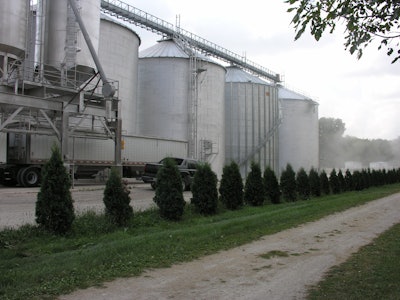
To avoid grain entrapment, stay out of stored grain. Oversimplified? Given all of the variables — probably. Yet, “There’s a direct correlation between grain entrapment incidents and out-of-condition grain,” emphasizes Professor Bill Field, of Purdue University’s Agricultural Safety and Health Program. Simply put, “when you maintain stored grain quality, safety improves.”
Since 1978, Purdue has documented grain entrapment cases — both on-farm and commercial. In 2010, the number of entrapment incidents spiked at 57. “It was directly related to the 2009 crop quality,” Field comments. In 2011, there were 30 incidents. In 2012, it dropped to 19. Unfortunately, this doesn’t suggest a downward trend. Though still unofficial, it looks like 2013 could come in with as many as 30 incidents. The chart on pg. 23 shows that through 2012, the five-year average remains above 35. About half of those trapped in flowing grain don’t make it out alive.
Quality, because it is more controllable, is a key focus, but other aspects may be contributing to increased entrapments and deaths. First, Field says, we have more storage, both on-farm and off. Second, we move a higher volume of grain off the farm and across the country. Third, consider changes in the agricultural labor workforce. “More and more employees don’t come from a grain handling setting and they simply are not familiar with the risk.”
Emphasizing that he sees more companies focused on safety, including some with zero tolerance policies on confined space entry, Field points out that “only about 5% of facilities are OSHA inspected.” This is not to suggest operators consistently ignore safety steps, “but with all of the factors we face in storing grain, we have to keep working on education and awareness of the potential hazards and how to stay safe.”
The compounding effect of poor quality
With 32 years of grain management experience and direct responsibility for six elevators, Bob Marlow has taken a strong stance on the grain quality/facility safety issue. Marlow, Central Region Operations Manager for The Andersons, used one of his facilities in cooperating with Purdue University’s field studies to analyze the quality/safety relationship.
Like Field, Marlow pays attention to the safety data and the causes of incidents. “The single leading factor that contributes to entering stored grain is that something happened to affect the grain quality resulting in slow or no discharge. In most cases, it’s not an equipment issue. The sump is plugged, fines have compacted and restricted flow …. most engulfment tragedies are a result of someone trying to unplug a bin when grain can still draw down,” he says.
It’s not that people don’t understand or recognize the OSHA requirements to help prevent these tragedies, comments Dave Laing, general manager of Mole•Master Services Corporation, a company providing equipment and bin cleanout services. “Too often, procedures are skirted — not followed to the letter of the law. Lockout/tag-out, harness requirements, air monitoring and respirator equipment requirements are all there” to help guide and protect people.
Proper equipment and training are essential for appropriate entry. Still, Laing says, grain managers can run into a host of problems with which they are not familiar. “We have supervisors who have been cleaning bins since 1984. We’ve been on thousands of jobs across the U.S. and many countries. You’d think we had seen it all, but we still uncover new problems.”
And while grain quality management is key to avoiding problems, there are other variables, “such as someone forgot to close a hatch and it was open during a rainstorm.” That human component may never be eliminated, but the majority of issues they see relate to grain moisture and cleanliness. “We’ve cleaned bins with tons of material that is hard as rock, bins with layers of grain that look like OSB board,” he says.
Grain quality problems have a compounding effect, Marlow points out. For example, you’re under the gun of a fast harvest. Some grain comes in too wet; some is high in fines. You crank up the heat on the dryer to keep grain moving, but that can lead to increased BCFM. The smaller particles restrict airflow through your bins. Aeration and cooling are less effective than needed, you get mold and hot spots, fines settle and compress, resulting in crusts or bridging that restricts or stops material from flowing.
