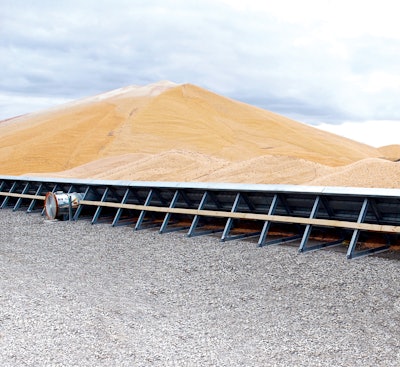
GSI is making it easier for commercial operations to set up temporary grain storage in anticipation of higher capacity demand this harvest season.
Changing marketing patterns are driving that demand, largely as a result of COVID-19, which has led to reduced livestock feed and ethanol demand and a strong incentive to carry grain beyond harvest. GSI offers complete, temporary storage systems that are an effective and cost-efficient way to quickly increase storage capacity and give owners more marketing flexibility.
Ben Althoff, GSI grain product manager, said changes are being made to make the systems easier to install in the field. “We’re doing more preassembly in the plant so that owners just have to flip the legs out and rebolt them,” he explained. “The legs will already be attached instead of having to be manually connected.”
GSI temporary storage systems consist of:
- Patented louvered wall panels that provide optimal airflow to protect grain quality and are configured to the needs of each operation. Wall heights include 3.5 and 6 feet.
- A customizable aeration system to ensure proper airflow during storage. The pipes are made from durable polypropylene pipe for easy on-site handling.
- A full line of tarps that use an integrated strapping system to provide maximum tarp security. A Velcro rain flap protects grain from the elements.
Althoff said GSI temporary grain storage systems can be used for corn, soybeans, wheat, barley, rice, milo and sunflowers. Installation time depends on the size of the system, which can be configured to meet any operation’s need but typically can be completed by the end user in under a week.