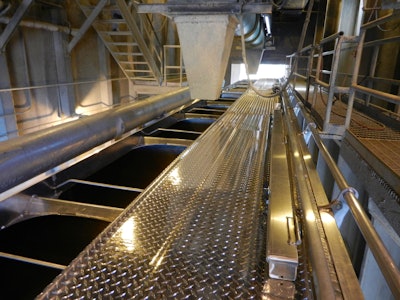
Highly pathogenic avian influenza (HPAI )H5, better known as the bird flu, infected 49,700,000 birds in the United States between December 2014 to June 2015, according to the United States Department of Agriculture Animal and Plant Health Inspection Service. In the Congressional Research Service Report R44114, Joel L. Greene estimates the value of the birds lost at nearly $1.6 billion, and the total economic loss at $3.3 billion. Those numbers launch the2014/2015 outbreak to the top spot as the most deadly and costly avian influenza outbreak in U.S. history, and show the value in continuingly monitoring and upgrading an operations biosecurity plan.
With billions of dollars on the line and the potential of entire operations being ruined, biosecurity continues to grow in both urgency and necessity. One of the key pieces to a working biosecurity plan is finding a way to diminish the risk from outside vehicles, such as feed bodies, that move from farm to mill to farm, picking up dust and pathogens up from each site. There are solutions to help mitigate the biosecurity risk that every shipment of feed brings with it to an operation, but some are not practical at every site.
With older sites, or sites with limited space, where complete isolation of outside vehicles is impossible, or even at sites where segregation is practiced but even more security is desired, there are still steps that can be taken to sanitize the feed bodies themselves.
Wheel sanitation
Perhaps the easiest solution to keeping this link in the biosecurity chain strong is by adding a sanitation solution to the trailer itself. This simple but ingenious solution has the driver of the feed trailer quickly spray a sanitizing agent onto the tires as they pull up to the operation. This can be a very effective way to kill pathogens living on the tires of the feed body.
“It’s effective if used in the right manner,” said Terry Medemblik, president of Walinga USA Inc. “Meaning, the driver has to ensure that he sprays enough disinfectant on the tires. The tires need to be coated reasonably well, so they have to get more than one revolution of spray allowing the disinfectant to make good contact and get absorbed into the tires.”
This system requires minimal training for the driver; they simply flip a switch at the right time and let the system do the work.
“Assuming that the driver is rolling at a reasonable speed, say, 10 to 15 mph, you don’t want to be going too fast because then the spray will not coat the tires well enough,” said Medemblik. “Typically, the driver would apply the spray approximately one-quarter mile from the entrance to the farm. It takes approximately two minutes to coat the tires.”
Full body sanitation
The wheels of feed trailers are in constant contact with the dirt and dust that can carry the pathogens that lead to outbreaks, so dousing them frequently will offer preventive if not complete measure. As the scale and potential economic repercussions of biosecurity threats increase, more complete solutions are being offered like those by Hydro-Chem Systems, Inc., a relative newcomer to the animal agriculture industry.
“A year and a half ago when H1N1 sprung up, all of the sudden we found ourselves at the forefront of having technology that could automate the process of sanitizing trucks, and do it in a way that was cost-effective and efficient,” explained Scott Harmsen, director of business development, Hydro- Chem Systems, Inc.
Depending on a consumer’s need, there is a wide range of solutions for full truck sanitation, from simply adding a sanitizing step to an in-place truck washing system, to a fully automatic biosecurity wash system.
“We believe the clean vehicle is the best thing to start with before you put a sanitizer on it, because if you put a sanitizer on dirt, that’s probably not going to be as effective as if we have a clean surface to work from,” Harmsen said. “We prefer to sell the full biosecurity, but we do have a sanitizing arch option only for those fleets that are maybe washing them another way already or aren’t finding they have that much dirt on them.”
These systems are quick, easy and approved by the US Environmental Protection Agency in each of the states they are currently operating.
“A truck can get through the system in two and a half to three minutes, and it’s usually done for under $5,” said Harmsen. “Now if you had just a sanitizing arch, where it’s not the full biosecurity, you’re running through that in less than a minute and you’re doing it for less than a couple of bucks. Our system will do the complete undercarriage of the vehicle, all in the wheels, around the wheel wells and everything, so it [offers] more comprehensive coverage of the vehicle and is done more quickly for less money.”
More to come
No matter what system works for an individual operation, expect more attention to be paid to every step in the biosecurity plan, as companies look to close up holes and avoid massive losses. The industry as a whole wants solutions, and advancements will continue to be made until they are achieved.
“Our most recent addition of the Full In Cab HMI operating system is really starting to catch on,” Medemblik explained. “That system monitors the performance of the unit while also allowing the driver to fully operate the unit without leaving the seat of the trailer. Additionally, we have been spending more time on developing better cleanout of the unit. As we continue to see the drive to ‘full quarantine’ or ‘complete secure sites,’ we definitely see more requests for better disease control.”