Laing and his crews view this compounding effect as Low, Medium and High Degree of Difficulty. Low Degree issues typically are solved with a whip machine. “If there’s a small amount of build-up, a rathole, poor flow, you can get those out with relative ease,” he says. As problems compound, the rathole gets smaller or completely restricted, you may need a drill and definitely more expertise to create a flow channel; you have to get material flowing. He draws an analogy to humans: When blood vessels are free and clear, everything works. The greater the restriction, the greater the problem — and the High Degree of Difficulty label. “We’ve seen situations where the material is almost one solid mass within the silo,” he says. These situations require expertise to safely get product flowing or removed. “Your goal is to keep people safe, always, while you work to minimize any damage that might be done to the structure and hope you can salvage the grain or material,” he adds.
Putting a quality management process in place
Problems are best avoided, Marlow suggests, by following a process that keeps bins and grain in proper condition. “We don’t often have the luxury of time (during harvest) to handle grain more slowly. Because you can’t always eliminate the risks when you put grain into storage, it’s important to recognize that you’re likely to have conditions that can lead to problems, and you need to go back and address those needs.”
Marlow follows SLAM, a process detailed by Purdue to help ensure grain quality. SLAM is:
S = Sanitize, Clean, Seal
L = Load, Screen, Level, Core
A = Aeration
M = Monitor
The “S” is best when the bin is empty. Clean aeration ducts, piping and under bin floors. Seal all openings around the roof, sidewalls and ducts. Clean conveying and handling systems from all old crop carry-over. To keep insects at bay, have residual insecticides applied by professionals. Marlow recommends whenever possible to inspect and test monitoring systems, replacing any inoperable cables.
“L” can take place while filling or after the bin is filled. “If possible, clean the grain before putting it in storage,” he says. “When you fill bins, fines accumulate in the center and the heavier free-flowing material goes to the outside. Coring will alleviate that issue. Because it’s not always feasible to core while storing, that’s often the step used to ‘go back and address potential problems.’ It’s best to “move the material when it is still in free-flow,” Marlow says. “If it’s high in fines, for example, we’ll pull from the center of the bin, sample it going out, clean it, sample it again, and then we can re-introduce the cleaner product back into the bin or move it to another bin. On a half-million-bushel bin, we may move 25,000 to 35,000 bushels.”
Time and expense? Yes. But if it helps you keep people from having to enter a confined space, it is a worthwhile investment.
Aeration, monitoring and management
Their goal for aeration is to “cool as much grain as quickly as possible,” Marlow explains. They work to make sure all the temperature cables are operating and use the monitors to help them cool grain into the mid 30 degrees over a few months. “We cool — aerate — grain to get to the temperature we want, then seal the fans.” Their target is to hold grain at 25 to 35 F. As weather warms or fluctuates, they run roof vents to move warm air out. The roof vents can be thermostatically controlled, which eases the need to monitor outside air temperatures. And, when carrying cold grain, running “even a small fan can reduce the heat in the headspace of the bin due to ambient temperatures in warmer months,” helping you avoid condensation issues.
Monitoring systems give you a heads up on potential problems. Along with temperature and moisture monitors Marlow advocates using CO2 monitors “CO2 is a leading indicator of some level of activity within a bin. It disperses so you can’t identify where the grain is spoiling, but continuous high readings show you something is going on with grain quality.”
Temperature cables help identify hot spots except, Marlow points out, grain is such a good insulator it’s almost impossible to have enough cables. In their 114-foot-diameter welded steel bins they will have 24 cables, leaving gaps where quality issues won’t be detected. “Testing for CO2 —which we also do in temporary storage — is important because it shows that you’re getting spoilage that might not be picked up by a temperature monitor” and lets you take action to keep grain conditioned. The Andersons will also transfer and sample grain, sample at load-out, check for odors and, with two trained people, open hatches to visually inspect stored grain if a problem is noted.
