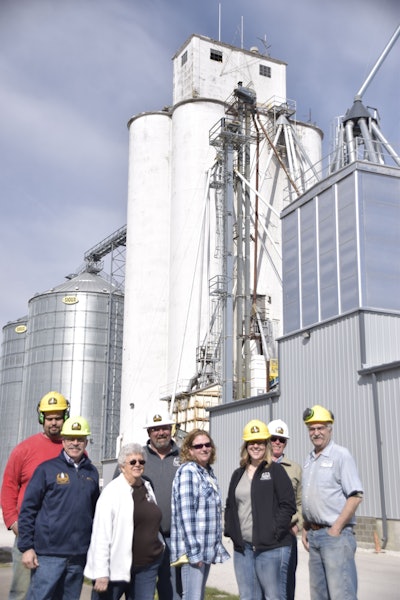
Farmers Exchange and Elevator Co. of Monroe City, MO, is approaching a milestone: 100 years of service to the community that it was founded in and the generations of farmers that have relied on it through good times and bad.
The cooperative has continuously adapted to its customers over the past century, but after an F2 tornado swept through the small community in 2006, the company’s perseverance and compassion were tested.
Twelve years later, Farmers Exchange and Elevator Co. has become stronger than ever, with increased profits and a $3.5 million expansion to its feed mill that has once again aligned it with its customers’ needs.
1919 to 1960
A Certificate of Incorporation was awarded to Farmers Exchange and Elevator on June 6, 1919. A year later, it became a cooperative. During the first few decades, the company focused on meeting its customers’ needs, offering services members required and could be accomplished at the site. In addition to grain storage, the site hosted a stockyard, marketed produce and even dealt in wool. “I think they did about anything their members needed and they could make a buck on,” explains Marlin McCormick, general manager. “Most of the employees were hard workers, and they were located on the rail. So, they dealt in anything they could unload or load onto a railcar. Life was hard. Work was tough.”
Farmers Exchange and Elevator started making feed in the ‘40s, mixing for brands like Purina, Wayne Feeds, Critic, and eventually Farmland Industries. During that time, it also mixed its own brand, MC Pride.
In 1960, the company built the concrete grain silos that still tower over the campus today. While the silos are still operational and have held up well in their almost 60 years of service, the $160,000 price tag and 250,000-bushel storage raised some eyebrows in the community when first proposed.
“People in the community said the silos were too big and would never be needed,’” says McCormick. “At the time, 250,000 bushels of space was just huge.”
The company continued to adapt to the needs of its customers through both lean and prosperous years, but the cause of the next wave of large-scale investments can be linked to one tragic event.
Tornado
On Sunday, March 12, 2006, the state of Missouri experienced 72 tornadoes. An F4 tornado spawned in Monroe county and made its way toward the small community bearing the same name. It had weakened to an F2 by the time it hit town, but the damage was substantial to anything in its path, including Farmers Exchange and Elevator Co. That night, after the tornado, McCormick went to the co-op campus to survey the damage.
“When we first arrived, we thought everything was okay until we saw the backside — the whole back of the building was gone,” McCormick recalls. “We pulled our vehicle up to the front door, and used the light from the headlights and flashlights to gather everything left in the office that was needed to run the business. We worked until 3 in the morning, only leaving when the police told us we needed to because there was another line of storms coming.”
The next day was Monday, so after a sleepless night of gathering what they could, it was time for McCormick and management to head back to the mill and address the workers whose livelihoods had been scattered. The company started with surveying the damage and working to keep its obligations fulfilled.
“We just started putting things together one at a time. First, we sent employees out to survey the campus, then contacted our customers,” says McCormick. “We were doing some business with Cargill and a lot of business with Land O’Lakes at the time. Luckily, Those corporate mills could handle our orders for us until we were able to get power back on at the feed mill three days later.”
McCormick is still thankful for the reaction he got from the company’s employees, customers and the community.
“Everybody just came together — the whole town,” he explains. “A lot of our customers helped us clean up the mess, then suddenly, it was time to go to the field, and we were able to start dealing with reality again.” Looking back at the tragic event, the tornado was a pivotal point for where Farmers Exchange and Elevator is today. “It made us stronger,” says McCormick. “The tornado didn’t destroy any of the income generating properties of our business. It took our office and warehouse out, but we got through that. The tornado gave us an opportunity to clear the slate, to think about what we wanted from our facility.”
Going all in
Since the tornado, Farmers Exchange and Elevator has been making incremental updates and expansions to its campus, starting with a new office and storefront, additional warehouse space and more grain storage.
The management team realized there was additional opportunity on the feed manufacturing side of the business, because of the relationship they had with their customers.
“This mill’s opportunity lies in giving our local co-op customers a place to market their grain without having to drive 30 miles away,” says Ron Dean, livestock consultant. “The main point to building this feed mill expansion was either going into feed with both feet or just rolling backward,” explains McCormick.
But any expansion would first have to overcome a major roadblock — space. Farmers Exchange and Elevator is located on a narrow strip of land nestled between a city road and a rail line. There is little room to add a building without demolishing another, and the land around the elevator is either owned by the town or railroad or is residential property. If the company wanted to stay in the same location they were founded at almost 100 years ago, they would have to get creative.
“We started interviewing potential suppliers of equipment and services in 2014, even inviting a few here to take a hard look at our place,” says McCormick. “Some of them just ran as fast as they could to get away from us. Some only wanted to work on a new facility.”
A new facility was not an option for the co-op, and the team had to figure out how to build on the land they had. Poepping, Stone, Bach & Associates, Inc., Quincy, IL, helped devise a solution for the limited space available for building. After years of research and planning, the team got approval from the co-op board in November 2016 and got to work.
“We didn’t have much space so we were forced to build high and low rather than side to side,” says Dean. The strange building conditions were not the only issues millwright Industrial Enterprises Inc. of Mid Missouri, Jefferson City, MO, worked around. A high water table and a need to keep the current portion of the mill running during construction played large roles in how the new portion of the mill was built.
“We were moving tanks around as we dug the holes that would house our mixer and other equipment,” says Dean. “We would kind of just move things slightly to the side of the hole to dig, that way we could stay operational during the project.”
The hardships paid off when the advantages of a modern mill revealed themselves to the mill management, employees and customers.
A major upgrade
The mill has never had much storage for finished feed on site. The realities of modern livestock farming, primarily swine raising in this instance, mean that different formulas of feed are needed for different breeds, growth requirements and nutritionist recommendations.
It’s easier for Farmers Exchange and Elevator Co. to mix the feed a customer needs rather than predicting what he or she will want. A large micro-ingredient system with 24 bins and tote bag system from Easy Automation, Inc., Welcome, MN, makes that process simpler and faster for the co-op.
A new automation system from Easy Automation Inc., a set of eight 12-ton loadout bins and a 65 ton/ hour mixer from Scott Industries, Inc., New Prague, MN, has allowed the mill to exponentially improve the load-time of trailers. “The old mill was taking about 50 minutes to load a trailer full of feed,” explains McCormick. “Now we can make 96 tons in 90 minutes and fill a trailer in six minutes.”
Speed is just one of the many modernizations of the mill expansion but not every improvement focused on increasing productivity of the mill. Heated workstations, a bathroom in the mill, and better ventilation are all focused on increasing the productivity of the employees in the mill. These features also focus on bringing to the forefront the people that are the company’s most important asset.
Farmers Exchange and Elevator Co. survived through World War II, the Great Depression, and countless other large and small calamities by pulling together as a company and community. The new mill expansion will serve as a capstone to the company’s first century of existence and readies it to continue to serve its community for another 100 years. ❚