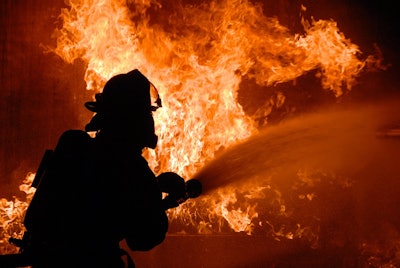
The grain handling industry is a high hazard industry where workers can be exposed to numerous serious and life threatening hazards.
According to the Occupational Health and Safety Administration (OHSA), these hazards include fires and explosions from grain dust accumulation, suffocation from engulfment and entrapment in grain bins, falls from heights and crushing injuries, and amputations from grain handling equipment.
Valuing workers’ safety and well-being are crucial for a company’s success, particularly within a potential dangerous environment such as grain handling.
Installing the proper equipment in bins, hoppers and silos is the first step in reducing the risk of accidents caused by entrapment and explosions, as well as following proper safety procedures.
Here are several steps to consider:
1. Dislodge dirt and keep airflow moving within dust collectors. Grain dust explosions are a serious occurrence. These explosions are often severe, involving loss of life and substantial property damage.
Over the last 35 years, there have been over 500 explosions in grain handling facilities across the United States, which have killed more than 180 people and injured more than 675, according to figures from the OSHA.
Grain dust is the main source of fuel for explosions in grain handling. Grain dust is highly combustible and can burn or explode if enough becomes airborne or accumulates on a surface and finds an ignition source (such as hot bearing, overheated motor, misaligned conveyor belt, welding, cutting, and brazing).
OSHA standards require that both grain dust and ignition sources must be controlled in grain elevators to prevent these often deadly explosions. Applying vibration to your dust collectors can offer the proper dust dislodging technique to reduce the risk of explosions and help provide better safety for your crew.
Equipment such as vibrators, rappers and knockers that can extend the life of dust collection equipment, keep it running at optimal efficiencies and improve clean out processes.
These benefits all add up to a reduction in maintenance and materials, higher production rates and less dust in the work environment. These products are ideal for electrostatic precipitators, bag houses, cyclone collectors and collection hoppers.
For example, Cleaveland Vibrator Company offers the CVC Model PMA specifically designed for dislodging dust collected in an Electrostatic Precipitator. The tapered mount design conforms to most shaft and adapter designs currently in use, while the piston and bore design produce higher frequency and force which uses less air. Vibra-Might vibrators or SI air knockers keep collection hopper walls clean to ensure smooth flow of fine particulates to the feeder or discharge for total clean out.
2. Choose proper location of dust collection equipment. Keep in mind that all filter collectors that have been installed after March 1988 should be located outside of your facility. This will help to reduce explosion hazards. If your piece of dust collection equipment is within the facility, it should be protected by an explosion suppression system.
3. Use appropriate vibratory equipment for grain storage bins. Suffocation is the leading cause of death in grain storage bins. It takes five seconds or less for a worker to be completely engulfed while they are trying to unclog the “bridged” grain. The behavior and weight of the grain creates a quicksand-like rotation, making extremely difficult for a worker to escape without assistance in many cases.
"Bridged" grain and vertical piles of stored grain can also collapse unexpectedly if a worker stands on or near it. The behavior and weight of the grain make it extremely difficult for a worker to get out of it without assistance, according to the OHSA. The pressure of engulfing grain is so powerful, it takes more than 1,500 pounds of force to free a body submerged under less than two feet of grain.
Using an air piston vibrator, such as Cleveland Vibrator’s VMSAC or SI Single Impact Air Knocker, on the side of your storage bins can help reduce the need for bin/hopper entry. The VMSAC units offer a wide range of vibration intensities while the dual diameter piston allows for mounting at any angle on your bins, chutes and hoppers. These vibrators can handle material loads from 200 lbs to 100+ tons.
The single impact pneumatic vibrator or "air knocker" delivers one impact at a maximum frequency of once every three seconds through a five-port spool valve. A timer is used to vary the impact cycle required. Single impactors or "air knockers" act most like a hammer and are most effective for sticky materials because they are less likely than continuous vibration to cause packing in bins and hoppers
4. Power down any excess equipment associated with bins. OSHA Standard 1910.147 Control of Hazardous Energy states that all powered equipment must be turned off and locked out prior to entering the bin. Whether it is pneumatic, electric, hydraulic, or mechanical, any piece of equipment that is moving grain heightens the chances of engulfment. That’s because the equipment can create a suction of the material, pulling your worker into the grain in the matter of seconds. Always LOTO (Lock out/Tag out) unloading equipment and other energy sources before entering a bin.
5. Provide all employees with a safety harness. Flowing grain is the MOST DANGEROUS. It acts like quicksand. It continually flows to fill in holes. The flow creates a suction to pull you under, according to the Grain Handling Safety Coalition. The faster grain flows the faster you become submerged. Grain only needs to remove the body volume of a person to completely cover you.
The average body volume is 5-7 cubic feet. It can take as little as five seconds to become totally engulfed. An average 10-inch auger unloading at a rate of 4,086 bushels per hour will completely engulf a person in less than 60 seconds, according to the coalition. A safety harness should be connected to a lifeline and employees must wear this harness when the need to enter a bin should arise.
6. Implement Preventive Maintenance Programs. Be sure to regularly schedule inspections of your mechanical and safety control pieces of equipment. Using equipment that is not up-to-date with current safety codes can prove to be a critical mistake which makes the odds of an accident greater within your facility. Cleveland Vibrator can provide field tips and also evaluate your vibratory drives or equipment.
Finally, check your tools to make sure they are in good working order which includes inspection of the guards; make sure you have no frayed electrical cords. Generally, this is just good work ethics in any work environment.
Safety doesn't happen by accident. There are precautions that can be taken in the grain handling industry to minimize the safety hazards around the bin. Awareness is key.
This article was written by Katy Sabo, Marketing Communications Manager, for Cleveland Vibrator Company, Cleveland, OH. She can be reached at 216-241-7157, ext. 245, or email at [email protected].