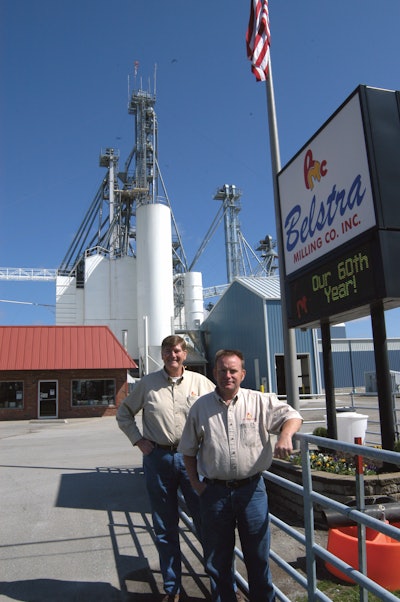
In 2010, Tim Belstra says it became clear that several of their 1960s-era grain bins needed upgrading. Certainly, over the 60-year history of Belstra Milling Co., Inc., equipment upgrade and replacement has been an ongoing exercise.
But this time, the question of what to do with the bins turned into a broader discussion. “Those tired bins sparked a conversation about what we wanted this place to look like,” recalls Belstra, chairman of the DeMotte, IN, milling company. “Our motto became, ‘Let’s plan for the next 20 years.’”
Continual evolution has gone hand-in-hand with Belstra Milling’s growth. Started by Tim’s father, Bud, in 1954, the mill’s operation has reflected the changing livestock scene in northern Indiana. As the trend is most everywhere, livestock operations have consolidated. Belstra Milling now serves a large hog population (see sidebar on pg. 14), and dairies have become significant customers with an estimated 40,000 head in their market area. It was this combination of factors, including the changing livestock base and their confidence in the growth of the livestock market in their region, that pushed Belstra and his team to embark on a formal upgrade plan, with the final step — a brand new packing system —completed in April 2014.
The master plan
The foundation had been set in 2010 when Belstra Milling engaged the consulting services of Sunfield Engineering, Inc., Cedar, MI, to develop the master plan for renovating the facility. Sunfield’s owner Dick Kobetz and his business partner Kay devised an integrated master plan for the mill that identified the steps needed, categorized into three phases: grain receiving and traffic flow; ingredient receiving; and packaging, depackaging and warehousing.
“They did this right — by the book,” Dick says. “We had clearly defined steps, and they followed through completely.”
The work was performed in three phases, using an owner-directed approach to the construction.
“We performed the detailed design and engineering, then turned it over to them. They managed and directed the construction,” Dick says.
“These renovations have given them more capacity, it’s made them more flexible in the feed they can make, it has improved their accuracy, and it has increased overall product quality.”
Phase 1: Traffic flow
The priority from the initial plan was improving overall traffic flow at the facility.
Specifically, one lane and one scale handled virtually all traffic, from inbound corn and ingredients to load-outs of finished feed.
“It was a huge bottleneck,” says Mark Zuchowski, special projects manager at Belstra Milling, who has led the overall process and facility improvement initiative. Not only were trucks jockeying for position as they went back and forth through the lane, but they were crossing paths with retail customers visiting the farm store.
“Semis and people don’t mix very well,” Belstra notes.
Their Phase 1 of the plan was to set up one-way traffic flow and have purpose-specific lanes.
Prior to the reflow, all trucks entered and exited from a highway running east and west in front of the facility. By accessing land Belstra owned immediately east of the mill, they established an “in” drive from a road running north and south alongside the property. This allowed all truck traffic to become one-way, in from the east and exiting to the south, and greatly improving efficiency and safety.
Two more lanes were added, to give three purpose-specific lanes.
The original lane was designated strictly for feed load-out. The center lane was setup for ingredient receiving and rolled corn load-out. A third lane was set up exclusively for grain receiving.
This new setup is vastly more efficient, thanks to the one-way traffic flow and dedicated scales for each lane.
Overhead storage for rolled corn load-out was increased from 56 tons to 75 tons, and a 10-foot by 70-foot Rice Lake platform scale was installed. In fact, each of the three product-specific lanes have dedicated scales, contributing to the overall improved traffic flow.
Phase 2: Ingredient receiving
With the more efficient traffic and product flow in place, in 2012 Belstra Milling opted to act on Phase 2 of the master plan, ingredient receiving, prompted by the need to replace aging bins.
The increase in Belstra Milling’s dairy business resulted in them handling, mixing and delivering a broader range of rations.
“Hog feed is pretty basic, consistent, but dairy feed is different,” Belstra says. “The dairies are constantly adding and changing ingredients. We had to learn how to warehouse, mix and handle these.”
Belstra Milling’s mixing room draws from 30 ingredient bins of vitamins and minerals, which go to a Scott twin-ribbon mixer.
Dairy feeds introduced the challenge of dealing with feed inputs that are corrosive, abrasive, sticky or dusty. In response, Belstra and Zuchowski began replacing mild steel pipes with stainless steel, and reoriented pipes to eliminate curves. In summer’s heat and humidity, the stickier feeds can coat the pipes, causing plugs.
“We found that elevating dairy feed and dropping it straight down works a lot better,” Belstra explains.
