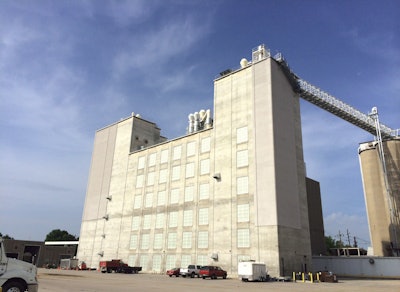
Here’s a riddle. What covers nearly 90,000 square feet, is located just minutes away from one of the top 15 metropolitan U.S. cities, yet almost no one outside its rural home community knows it exists?
Got it? The answer is Archer Daniels Midland Co.’s Beech Grove, IN, wheat milling facility — the third largest flour mill in the nation. ADM brought its newly constructed C mill online in May, adding flour milling capacity of 8,400 hundredweights (cwts)/day inside a 30,000-square-foot, six-story production facility.
“The mill is tucked away off the road in a great spot where a lot of people can’t even find us,” shared Jeff Stephens, commercial director, ADM. “So, we’ve got one of the largest flour mills in North America, sitting a couple miles from downtown Indianapolis, but so many people don’t know we’re here, which is really fascinating when you see the size of this facility.”
ADM purchased the mill, originally located in downtown Indianapolis, from Acme-Evans in 1988 and moved to Beech Grove in 1992.
Beech Grove, IN, is a small community within Indianapolis offering all the benefits of a metropolitan area, without the inherent logistical transportation challenges of an urban location.
“Where we are now is very conducive to doing business,” said Stephens. “When you look at Beech Grove and its proximity to major metropolitan areas, we’re in a great location to access the railroads and the interstate system.”
The Beech Grove facility mainly supplies commercial bakers in Indiana, Kentucky and Ohio with various spring, winter and soft wheat flour blends.
It also markets wheat middlings, a byproduct of the flour milling process, to local dairies and beef producers for feed.
The original Beech Grove mill consisted of two identical A and B mill buildings and served the company’s needs for more than 20 years, but as their customers’ businesses grew, management knew the current mills wouldn’t be able to meet the increased demand. With an ideal location and room to grow, ADM seized the opportunity to expand the Beech Grove flour milling facility.
“Senior management, along with regional personnel, continued to see the organic growth of our customers,” said Stephens. “It would not have been possible to grow with them without this expansion. We set to work four to five years ago and executed a thorough plan to size the mill.”
The plans ultimately included a 30,000-square-foot concrete slip form building outfitted with new, fully automated milling equipment and process controls, along with three bridge structures, provided by contractor Todd & Sargent, Inc.
“The new flour mill and state-of-the-art equipment increases milling capacity by 8,400 cwts/day [381 metric tons] and increases our loadout capacity of flour nearly 100%,” said Stephens. “We also added over 31,000 cwt of flour storage, including eight additional fast load out flour bins. These sizable increases will help us serve our customers and allow us to grow with them as their demand for flour increases.”
Construction considerations
Crews began construction in January 2013, and the facility was finished and operational by May 2014. Todd & Sargent’s key projects included grading, foundation work, slip-forming the building and erecting an overhead conveyor system.
Despite the magnitude of work that was required, ADM’s commitment to customer satisfaction meant it couldn’t halt wheat milling production for construction.
“Our contractors understood from the very beginning that we could not allow a project of this magnitude to negatively affect service to our customers, and it did not,” said Stephens. “ADM is grateful for the efforts of the project contractors, the transportation companies and the management team at Beech Grove who made sure service was not compromised.”
According to Clint Steele, vice president of marketing, Todd & Sargent, Inc., the facility only experienced downtime when electrical connections were made from the original facility to the new building.
To keep wheat receiving and milling operations running smoothly throughout construction, the project managers isolated the work site by erecting a temporary chain-link fence.
This helped direct traffic flow around the site and provided a safe area for construction workers by securing the location.
The fact that Beech Grove is a food production facility brought another set of considerations to the project.
Cleanliness of the construction site was as important as cleanliness on the production floor, according to ADM’s guidelines.
“During construction of the new building, keeping contractors aware that they were working to safely build a food-grade mill was something we took very seriously,” said Stephens. “Laying the groundwork for this behavioral shift was the initial orientation that all employees received when they arrived on-site. The most influential tool was the front line supervision, and holding employees accountable for keeping their areas clean, sanitary and up to ADM’s standards.”