Because quality and safety are so interconnected, Kevin Miles, president of Rolfes@Boone, says more grain facilities are installing kanal systems in existing tanks and most new structures designed are built with a kanal system. “A well-designed kanal system can help you empty a tank down to a bucketful of grain. They support better aeration and cleanout; you don’t need a sweep auger; and it eliminates the need to enter a bin,” he says. Some will consider these systems “pricey,” but reduced mechanical problems, better cleanout and improved safety provide return on investment.
Rolfes@Boone manufactures aeration, dust control, and temperature and hazard monitors, working with grain facilities across the country. Miles typically sees people shut off fans too quickly, “which can create buffer zones where cold grain sits next to warm grain. You’ll see crusting and hot spots — it can lead to a host of problems.”
To consider how aeration works, think of a garden hose. The adjustable nozzle lets you water with a broad spray or switch to faster, narrower streams. With aeration, you only want that broad “misting” of air that moves slowly and spreads evenly through the grain mass. If aeration isn’t functioning properly, crusting and channeling can occur. “Air flows around those areas rather than through them,” Miles says.
If a fan needs to be replaced, replace it with same horsepower rating. “We’ve seen situations where a higher horsepower fan was used as a quick replacement. But when you move air too fast, you get a narrower stream, which can lead to quality issues. You want to keep the air front dispersed and moving up through the grain and out the top.” Because air at the top will be wetter, consider running exhaust fans for an extra hour or two to dry out head space when ambient temperatures fluctuate. Powered roof vents should move 1.3 to 1.5 times the airflow coming in at the bottom of the grain mass, Miles says.
Recognize the differences in moisture and fines in each structure and know the cfm recommendations for the bin, he reminds.
Quality in equals quality out
Look at it this way, suggests Dave Crompton, founder and CEO of OPI-integris: “As a grain manager, your key focus is to get the most value from that grain asset.
When you properly manage grain, you can optimize its value while reducing risk and increasing safety.” Crompton’s company sells products and systems that monitor grain moisture, temperature, insect levels, and can automate the aeration and ventilation system for commercial grain and producer customers.
A modern grain management system and trained operators work hand-in-hand for safety and value, Crompton says. “All the information you need is being measured — the data is coming to you. It should keep people from going inside a bin.” He recognizes, though, that new facilities are more inclined to invest in technology. “If someone is putting up a new bin, we see much greater acceptance of investing in technology to help store grain at the right moisture, hold grain quality as best you can.” The ROI, in addition to lowered risk, can include reduced energy and labor costs, along with less spoilage and shrink.
There is a “significant infrastructure of pre-existing storage, monitoring and conditioning systems where full capitalization for replacement isn’t likely to happen. Some investments can be made on a more ad hoc basis,” to increase the amount of data captured.
“But some older facilities will remain older — with no updates. These require constant attention and awareness, and have increased risk as a result. With a system that delivers accurate data and supports grain management, you are more likely to get the same quality of grain coming out of the bin as went into the bin. And with that there is no reason to have people in the bin.”
Professor Field agrees that older structures will require more diligence, regardless of who owns them. “We see some older satellite facilities used for temporary storage” that might not receive consistent attention. “And there are instances where we’ve seen the transfer of older, smaller properties to farmers, and these facilities are exempt from OSHA requirements. This is why we think it’s so important to carry the safety message throughout agriculture.”
Purdue has piloted safety classes for young and beginning workers in agriculture, working to teach basic awareness of grain management, bin entry risks, personal protection and OSHA regulations in place and why they are in place. It’s a start — and it’s sorely needed. “Sometimes, it’s hard to believe what people will do,” Field says, from poor bin design and construction to continuing to walk down grain to sending someone in with a pickaxe to knock crust off the bin walls while grain was flowing — and many others. Granted, much of this occurs on farms, but commercial facilities still have risks and see tragedies.
Marlow says the “quality and safety message require constant attention,” and should include producer customers. Discussing on-farm grain quality management with growers improves value for them and the elevator, and contributes to keeping people safe and out of stored grain.