Ultimately, the company’s managers decided that totally separating the handling of dairy and hog feeds would be the best solution.
“We provide 3 to 5 pounds of a dairy cow’s daily consumption,” Belstra explains. “That’s the mineral mix that has the calcium, the soda bicarbonate, the magnesium oxide, the bypass fats, and other similar products. It’s a higher level of mixing the dairies don’t want to handle themselves.”
More effective dust collection
Throughout all phases of Belstra Milling’s upgrade, dust collection was a priority for two reasons, Belstra explains. “We’ve added five dust collectors in an effort to be better neighbors, and to improve employee health.”
Airlanco dust collectors, ranging in capacities from 800 to 12,000 cfm, are located in the grain processing, ingredient receiving, packaging and depackaging areas.
The ingredient receiving and corn rollout lane includes doors that can be closed when unloading high-dust ingredients.
The ingredient receiving phase of the upgrade included a new 9,400-square-foot warehouse for receiving and staging totes of ingredients. The new warehouse is insulated and temperature controlled, including in-floor heating, to help maintain the quality of certain minerals and other feed inputs that are especially sensitive to changes in temperature and humidity.
They installed an in-floor dump and underground conveyor to move ingredients from the warehouse to the feed processing area. As part of their revamping of the traffic flow, they added more space for semitrailer staging. This provides more “rolling storage” with dropped trailers loaded with ingredients. A used yard spotter truck is a recent addition that Belstra says has proven handy for moving trailers.
Phase 3: Packaging, depackaging and warehousing
In April 2014, the company completed its newest addition to the packaging, depackaging and warehousing phase — a Taylor dual auger-fed packer with a Fishbein sewer with tape, and a JEM tote packager. Six 8-ton overhead bins can be switched to feed the toter or bagger.
The packer’s dual-auger system hits the target weight to within a tenth of a pound. All stainless, it will stand up to the dairy feeds.
Dust collection was a priority for this bagging system. “The Taylor packer has the dust-tight spout that inflates and holds the up to completely seal it. There’s no chance for any ingredients or dust to escape,” Zuchowski says.
Standing up to the dairy feeds and improving dust control was the driver for the bagging system, but it will handle all finished feed, as well as ingredients, if needed. New warehouse racks are planned to store the filled bags for better staging and loading into trucks for delivery.
Easing stress with automation
Automation upgrades are ongoing at Belstra Milling. Their most recent change included automating the feed grinding process, including keeping bins above the grinders full, and reclaiming corn.
“We’re looking at automation to reduce the amount of monitoring our employees have to do,” Zuchowski says. “It’s part of our plan to reduce overall stress levels.”
The corn processing and feed load-out systems have received similar upgrades, providing the operators higher levels of visual monitoring and control. Easy Automation has been their primary automation provider. For their latest software upgrades, Belstra and Zuchowski spent a day at Easy Automation’s facility reviewing and selecting graphics for the overall look and feel for the system’s visual interface.
“What you see on the screen is indicative of what we have in the plant,” Zuchowski says. “It’s nice and user-friendly, and well worth [it].”
Avoiding downtime
Throughout the three phases of the facility’s upgrade, Belstra and Zuchowski said they placed a priority on keeping production going. At some stages, this involved producing extra feed ahead of schedule to continue to fulfill customer needs when they knew a short-term interruption was inevitable. This also helped them identify opportunities for redundancy … having alternate systems in place to keep production going in the event of a breakdown or during scheduled maintenance.
Reduce, reuse, recycle
They refurbished and repurposed equipment whenever possible to help keep costs down, and didn’t hesitate to seek out good used equipment. For example, they moved and upgraded existing bins, they recommissioned their roller grinder into their cracker crimper, and they bought two used CPM/ Roskamp Champion 12 x 42 triple pair roller/grinders.
“We’ve always thought longterm,” Belstra explains. “Every day that you turn on a feed mill, you’re wearing it out, so we’ve always invested back into the business. And when those grain bins began to fail, we saw the opportunity to make this whole operation more efficient, and make life better for our employees.”
OWNERSHIP IN HOG FARMS PROVIDES FOUNDATION
Belstra Milling became involved in the pig business by representing the PIC, the pig breeding stock company, in 1983. This relationship led to Belstra Milling establishing a gilt multiplier in 1988.
This has evolved into six individual pig farms near Belstra Milling and is managed by a separate entity, Belstra Group Farms.
Each farm operates as a separate LLC, with investment by Belstra Milling and others. These farms consume the majority of the pig feed Belstra Milling produces. Five of the six farms produce seed stock; two are farrow-to-wean; four are farrow-to-finish. More than 14,200 sows produce some 400,000 pigs annually.
“These farms put a firm foundation under our milling company,” Tim Belstra, chairman of Belstra Milling Co., Inc., says. “The pig industry was changing. People needed genetics, and they needed to improve their feed and facilities.”
Their newest pig farm is named Pig Adventure. Located at Fair Oaks Farms in nearby Fair Oaks, IN, Pig Adventure joins the Fair Oaks Farms’ mission of educating the public about modern farming activities with tours of a working dairy, and now, the Pig Adventure farrowing and gestation facilities.