Value engineering
Just as the heart needs clear arteries to deliver blood, the connection between the A, B and C mills was vital to give facility personnel and product an easy passageway from the old to the new structures.
The highly automated facility requires only one operator in the control room, who may need to quickly move from one side of operations to the other, so engineers designed a third-story personnel bridge.
A conveyor system constructed above the top of the building provided a cost-saving materials handling solution to bring wheat into the mill and send wheat midds to existing feed storage bins.
“ADM wanted to use the existing wheat storage bins for the C mill to get a bigger return on investment, so we found a way to use them to bring wheat over and also to return the midds,” Steele began. “Building one bridge and a conveyor are much more economical than building new silos. We brought a lot of value engineering with this idea, and ADM’s management were very happy with the end result.”
Steele was quick to note, however, that engineering this mammoth facility was not a solo endeavor.
ADM, Todd & Sargent and equipment manufacturer Bühler Inc. worked closely together on the project. ADM provided the scope for the new mill, while Bühler designed the 381-metric-ton mill with complete cleaning house, mill, storage and load out system.
Todd & Sargent designed the foundation, the structure, and engineered the building slip form and the installation as well as installed the milling equipment with the assistance of a Bühler installation supervisor.
“We are proud of our working relationship with both Todd & Sargent and Bühler,” Stephens said. “The three companies had one objective — to safely construct a state-of-the-art flour mill and that is what we did.”
Automation leads to customer satisfaction
The ADM-Beech Grove facility is fully automated from wheat receiving through bulk flour load out and everywhere in between.
The wheat is delivered to the mill from an elevator with flow rate controlled through automation. Before initial cleaning, the wheat is processed by a state-of-the-art color sorter.
This piece of equipment uses cameras to identify stones and undesirable color characteristics for quality control. The color sorter removes undesirable wheat including broken and shriveled kernels and grain other than wheat.
Then, the cleaned wheat is sent to the tempering system, which adds water to prepare the wheat for cleaning by toughening the bran and mellowing the endosperm. The bran is removed and the endosperm is reduced into flour during the milling process.
After tempering, the wheat is processed into flour using seven double-high roller mills and nine single-high roller mills. The flour is produced to meet customer specifications.
The new mill is equipped with Buhler’s Yield Management system that precisely weighs production.
“The load out system monitors the rate at which flour is transferred from the storage bins to the load out bins,” said Stephens. “Enrichment, malt and LA Novadelox® [a flour bleaching agent] are accurately applied by loss-in-weight ingredient feeders.”
The finished flour goes into one of 11 storage bins, which feed multiple conveyors to the eight new (216-metric-ton total) fast load out bins, or to existing bulk or packing storage in the A and B mills.
It takes 16 minutes to fill a 50,000-pound truck with flour from the time it pulls up until it leaves the facility. Much of this time is spent setting the truck up for load out.
Setting priorities and objectives
Having a safe work environment for employees and keeping the mill clean are two of ADM-Beech Grove’s top priorities.
“And they go hand in hand,” Stephens said.
For example, Stephens said production issues in most mills today can create large spills — what are referred to as chokes.
“Flour chokes are unproductive,” he started. “There is a lot of cleanup and product loss involved. In the new mill, production issues will cause it to go into suspension, so it will continue to run without choking down and causing spills. The automation and equipment allows us to keep the mill cleaner and follow our food safety guidelines.”
When it comes to setting priorities, ADM is clear in its intentions. Mark Kolkhorst, president of ADM Milling, summed up the Beech Grove expansion’s objective at the facility’s opening ceremony. “All the improvements we’ve made were designed with three things in mind: efficiency, sanitation and quality.”
Through a cooperative team of engineers, state-of-the-art equipment and quality construction, ADM-Beech Grove achieved its three goals and then some.
The giant mill may be off the beaten path, but its presence is felt throughout the region.
From the farmers who supply wheat to truck drivers and the mill’s employees to commercial bakers and livestock producers, the ADM-Beech Grove facility provides hundreds of individuals employment opportunities and gives companies easy access to safe and sanitary wheat products.
“We enjoy being in Beech Grove, we have a great relationship with the local community, and we look forward to being here for years to come,” Stephens said.